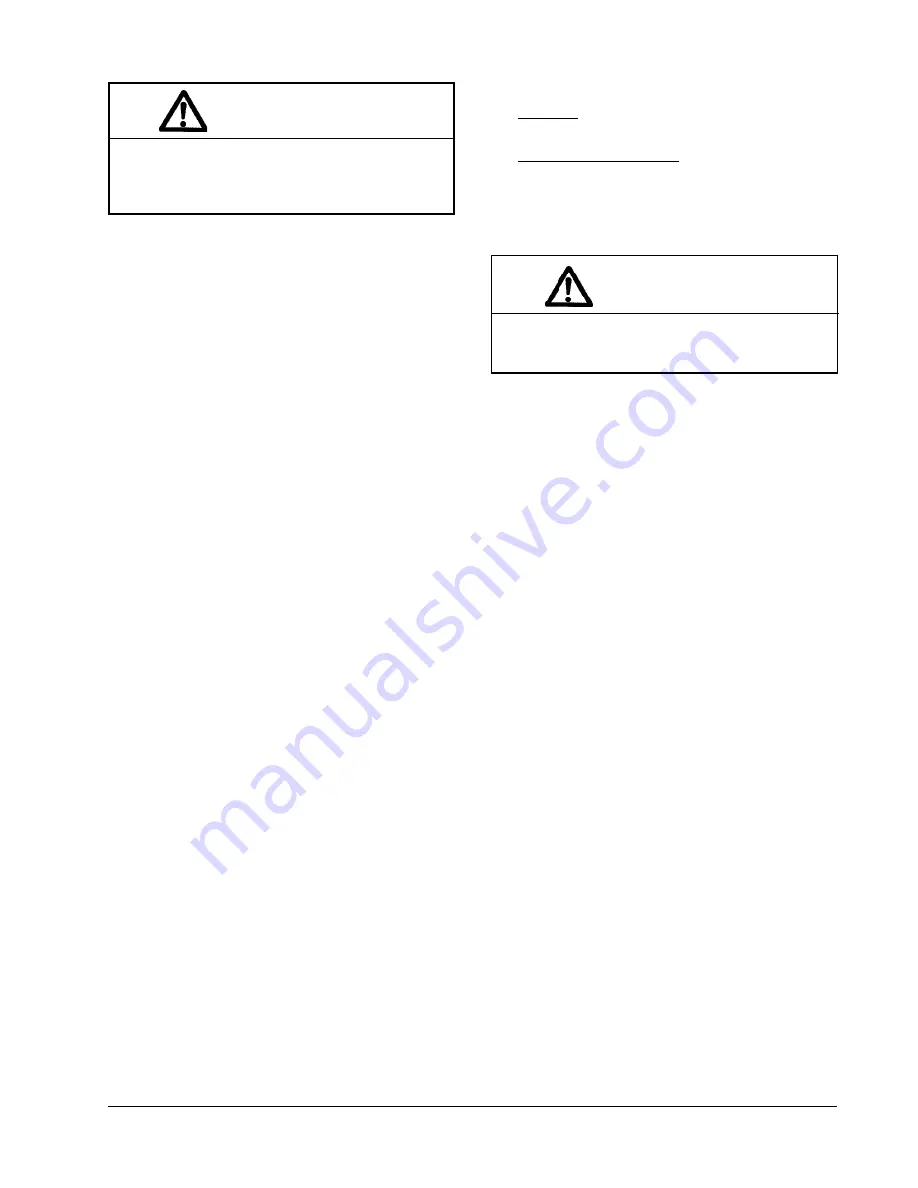
Manual 2100-721B
Page
39 of 54
Routine Maintenance
1. Air Filters – Check the condition at least monthly
when the unit is in use, and replace as necessary.
2. Lubrication Requirements – The indoor circulating
air blower motor and outdoor circulating air fan
motor are permanently lubricated and requires
no re-oiling. The combustion air blower motor
requires no re-oiling.
Routine Inspection
1. Inspect the physical support of the unit annually to
make sure it is securely fastened to the building.
Also look for any obvious signs of deterioration.
2. Inspect the main burners at the beginning of each
heating season and clean as necessary.
3. Inspect the vent terminal and combustion air
intake hood for any obvious deterioration, to make
sure it is free and clear of any obstructions.
30. TROUBLESHOOTING NIDEC
SELECTECH SERIES ECM MOTORS
If the Motor Is Running
1. It is normal for the motor to rock back and forth
on start up. Do not replace the motor if this is the
only problem identified.
2. If the system is excessively noisy, does not appear
to change speeds in response to a demand (Heat,
Cool, Other) or is having symptoms during the
cycle such as tripping limit or freezing coil, check
the following:
A. Wait for programmed delays to time out.
B. Ensure that the motors control inputs are
wired as shown in the factory-supplied wiring
diagram to ensure motor is getting proper
control signals and sequencing.
C. Remove the filter and check that all dampers,
registers and grilles are open and free flowing.
If removing the filters corrects the problem,
clean or replace with a less restrictive filter.
Also check and clean the blower wheel or coil
as necessary.
Annual Maintenance
Routine inspection and maintenance procedures are
the responsibility of the user and are outlined below.
1. Before inspecting unit:
A. Turn room thermostat to lowest or off setting.
B. Turn off equipment gas shut-off valve.
C. Wait for unit to cool if it was recently
operating.
D. Turn off electrical power to unit.
2. Inspect the following:
A. Vent terminal and combustion air intake
terminal. Make sure both are free from
obstructions.
B. Vertical vent applications – Inspect venting
system. Make sure system has no holes, is
physically sound and free from obstructions.
C. Make sure the supply and return air flange
sleeves or duct work are securely fastened to
unit and physically sound.
D. Supply and return grilles must be open and
free from obstructions.
E. Inspect to make sure the unit is securely
fastened to the wall. Seal any possible leaks
between unit and wall with appropriate exterior
sealing material.
F. Inspect burners, heat exchanger, induced draft
blower and induced draft blower collector
box. There must be no obvious signs of
deterioration.
G. Inspect all electrical connections and wiring.
H. Check all gas piping for leaks with soap
solution used to detect leaks.
I. Inspect, clean and repair as needed the entire
blower assembly, air filters, draft inducer,
cooling coils and vent options (if installed).
WARNING
Disconnect electrical power before servicing
unit. Failure to do so could result in electrical
shock or death.
WARNING
Turn off electrical power supply to prevent injury
from moving parts or electric shock.