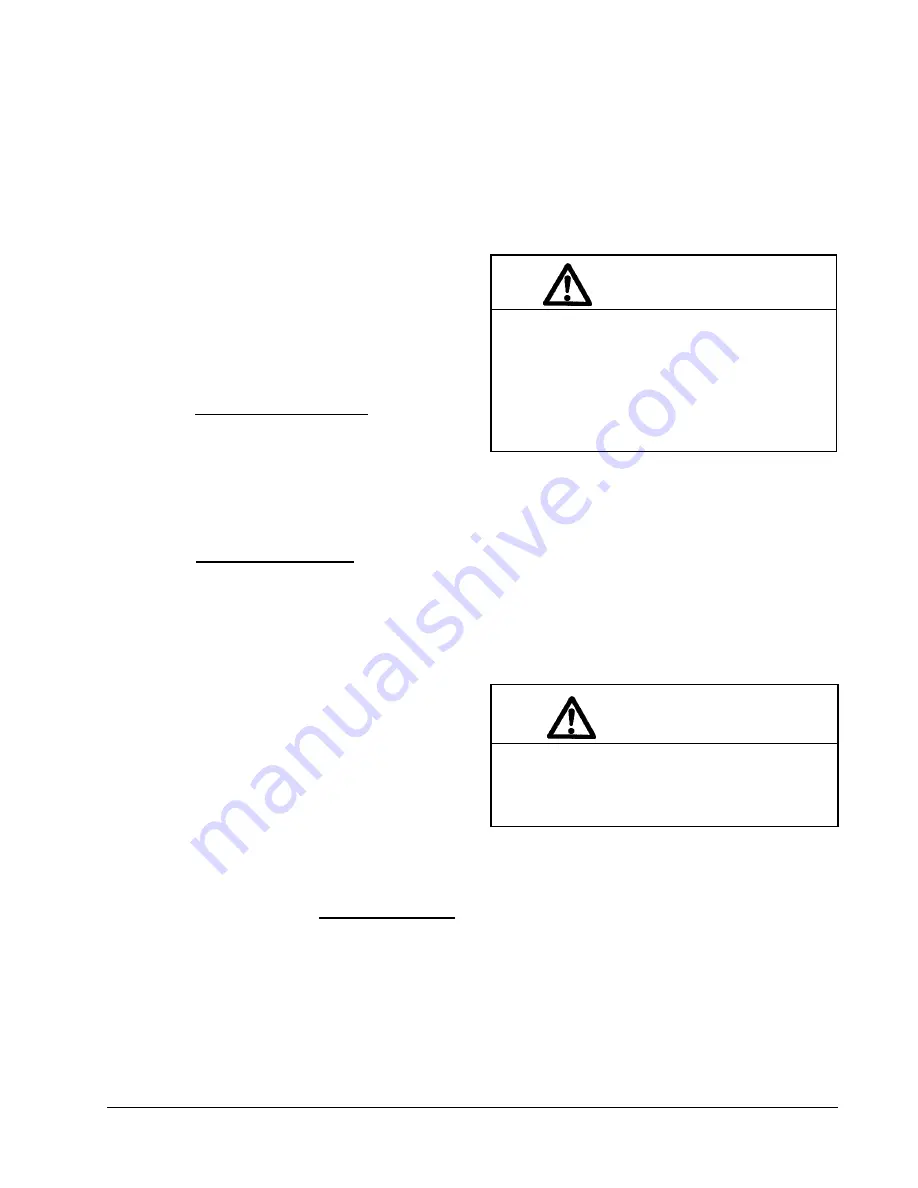
Manual 2100-365
Page 21
1. Make sure you have proper main burner orifices.
2. Gas supply pressure must be between 11 and 13
inches W.C. for propane (LP) gas.
3. Start furnace following "Operating Instructions" on
front door.
4. Let furnace warm up for 6 minutes.
5. Adjust manifold pressure to 10.0 W.C. ± 0.3
inches W.C. See Section 19, "Manifold Pressure
Adjustment".
PROPANE (LP) GAS INPUT RATE
8. Calculate gas input using this formula:
Gas Heating Value (BTU/cu. ft.)
x 3,600 sec/hr
Gas input =
= BTU/hour
Time (Seconds for one
cubic foot of gas)
Example:
Assume it took 29 seconds for one cubic foot of
gas to flow and heating value of 1,000 BTU/cu. ft.
