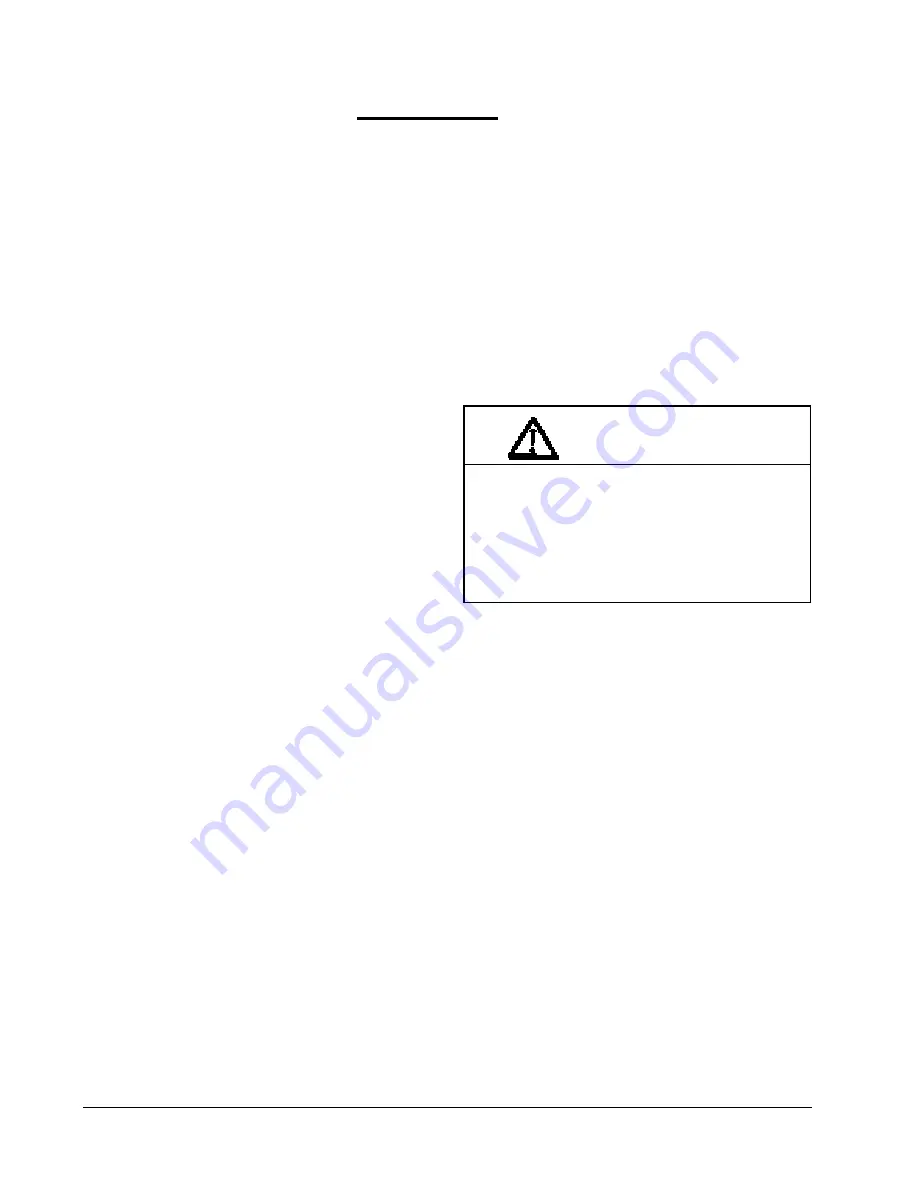
Manual 2100-385B
Page
20
NOTICE
The refrigeration system in this unit is charged
with refrigerant R-407C
SERVICE PROCEDURE AND
CONSIDERATIONS
Refrigerant R-407C is a blend of three refrigerants,
HFC-32 / HFC-125 / HFC134A. Unlike pure fluids and
azeotropes, blends boil and condense at varying
temperatures for a given pressure. The range over
which the temperature varies is referred to as
temperature glide. R-407C has moderately high
temperature glide between about 9° F and 13° F (5 to
7.2 Celsius) depending upon pressure.
When dealing with blends, pressure temperature tables
are presented in an unconventional manner. Two
temperatures are listed for the same pressure – the liquid
temperature and the vapor temperature.
When a pressure reading is taken from the suction line
or discharge line it is converted to temperature from the
“Vapor Temperature” column on the pressure
temperature chart.
When a pressure reading is taken at the liquid line it is
converted to temperature from the “Liquid
Temperature” column on the pressure temperature chart.
All Bard “WE” models have a pressure tap in the
suction line and the liquid line.
See Pressure Temperature Table 12 on page 21.
CHARGING
When charging a system with R-407C, only the
liquid phase is to be used to ensure proper
refrigerant composition and system performance.
When charging the system into the suction side, care
must be exercised to avoid damage to the compressor.
Because the refrigerant leaving the refrigerant cylinder
must be in liquid phase, it is suggested that a sight glass
be connected between the charging hose and the suction
service port. This will permit you to adjust the cylinder
hand valve so that liquid can leave the cylinder while
allowing vapor to enter the compressor.
The proper refrigerant amount is shown on the unit
rating plate.
LEAKS
If a significant leak develops in the system and a
noticeable change in the system performance occurs,
remove the remaining refrigerant with proper refrigerant
recovery methods, repair the leak with proper industry
practice and methods, and then, after evacuation,
recharge the system with new refrigerant. Again, charge
only with liquid refrigerant to ensure that the proper
composition is in the system.
CAUTION
Leak checking should never be done with a
mixture of R-407C and air. Leak checking
can be performed safely with a mixture of
R-407C and nitrogen. Make sure the leak
detector is capable of detecting R-407C
before using.
Notice:
When opening a system, care must be taken to
minimize the system exposure to atmosphere.
Exposure for more than five minutes could
shorten the life of the system. The compressor in
this system contains Polyol Ester (POE) oil.
POE's are very hygroscopic. They absorb
moisture from the atmosphere at a much faster
rate than mineral oils used in R-22 systems.
This system has a factory-installed filter drier in the
liquid line. It is highly recommended that the filter drier
be replaced when the system has been open. Make sure
the replacement filter drier is suitable and approved for
use with R-407C.
Before recharging the system, a vacuum of 250 microns
or less must be achieved.