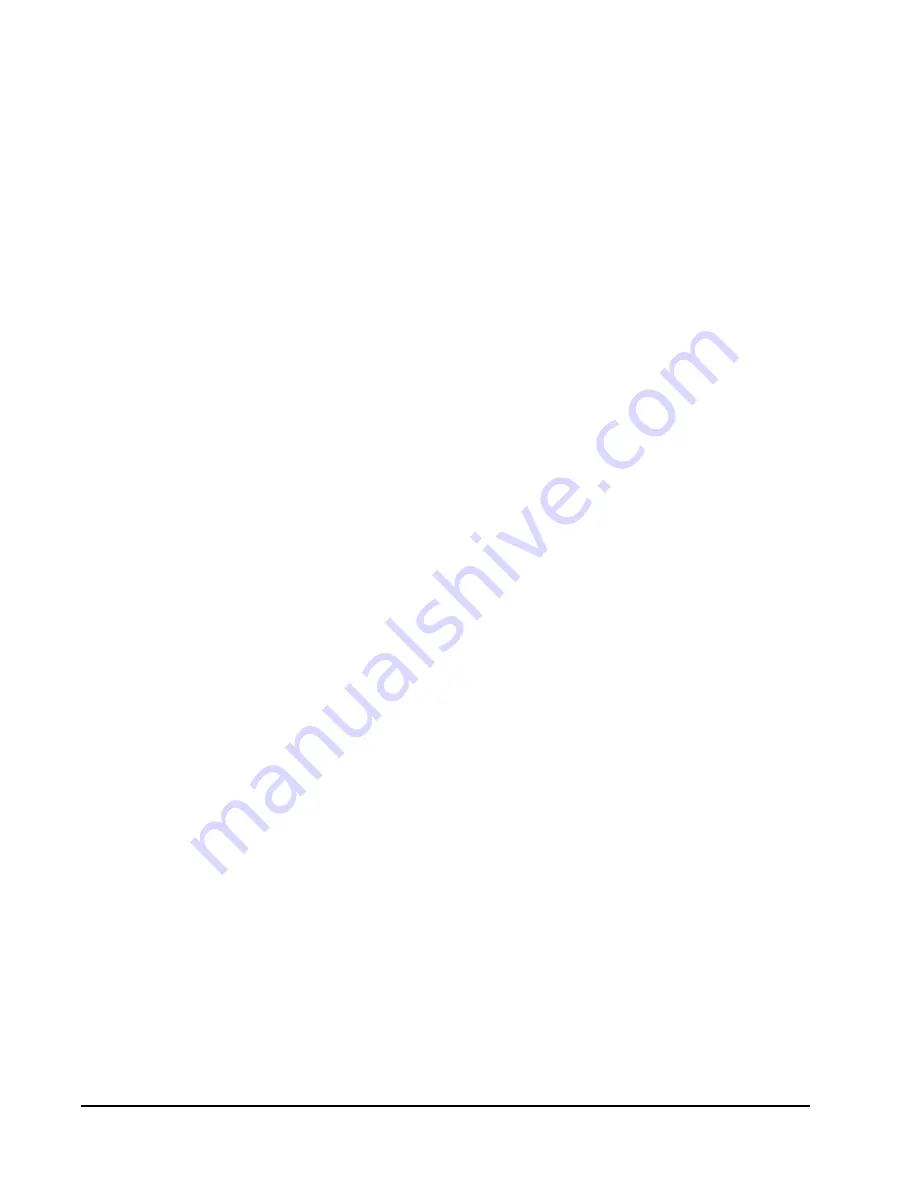
Manual 2100-720C
Page
24 of 42
High pressure switch settings: Opens 650 +/– 15 PSI,
Closes 520 +/– 15 PSI.
Three Phase Scroll Compressor Start
Up Information
Scroll compressors, like several other types of
compressors, will only compress in one rotational
direction. Direction of rotation is not an issue with
single phase compressors since they will always start
and run in the proper direction.
However, three phase compressors will rotate in either
direction depending upon phasing of the power.
Since there is a 50-50 chance of connecting power
in such a way as to cause rotation in the reverse
direction, verification of proper rotation must be made.
