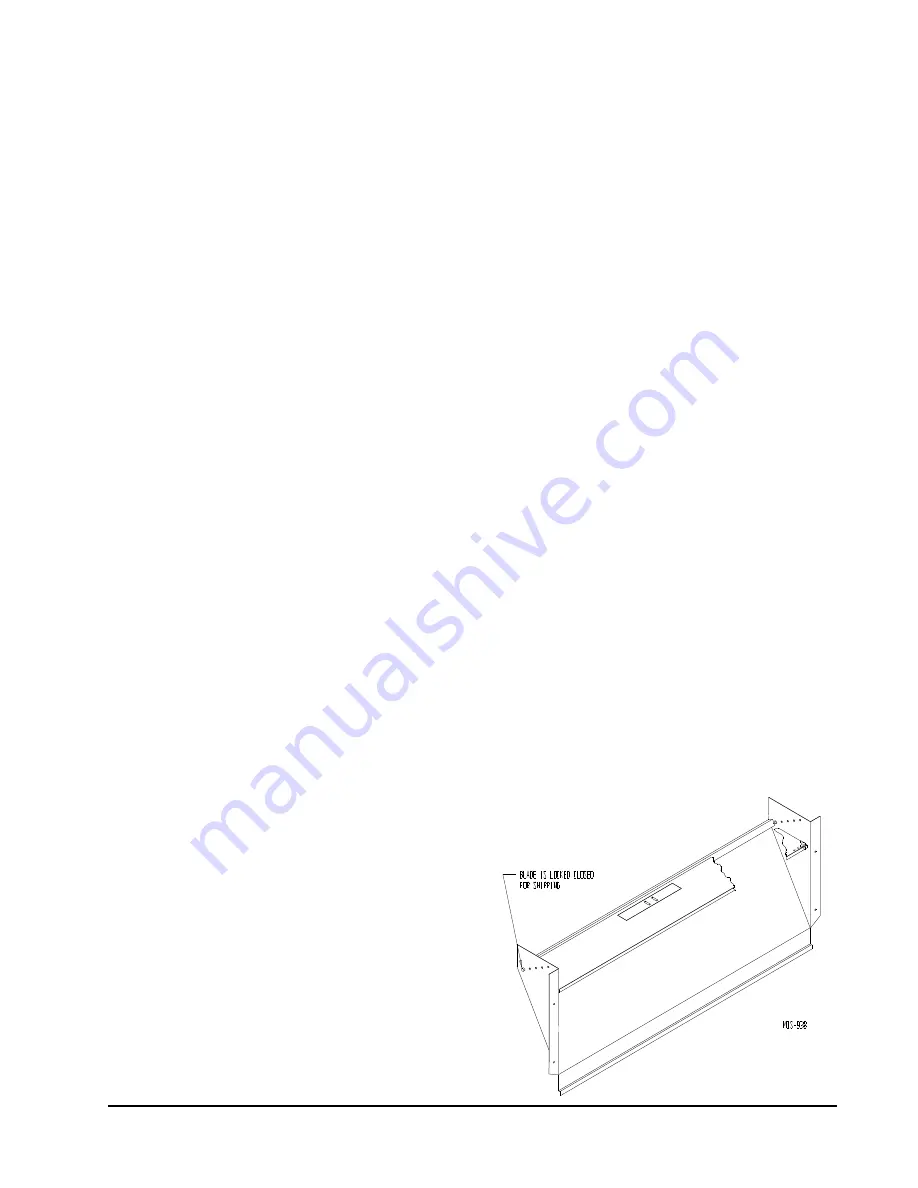
Manual 2100-615A
Page
5 of 24
FILTERS
A 1-inch throwaway filter is standard with each unit.
The filter slides into position making it easy to service.
This filter can be serviced from the outside by removing
the filter access panel. A 1-inch washable filter and
2-inch pleated filter are also available as optional
accessories. The internal filter brackets are adjustable
to accommodate the 2-inch filter by bending two (2)
tabs down on each side of the filter support bracket.
FRESH AIR INTAKE
All units are built with fresh air inlet slots punched in
the service door.
