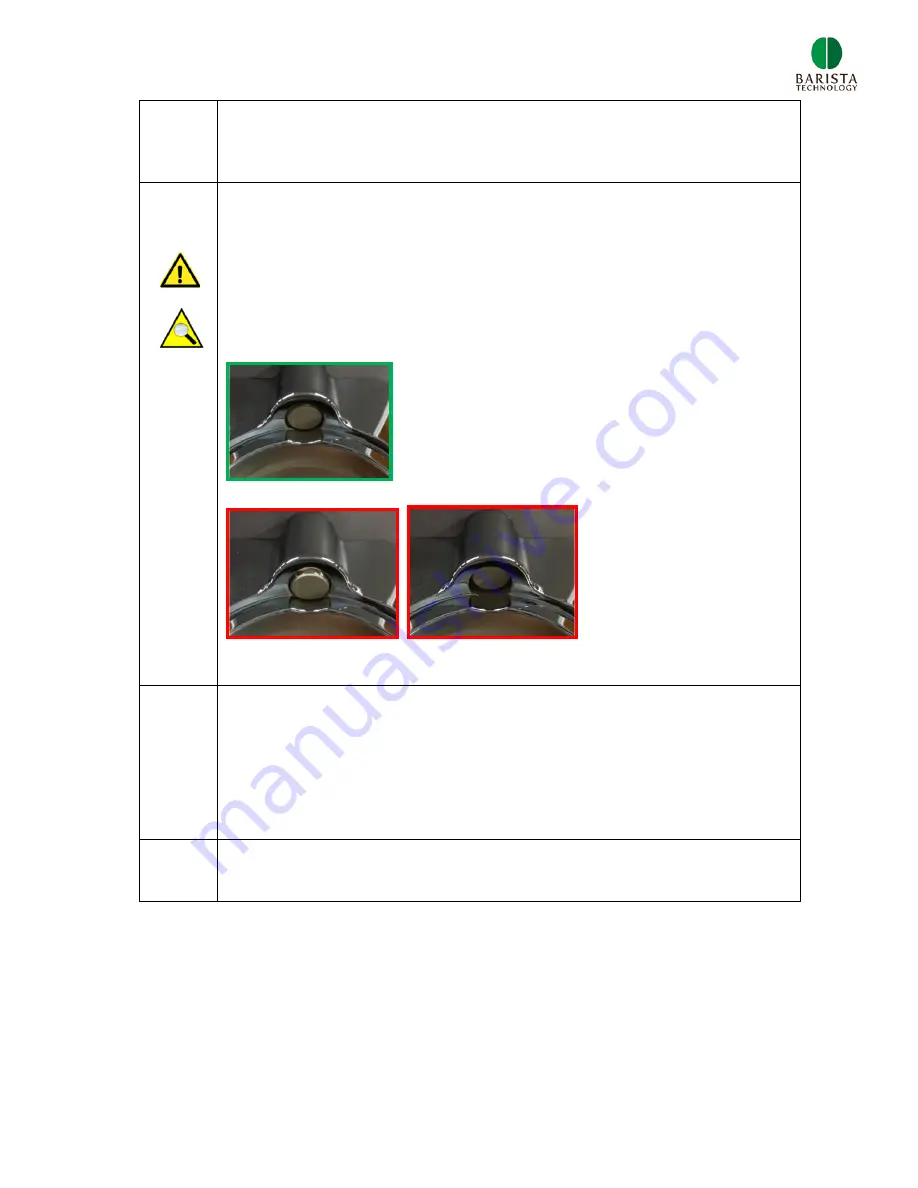
11
7
Insert a new induction sensor and connect the sensor to the motor
controller PCB, see step 6.
8
Fasten the set screw M5, see step 5.
Critical: The sensor does not function when too much torque
is applied
.
Check the position of the sensor after assembly
Correct
NOT correct NOT correct
9
Mount the main housing – back cover, see step 3
Mount the main housing – middle cover, see step 2.
Mount the main housing – top cover, step 1.
10
Check functioning of the new induction sensor.