Verification of proper rotation direction is made by
observing that suction pressure drops and discharge
pressure rises when the compressor is energized.
Reverse rotation also results in an elevated sound level
over that with correct rotation, as well as substantially
reduced current draw compared to tabulated values.
Verification of
proper rotation
must be made at the time
the equipment is put into service. If improper rotation
is corrected at this time, there will be no negative
impact on the durability of the compressor. However,
reverse operation for over 1 hour may have a negative
impact on the bearing due to oil pump out.
NOTE:
If compressor is allowed to run in reverse
rotation for an extended period of time, the
compressor’s internal protector will trip.
All three phase compressors are wired identically
internally. As a result, once the correct phasing is
determined for a specific system or installation,
connecting properly phased power leads to the same
Fusite terminal should maintain proper rotation
direction.
The direction of rotation of the compressor may be
changed by reversing any two line connections to the
unit.
Phase Monitor
All units with three phase scroll compressors are
equipped with a three phase line monitor to prevent
compressor damage due to phase reversal.
The phase monitor in this unit is equipped with two
LEDs. If the Y signal (call for cooling) is present at the
phase monitor and phases are correct, the green LED
will light.
If phases are reversed, the red fault LED will be lit and
compressor operation is inhibited.
If a fault condition occurs, reverse two of the supply
leads to the unit.
Do not reverse any of the unit factory
wires as damage may occur.
Condenser Fan Operation
NOTE:
Certain models may be equipped with a low
ambient control (LAC), and if so, the condenser fan
motor will have a delayed start until system refrigerant
operating pressure builds up. After starting, the fan
motor may or may not cycle depending upon ambient
conditions. This is normal operation.
Vent Connection Plug
All units are equipped with a vent connection plug in
the side of the control panel for the different ventilation
packages to plug in to. If the compressor will not start
and there is no "Y1" at the compressor control module,
first check to make sure that either the optional vent is
plugged into the vent connection plug or the supplied
jumper plug is in place.
The unit will not operate
without anything plugged in.
This plug is located on
the side of the control panel behind the front vent door
(behind the filter access door). If the unit is supplied
with a factory-installed vent package, it will be plugged
in but the jumper plug will also be tethered next to the
connection for troubleshooting purposes, if necessary.
NOTE:
Economizer will disable Balanced Climate
operation.
Compressor Control Module
The compressor control module (CCM) is standard on
all models covered by this manual.
Features
Delay-on-Make Timer
Short Cycle Protection/Delay-on-Break
Low Pressure Detection
High Pressure Detection
LPC and HPC Status LEDs
Test Mode
Brownout Protection with Adjustment
Delay-on-Make Timer
A delay-on-make timer is included to be able to delay
startup of the compressor. This is desired when more
than one unit is on a structure so that all of the units
do not start at the same time which could happen
after a power loss or building shutdown. The delay-
on-make time period is 2 minutes plus 10% of the
delay-on-break time period. To ensure that all of the
units do not start at the same time, adjust the delay-
on-break timer on each unit to a slightly different
delay time.
Short Cycle Protection/Delay-on-Break
An anti-short cycle timer is included to prevent short
cycling the compressor. This is adjustable from 30
seconds to 5 minutes via the adjustment knob (see
Figure 22). Once a compressor call is lost, the time
period must expire before a new call will be initiated.
Summary of Contents for WA Series
Page 2: ......
Page 12: ......
Page 18: ...Manual 2100 479 Page 6 of 11 FIGURE 1 TYPICAL AIR CONDITIONING SYSTEM COOLING CYCLE MIS 369...
Page 19: ...Manual 2100 479 Page 7 of 11 FIGURE 2 TYPICAL HEAT PUMP SYSTEM COOLING CYCLE MIS 368...
Page 24: ......
Page 66: ...Manual 2100 720C Page 42 of 42 GRAPH 3 W5SAC FAD NE5 W O Exhaust Ventilation Delivery...
Page 67: ......
Page 72: ...Manual 2110 1461B Page 5 of 17 This page intentionally left blank...
Page 76: ...Manual 2110 1461B Page 9 of 17 This page intentionally left blank...
Page 85: ......