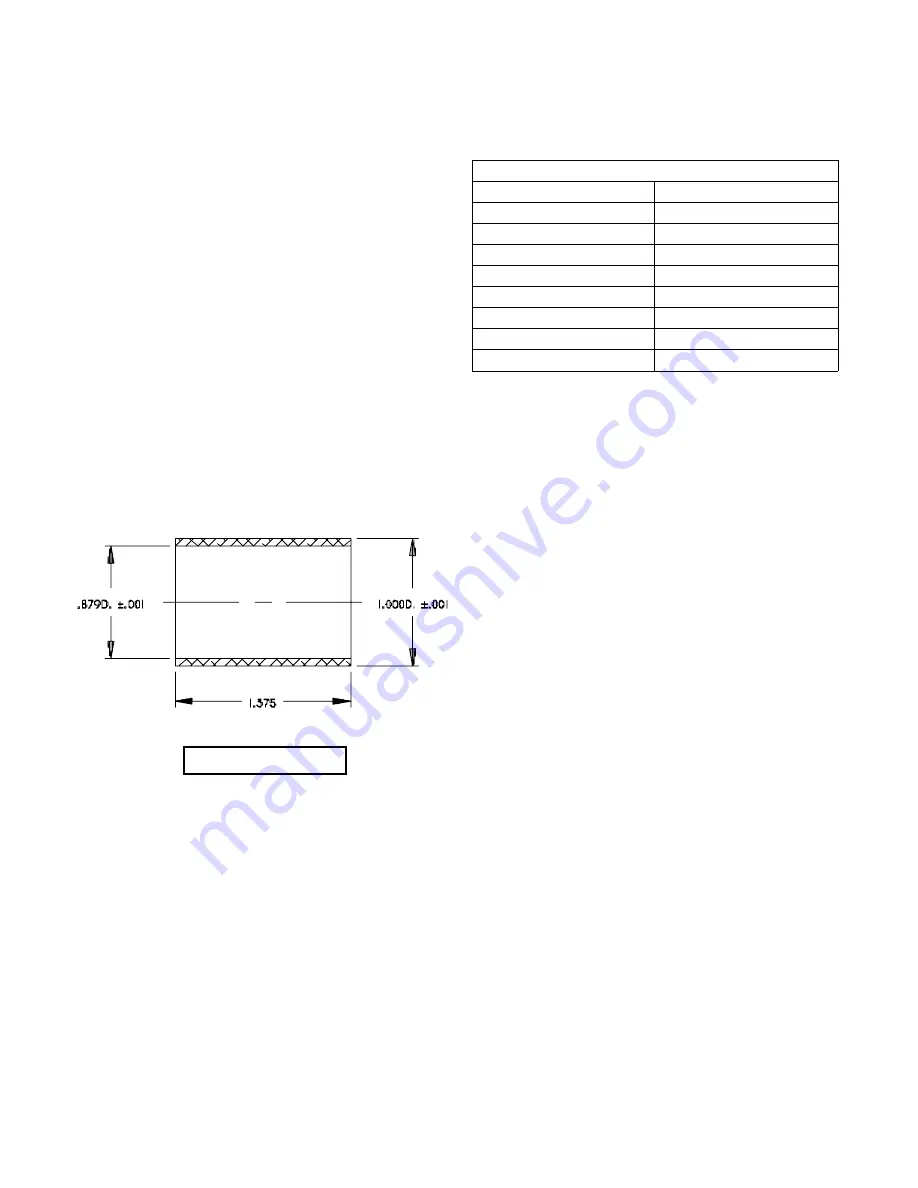
F-3.2) Leak Checking - Double Seal:
When leak checking units, seal retainer (see Figure 3) should
be used in place of impeller and top cover (20) must be
removed. Push motor diaphragm (40) down into cavity. Place
a plug with no burrs or sharp edges (see Figure 4) in recess
formed by diaphragm. Hold diaphragm plug in place with
diaphragm clamp (see Figure 5) fastened to switch end bell.
Install approximately 4Ft. of 1/4" O.D. nylon tubing or
equivalent to inboard seal housing with a male connector
assembly.
(NOTE: Run tubing thru drive end bell)
. Install
another compression fitting on opposite end of tubing so it can
be adapted to air line fittings. Install pipe plug (11) in either
switch end bell (42) or drive end bell (46). Apply 4 to 5 PSI air
pressure to nylon tubing attached to seal housing, submerge
motor, any bubbling indicates outboard seal leakage.