If the unit is equipped with a fresh air damper
assembly, the assembly is shipped already attached
to the unit. The damper blade is locked in the
closed position. To allow the damper to operate, the
maximum and minimum blade position stops must be
installed. See Figure 1.
All capacity, efficiency and cost of operation
information is based upon the fresh air blank-off plate
in place and is recommended for maximum energy
efficiency.
The blank-off plate is available upon request from the
factory and is installed in place of the fresh air damper
shipped with each unit.
CONDENSATE DRAIN
A plastic drain hose extends from the drain pan at
the top of the unit down to the unit base. There are
openings in the unit base for the drain hose to pass
through. In the event the drain hose is connected to
a drain system of some type, it must be an open or
vented type system to assure proper drainage.
Size of unit for a proposed installation should be based
on heat loss calculation made according to methods of
Air Conditioning Contractors of America (ACCA). The
air duct should be installed in accordance with the
Standards of the National Fire Protection Association
for the Installation of Air Conditioning and Ventilating
Systems of Other Than Residence Type, NFPA No.
90A, and Residence Type Warm Air Heating and Air
Conditioning Systems, NFPA No. 90B. Where local
regulations are at a variance with instructions, installer
should adhere to local codes.
DUCT WORK
All duct work, supply and return, must be properly
sized for the design airflow requirement of the
equipment. Air Conditioning Contractors of America
(ACCA) is an excellent guide to proper sizing. All duct
work or portions thereof not in the conditioned space
should be properly insulated in order to both conserve
energy and prevent condensation or moisture damage.
Refer to Maximum ESP of Operation Electric Heat Only
Table 5 on page 23.
Design the duct work according to methods given by
the Air Conditioning Contractors of America (ACCA).
When duct runs through unheated spaces, it should be
insulated with a minimum of one inch of insulation.
Use insulation with a vapor barrier on the outside of the
insulation. Flexible joints should be used to connect
the duct work to the equipment in order to keep the
noise transmission to a minimum.
For model series W3R/LV, W5R/LV and W6R/LV a 1/4
inch clearance to combustible material for the first
three feet of duct attached to the outlet air frame is
required. See Wall Mounting Instructions and Figures
3A, 3B and 4 for further details.
Ducts through the walls must be insulated and all
joints taped or sealed to prevent air or moisture
entering the wall cavity.
Some installations may not require any return air duct.
A metallic return air grille is required with installations
not requiring a return air duct. The spacing between
louvers on the grille shall not be larger than 5/8 inch.
Any grille that meets with 5/8 inch louver criteria may
be used. It is recommended that Bard Return Air
Grille Kit RG2 through RG5 or RFG2 through RFG5
be installed when no return duct is used. Contact
distributor or factory for ordering information. If using
a return air filter grille, filters must be of sufficient size
to allow a maximum velocity of 400 fpm.
NOTE:
If no return air duct is used, applicable
installation codes may limit this cabinet to
installation only in a single story structure.
FIGURE 1
FRESH AIR DAMPER
Summary of Contents for W3LV2-R
Page 2: ......
Page 27: ......
Page 34: ......
Page 43: ......
Page 46: ......
Page 68: ......
Page 74: ...Manual 2100 479 Page 6 of 11 FIGURE 1 TYPICAL AIR CONDITIONING SYSTEM COOLING CYCLE MIS 369...
Page 75: ...Manual 2100 479 Page 7 of 11 FIGURE 2 TYPICAL HEAT PUMP SYSTEM COOLING CYCLE MIS 368...
Page 80: ......
Page 82: ...Manual 2110 1418G Page 2 of 16 CABINET COMPONENTS RIGHT EXTREME DUTY DOOR...
Page 84: ...Manual 2110 1418G Page 4 of 16 CABINET COMPONENTS RIGHT MODERATE DUTY DOOR...
Page 86: ...Manual 2110 1418G Page 6 of 16 CABINET COMPONENTS LEFT EXTREME DUTY DOOR...
Page 88: ...Manual 2110 1418G Page 8 of 16 CABINET COMPONENTS LEFT MODERATE DUTY DOOR...
Page 97: ......
Page 100: ......