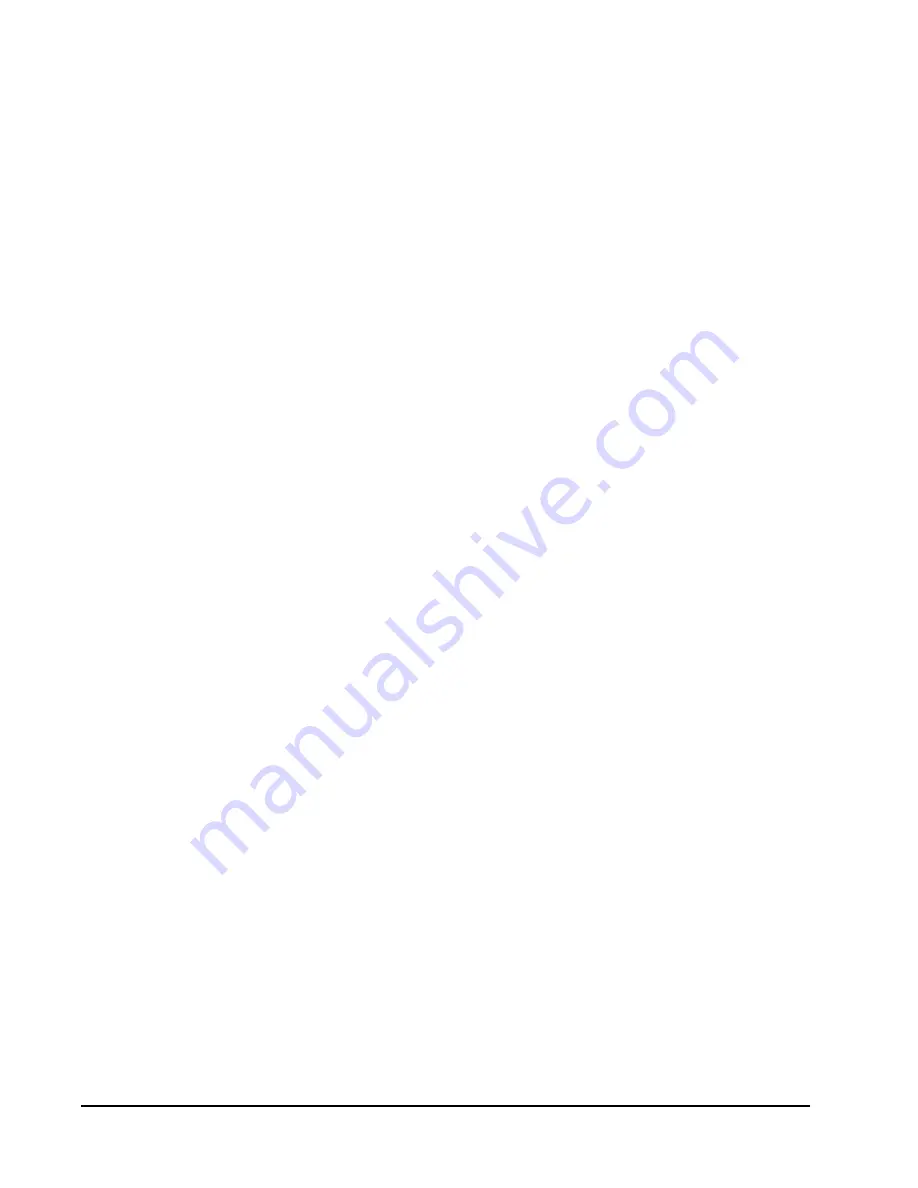
Manual 2100-703
Page
8 of 40
Unit Installation
Make sure to have the proper tools at the work site that
are needed for unit installation. The following steps
are provided to ensure the unit is installed properly to
the wall surface, and that the unit will provide years of
service with minimal service requirements.
Materials/Tools List
Additional hardware and miscellaneous supplies are
needed for installation. These items are field supplied
and must be sourced before installation. This list also
includes tools needed for installation.
• Appropriate safety gear including gloves and safety
glasses
• 5/16" hex bit with drill driver
• Phillips head screwdriver
• Small straight (thermostat) screwdriver
• Tape measure
• Leveling device
• Two (2) tubes of caulk and caulk gun
• Utility knife
• Tools for cutting holes in the wall surface (if
needed)
• Electrical components and wiring along with
electrical tools
• Multimeter
• Wall fasteners for side flanges, bottom mounting
bracket and top rain flashing.
• Duct tape and/or other duct sealing materials.
Wall Preparation
1. Two holes for the supply and return air openings
must be cut through the wall as shown in
Figures 3A and 3B on pages 10 and 11. Be sure
the openings are square and level. Follow all
clearances including distances to combustible
materials and all instructions provided in this
manual.
2. Review all electrical requirements provided in this
manual and plan out electrical entrances into the
building. Also plan electrical conduit routing and
thermostat placement, if necessary.
3. Install necessary duct work and prepare the
openings for unit installation.
4. Clean the exterior wall where the unit is to be
installed and make sure it is able to provide a
smooth, level, debris-free surface. Remove all
construction debris from the supply, return and
electrical hole cutting process.
Wall Mount Installation to Wall Surface
1. Remove packaging from unit and make sure unit
is not damaged before installation. A top rain
flashing is supplied for field use and is mounted
to the back of the unit for shipping. Remove rain
flashing before locating the unit against wall. Top
rain flashing is required to avoid water entering
the area behind the unit that is against the wall. A
bottom mounting bracket, attached to the skid for
shipping, is provided for ease of installation but is
not required. Review all requirements listed on unit
labels and on serial plate located on the side of the
unit.
2. Locate and mark bolt hole locations and bottom
mounting bracket location. Install bottom mounting
bracket with field-supplied fasteners to wall if it is
to be used (optional). Bracket must be level and
installed in the correct location to help support the
unit during the installation process (see Figures 3A
and 3B).
3. Position the wall mount unit close to the wall
surface where it will be installed. Install rain
flashing at the top of the unit facing the wall by
hooking the hem bend into the rear bend of the
unit top (see Figures 3A and 3B).
4. Apply a liberal amount of caulk on left and right
cabinet side wall mount brackets and back of
top rain flashing. Place unit back surface flush
against wall. Unit must be level to ensure proper
condensate drainage. Optional bottom bracket may
be used to help support the unit.
5. Units are secured to the wall by using field-
supplied fasteners along each side of the wall
mount through the built-in wall mounting brackets.
It is the responsibility of the installer to select the
proper fastener to secure the unit to the wall based
on wall construction and applicable building codes.
Typical installations may include 5/16" fasteners
with 7/8" diameter flat washers. Be sure unit is
securely mounted and all weight-bearing fasteners
are attached to the weight supporting structural
members of the wall.
6. Apply a bead of caulk between the back of the unit
top and the front surface of the top rain flashing
(see Figures 3A and 3B).
7. Connect unit duct work from the inside of the
building following all clearances and instructions
provided. For additional mounting rigidity, the
return air and supply air frames or collars can be
drilled and screwed or welded to the structural wall
itself (depending upon wall construction). Be sure
to use code approved duct tape or other sealing
materials to seal the duct work to the unit.
8. On side-by-side installations, maintain a minimum
of 20" clearance on right side to allow access to
control panel and heat strips, and to allow proper
airflow to the outdoor coil. Additional clearance
may be required to meet local or national codes.