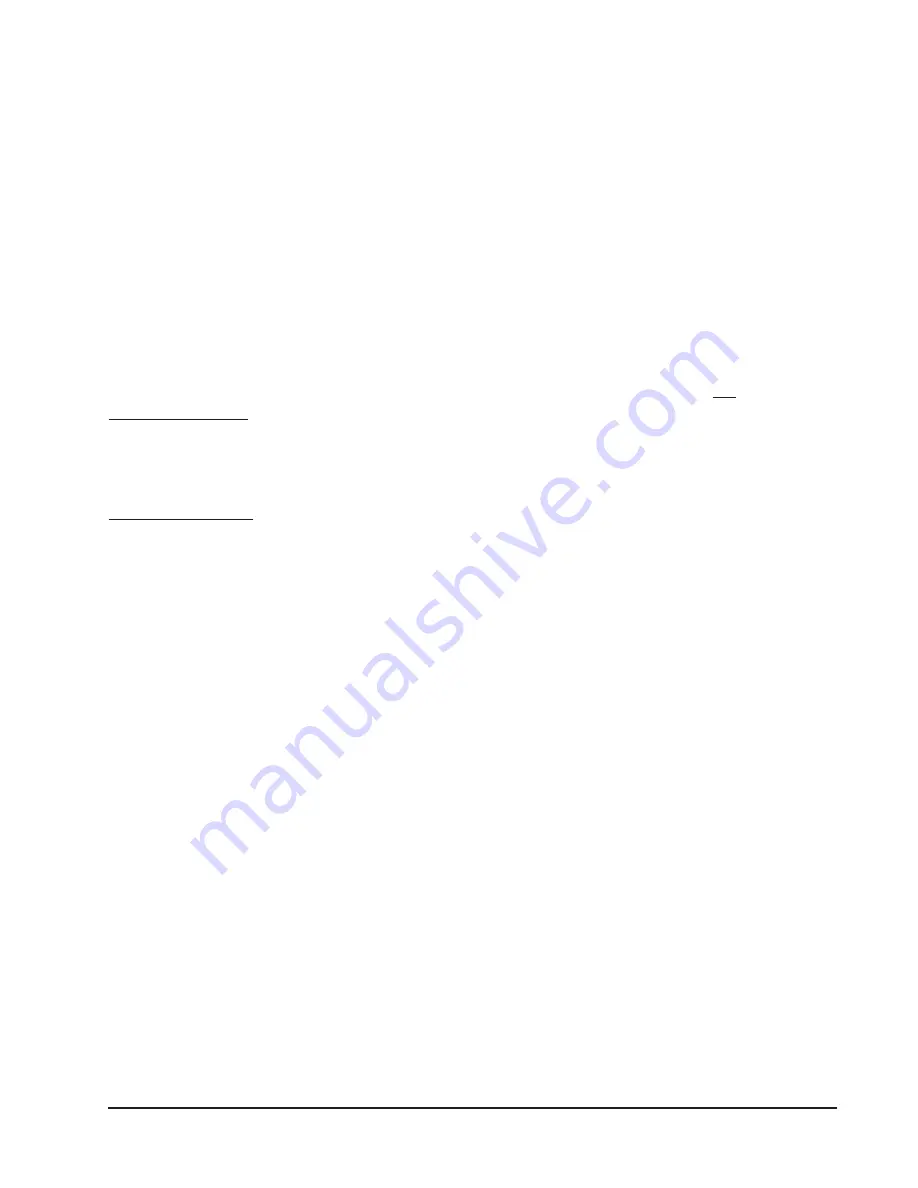
Manual
2100-526E
Page
15 of 24
SERVICE HINTS
1. Maintain clean air filters at all times. Also, do not close
off or block supply and return air registers. This reduces
air flow through the system, which shortens equipment
service life as well as increasing operating costs.
2. Check all power fuses or circuit breakers to be sure they
are the correct rating.
3. Periodic cleaning of the outdoor coil to permit full and
unrestricted airflow circulation is essential.
Frequency of coil cleaning will depend on duty cycle of
equipment, type of use and installation site variables.
Telecommunication type installations in high traffic
areas or in areas none too frequent to airborne debris,
will require more frequent coil maintenance than those
in areas not subject to those conditions.
SEQUENCE OF OPERATION
NON-ECONOMIZER
Stage 1 (Y1) cooling call activates Step 1 (partial
capacity, 66%) of compressor capacity.
Stage 2 (Y2) cooling call activates Step 2 (full capacity,
100%) of compressor capacity.
WITH ECONOMIZER
Stage 1 (Y1) cooling call goes to economizer controls for
decision:
- If Enthalpy Control decides outdoor conditions are
suitable for free cooling, the economizer will operate.
• If Stage 2 cooling call is issued during
economizer operation, the economizer will
close and the compressor will go straight to
Step 2 full capacity operation.
- If Enthalpy Control decides outdoor conditions
are not suitable for free cooling, the economizer
will not operate (or close) and Step 1 of the
compressor will operate.
• If Stage 2 cooling call is issued, the
compressor will shift to Step 2 full cooling
capacity operation.
COMPRESSOR CONTROL MODULE
The compressor control module is standard on the models
covered by this manual. The compressor control is an
anti-short cycle/lockout timer with high and low pressure
switch monitoring and alarm relay output.
Adjustable Delay On Make And Break Timer
On initial power up or anytime power is interrupted to the
unit, the
delay on make
period begins, which will be 2
minutes plus 10% of the
delay on break
setting. When
the delay on make is complete and the high pressure and
low pressure switches are closed, the compressor
contactor is energized. Upon shutdown the delay or
break timer starts and prevents restart until the delay on
break and delay on make periods have expired.
During routine operation of the unit with no power
interruptions, the compressor will operate on demand
with no delay.
High Pressure Switch and Lockout Sequence
If the high pressure switch opens, the compressor
contactor will de-energize immediately. The lockout
timer will go into a
soft lockout
and stay in soft lockout
until the high pressure switch closes and the delay on
break time has expired. If the high pressure switch
opens again in this same operating cycle, the unit will go
into
manual lockout
condition and the alarm relay circuit
will energize. Recycling the wall thermostat resets the
manual lockout.
Low Pressure Switch, Bypass and Lockout Sequence
If the low pressure switch opens for more than 120
seconds, the compressor contactor will de-energize and
go into a soft lockout. Regardless the state of the low
pressure switch, the contactor will reenergize after the
delay on make time delay has expired. If the low
pressure switch remains open, or opens again for longer
than 120 seconds the unit will go into manual lockout
condition and the alarm relay circuit will energize.
Recycling the wall thermostat resets the manual lockout.
Optional Low Ambient Control
An optional low ambient control is available for both
factory and field installed options. The low ambient
control is to be applied to the WA3S/WA4S/WA5S
models when operation below 50°outdoor conditions are
anticipated. Without this device, the evaporating pressure
would fall off, and the indoor coil would ice over.
The fan cycling control cycles the fan motor on, once the
liquid refrigerant pressure reaches 350 psig, and off, once
it has dropped to 225 psig. It will continue to cycle
between these parameters depending on outdoor
temperatures and the load/stage of the system.
This cycling maintains a minimum liquid pressure
affecting the minimum suction pressure. This effect
insures an evaporating temperature that is slightly above
the point of ice formation on the evaporator.