1,000 x 3,600
Gas input =
=
124,138
BTU
29
If you left no other pilots on, this is the furnace gas
input.
9. If you left water heater, dryer or range pilots on,
allow for them in calculating correct furnace gas
input. A quick way is to allow 1,000 BTU per
hour for a water heater, 500 BTU per hour for
dryer and 500 BTU per hour for each range burner
pilot.
Example:
If you left gas water heater, dryer, two range
burner pilots and one oven pilot on, allow:
Water heater pilot
1,000 BTU per hour
Dryer pilot
500 BTU per hour
2 range burner pilots
1,000 BTU per hour
1 range oven pilot
500 BTU per hour
3,000 BTU per hour
Subtracting 3,000 BTU per hour from 124,138
BTU per hour measured above equals 121,138
BTU per hour. This would be the correct furnace
gas input after allowing for pilots left on.
6. With stopwatch, measure time it takes to consume
two cubic feet of gas.
•
If dial is one-half cubic foot per revolution,
measure time for four revolutions.
•
If dial is one cubic foot per revolution, measure
time for two revolutions.
•
If dial is two cubic feet per revolution, measure
time for one revolution.
7. Divide this time by two. This gives average time
for one cubic foot of gas to flow through meter.
Example: If it took 58 seconds for two cubic feet
to flow, it would take 29 seconds for one cubic foot
to flow.
21. STANDARD ORIFICE SIZING AND
HIGH ALTITUDE DERATE
This furnace is shipped with fixed gas orifices for use
with Natural Gas and sized for 1000 BTU/cubic foot
gas. Make sure actual gas input does not exceed
rating plate input. You may need to change orifices
to get correct gas input. Whether you do or not
depends on input, and your gas heat value at standard
conditions and elevation. Consult your local gas
supplier for gas heat value and any special derating
requirements. See Section 19 for more information.
10. Manifold pressure may be adjusted within the
range of 3.2 inches W.C. to 3.8 inches W.C. to get
rated input ± 2 percent. See Section 17, "Manifold
Pressure Adjustment". If you cannot get rated
input with manifold pressure within the allowable
range, you must change orifices.
WARNING
Propane (LP) gas installations do not have gas
meters to double check input rate. Measure
manifold pressure adjustment with an accurate
manometer. Failure to accurately adjust
pressure could cause heat exchanger failure,
asphyxiation, fire or explosion, resulting in
damage, injury or death.
WARNING
Do not set Propane (LP) manifold pressure at
11.0 inches W.C. It could cause heat
exchanger failure.
Summary of Contents for WG421
Page 8: ...Manual 2100 365 Page 5 MIS 1352 FIGURE 1 UNIT DIMENSIONS...
Page 12: ...Manual 2100 365 Page 9 FIGURE 4 MOUNTING INSTRUCTIONS MIS 1472...
Page 15: ...Manual 2100 365 Page 12 FIGURE 8 COMMON WALL MOUNTING INSTALLATIONS MIS 1474...
Page 20: ...Manual 2100 365 Page 17 FIGURE 11 LOW VOLTAGE WIRING MIS 1162...
Page 21: ...Manual 2100 365 Page 18 FIGURE 12 GAS PIPE CONNECTION MIS 1478...
Page 29: ...Manual 2100 365 Page 26 26 LIGHTING AND SHUTDOWN INSTRUCTIONS FIGURE 14 INSTRUCTION LABEL...
Page 34: ...Manual 2100 365 Page 31 FIGURE 18 460 VOLT BLOWER MOTOR WIRING OPTIONS MIS 1487 A B C...
Page 41: ...Manual 2100 365 Page 38...
Page 42: ...Manual 2100 365 Page 39...
Page 43: ...Manual 2100 365 Page 40...
Page 44: ...Manual 2100 365 Page 41...
Page 45: ...Manual 2100 365 Page 42...
Page 46: ...Manual 2100 365 Page 43...
Page 47: ...Manual 2100 365 Page 44...
Page 48: ...Manual 2100 365 Page 45...
Page 49: ...Manual 2100 365 Page 46...
Page 50: ...Manual 2100 365 Page 47...
Page 51: ...Manual 2100 365 Page 48...
Page 52: ...Manual 2100 365 Page 49...