(NOTE: DO NOT APPLY HIGHER AIR PRESSURE TO
MOTOR OR SEAL HOUSING DUE TO THE POSSIBILITY OF
BLOWING SEAL SEATS OUT OF POSITION)
. Take motor
out of water and remove one pipe plug (11) from either end bell
(42 or 46) and apply 4 to 5 PSI air pressure. Hold tubing
attached to seal housing out of water and submerge motor.
Any bubbling indicates inbord seal leakage. In any case where
leakage occurs, changes must be made to correct the situation.
After removing motor from water, drain and dry all water from
top section of switch end bell.
F-3.3) Leak Checking - Leak Sensor:
Seal off hole for vent in bottom cover using a gasketed plate
bolted in place with 1/4-20 bolts and nuts. Remove vent plug
(82) and apply 4 to 5 PSI air pressure. Submerge unit in clear
water and check for air leakage. Release air pressure and
reinstall vent plug securely. Now, remove pipe plug (81) from
top cover (89) and apply 4 to 5 PSI air pressure. Submerge unit
and check for air leakage, correct any situation where leakage
occurs. See Section F-8 for assembly and disassembly.
F-4.1) Oil Filling - Pump:
(See Figures 4, 5, & 6).
All factory units are vacuum filled with dielectric oil (see Table
1). When vacuum filling these motors, use same diaphragm
retainer (see Figure 4) and clamp
(see Figure 5) as used when
leak checking.
This plug will allow the diaphragm to partially raise up in cavity
when unit is being filled. This allows room for contraction of the
diaphragm when unit is operated in cooler temperatures.
COOLING OIL - Dielectric - TABLE 1
SUPPLIER
GRADE
BP
Enerpar SE100
CONOCO
Pale Paraffin 22
MOBIL
D.T.E. Oil Light
G & G OIL
Circulating 22
Imperial Oil
Voltesso-35
Shell Canada
Transformer-10
Texaco
Diala-Oil-AX
Woco
Premium 100
A 1/8" pipe nipple is attached to pipe plug opening in switch
end bell (42). A 1/2" or larger valve is attached to 1/8" nipple
with bushings. The unit is now turned upside down with shaft
up. A line (plastic tubing or pipe) is run from the valve into a
container of dielectric oil. A 1/8" pipe nipple is threaded into
pipe opening in drive end bell (46).
A 3/8" nipple is attached to 1/8" nipple with bushings. A clear
plastic hose is connected to the 3/8" nipple. The hose is run up
vertically at least 3 ft. Now connect hose to vacuum source.
With the valve closed on the bottom side of motor,
25" to 29"
of vacuum is pulled on the motor. The valve under motor is now
slightly opened. Allow motor to fill with oil and oil level to rise
approximately 2" in plastic hose. Now close bottom valve. As
the air is pulled out of the unit, the oil level in the plastic hose
will drop. The valve to the oil must then be reopened to bring
the oil level up again. This may have to be repeated 2 or 3
times. After 10 to 15 minutes, the oil level in the plastic hose
should remain constant and no air bubbles should be flowing
up through the oil. Shaking the unit slightly will allow trapped
air to rise through the oil. If there are no air bubbles flowing up
through the oil, the unit is full.
NOTE:
If a steady stream of air
bubbles persists, there is a leak in the unit. Check all joints,
gaskets and seal.
Remove upper hose and fittings, insert pipe plug and secure.
Turn the unit right side up and fill the pipe that was connected
to the oil source with oil. Open the valve, then remove the pipe
and valve, insert pipe plug and secure.
NOTE:
Be sure motor
is completely filled. Reassemble per section F-7.
F-4.2) Oil Filling - Leak Sensor:
When leak testing is finished, make sure pipe and vent plugs
(81) and (82) are tight. (
NOTE:
Vent plug must be in the closed
position). Now lay leak sensor on its side with hole in bottom
cover facing up, pour three (3) fluid ounces of cooling oil (see
Table 1) through hole in bottom cover.
DO NOT OVERFILL
.
Leave leak sensor in a horizontal position until it is
reassembled to pump. Put O-ring (94) over tubing coming out
of pump. Hold finger over hole in leak sensor until it is aligned
with tubing. Bolt unit into place.
Fig. 3 - Double Seal
10