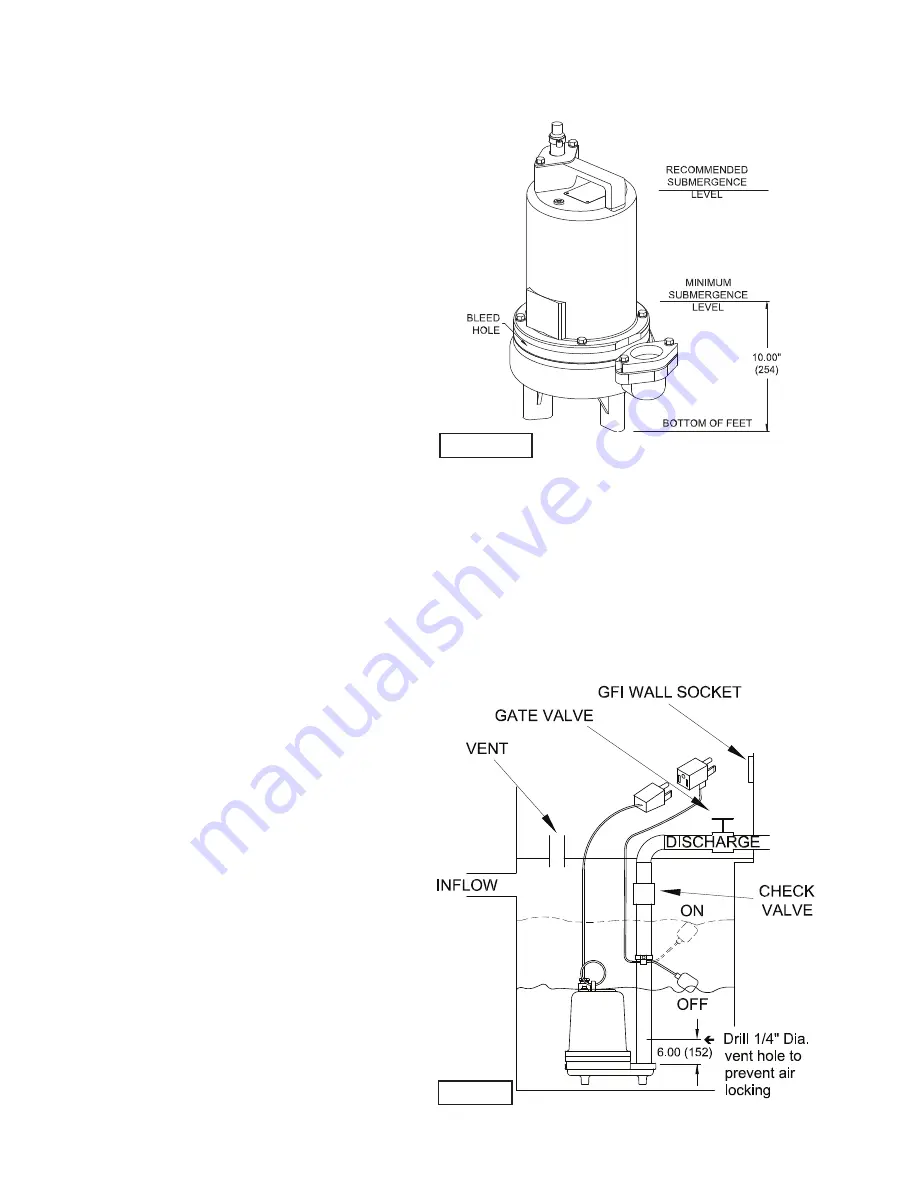
6
SECTION B: GENERAL INFORMATION
B-1) To the Purchaser:
Congratulations! You are the owner of one of the
fi
nest pumps
on the market today. CP&S pumps are products engineered
and manufactured of high quality components. Over one
hundred years of pump building experience along with a
continuing quality assurance program combine to produce a
pump which will stand up to the toughest applications. This
manual will provide helpful information concerning installation,
maintenance, and proper service guidelines.
B-2) Receiving:
Upon receiving the pump, it should be inspected for damage
or shortages. If damage has occurred,
fi
le a claim immediately
with the company that delivered the pump. If the manual
is removed from the packaging, do not lose or misplace.
B-3) Storage:
Short Term-
CP&S Pumps are manufactured for ef
fi
cient
performance following short inoperative periods in storage.
For best results, pumps can be retained in storage, as factory
assembled, in a dry atmosphere with constant temperatures
for up to six (6) months. Long Term- Any length of time
exceeding six (6) months, but not more than twenty-four (24)
months. The unit should be stored in a temperature controlled
area, a roofed over walled enclosure that provides protection
from the elements (rain, snow, wind-blown dust, etc.), and
whose temperature can be maintained b40 deg. F
and +120 deg. F. (4.4 - 49°C). Pump should be stored in its
original shipping container. On initial start up, rotate impeller
by hand to assure seal and impeller rotate freely. If it is
required that the pump be installed and tested before the long
term storage begins, such installation will be allowed provided:
1.) The pump is not installed under water for more than
one (1) month.
2.) Immediately upon satisfactory completion of the test,
the pump is removed, thoroughly dried, repacked in the
original shipping container, and placed in a temperature
controlled storage area.
B-4) Service Centers:
For the location of the nearest Barnes Service Center, check
your Barnes representative or Crane Pumps & Systems, Inc.,
Service Department in Piqua, Ohio, telephone (937) 778-8947
or Crane Pumps & Systems Canada, in Brampton, Ontario,
(905) 457-6223.
SECTION C: INSTALLATION
C-1) Location:
These pumping units are self-contained and are recommended
for use in a sump, lift station or basin. The sump, lift station or
basin shall be vented in accordance with local plumbing codes.
This pump is designed to pump sewage, ef
fl
uent, or other
nonexplosive or noncorrosive wastewater. and shall
NOT
be
installed in locations classi
fi
ed as hazardous in accordance
with the National Electrical Code (NEC), ANSI/NFPA 70 or the
Canadian Electrical Code (CEC). Never install the pump in a
trench, ditch or hole with a dirt bottom; the legs will sink into the
dirt and the suction will become plugged.
C-1.1) Submergence:
It is recommended that the pump be operated in the submerged
condition and the sump liquid level should never be less than
10 inches above the pump bottom (see Fig. 1).
C-2) Discharge:
Discharge piping should be as short as possible. Both a check
valve and a shut-off valve are recommended for each pump
being used. The check valve is used to prevent back
fl
ow
into the sump. Excessive back
fl
ow can cause
fl
ooding
and/or damage to the pump. The shut-off valve is used to
stop system
fl
ow during pump or check valve servicing.
C-3) Liquid Level Controls:
Figure 2 shows a typical installation for any submersible pump
using a level control mounted to the discharge piping with a
piggy-back plug.
FIGURE 1
FIGURE 2