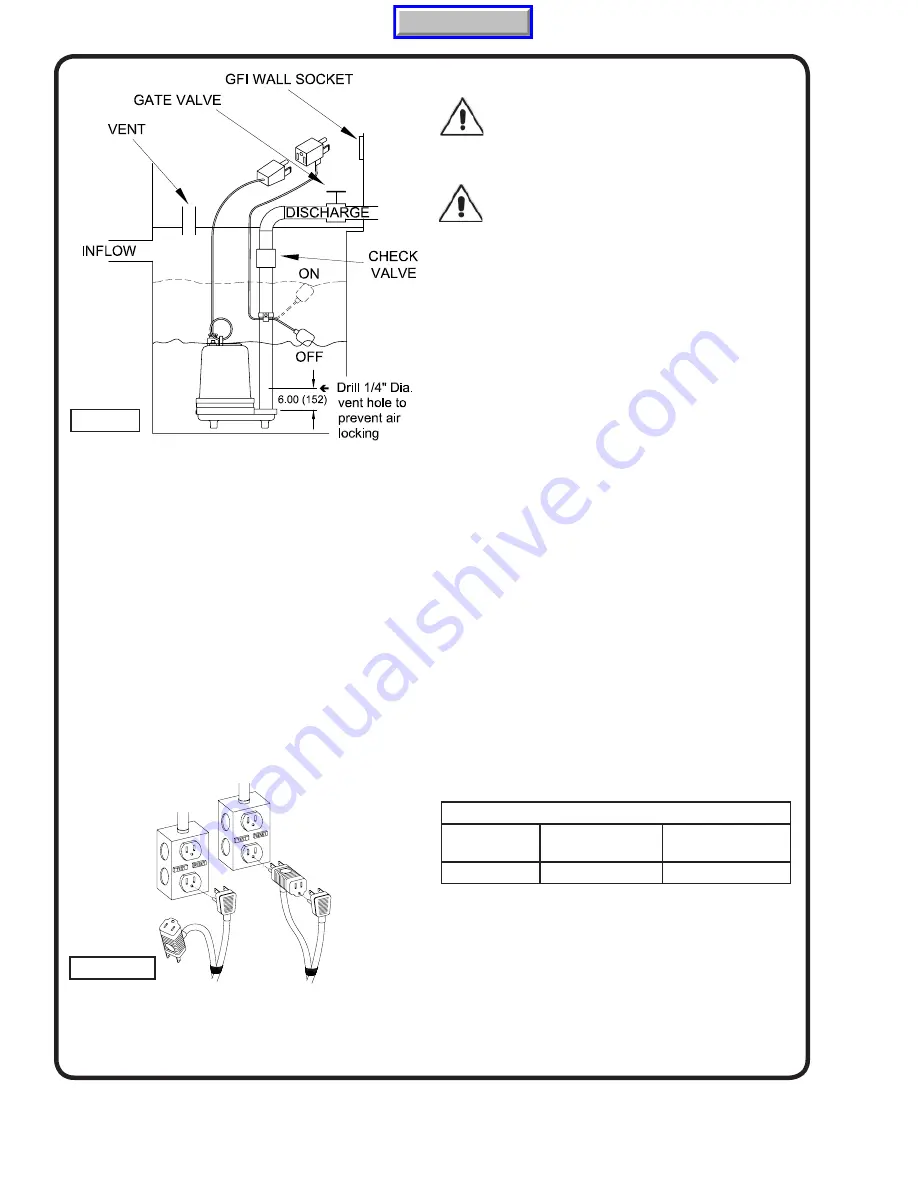
6
3) If a higher pump differential is needed, grip the cord
near the neck of the fl oat, then using the other hand,
exert a steady force on the lower edge of the cable
clamp. The cable clamp should slide up to the new
pivot point. Attach the level control to the discharge
hose in the manner described above.
4) Plug the level control plug into the receptacle, then
plug the pump into the piggyback plug. One cycle of
operation should be observed , so that any potential
problems can be corrected.
5) It is recommended that the fl oat should be set to insure
that the sump well liquid level never drops below the
top of the motor housing or a minimum level of 6
inches above the pump bottom.
6.) Figure 3 shows a typical connection for pumps with the
wide angle fl oat and piggy-back plug, for manual and
automatic
operations.
Automatic-
Plug fl oat cord into outlet, then plug pump
cord into fl oat cord.
Manual-
Plug pump cord directly into outlet.
C-4) Electrical Connections:
WARNING ! - Pump must be used in a circuit
protected by a ground fault interrupter.
WARNING ! - All model pumps and control
panels must be properly grounded per THE
NATIONAL ELECTRIC CODE or CANADIAN
ELECTRIC CODE and STATE, PROVINCE and
LOCAL electric codes. Improper grounding
voids warranty.
C-4.1) Power Cable:
The cord assembly mounted to the pump must not be
modifi ed in any way except for shortening to a specifi c
application. Any splice between the pump and the control
panel must be made in accordance with the electric codes.
It is recommended that a junction box, if used, be mounted
outside the sump or be of at least NEMA 4 (EEMAC-4)
construction if located within the wet well. Do not use the
power cable to lift pump.
NOTE: THE WHITE WIRE IS
NOT A NEUTRAL OR GROUND LEAD, BUT A POWER
CARRYING CONDUCTOR.
C-4.2) Overload Protection:
Single Phase - The type of in-winding overload protector
used is referred to as an inherent overheating protector
and operates on the combined effect of temperature and
current.
This means that the overload protector will trip out and
shut the pump off if the windings become too hot, or the
load current passing through them becomes too high. It
will then automatically reset and start the pump up after
the motor cools to a safe temperature. In the event of an
overload, the source of this condition should be deter-
mined and rectifi ed immediately.
DO NOT LET THE PUMP CYCLE OR RUN IF AN OVER-
LOAD CONDITION OCCURS !
If current through the temperature sensor exceeds the
values listed, an intermediate control circuit relay must
be used to reduce the current or the sensor will not work
properly.
TEMPERATURE SENSOR ELECTRICAL RATINGS
Volts
Continuous
Amperes
Inrush
Amperes
110-120
3.00
30.0
C-4.3) Wire Size:
Consult a qualifi ed electrician for proper wire size. See
table for electrical information.
FIGURE 3
Manual
Automatic
FIGURE 2
Manual Index
Summary of Contents for SE411HT Series
Page 12: ...12 FIGURE 10 Manual Index...
Page 13: ...13 FIGURE 11 Manual Index...