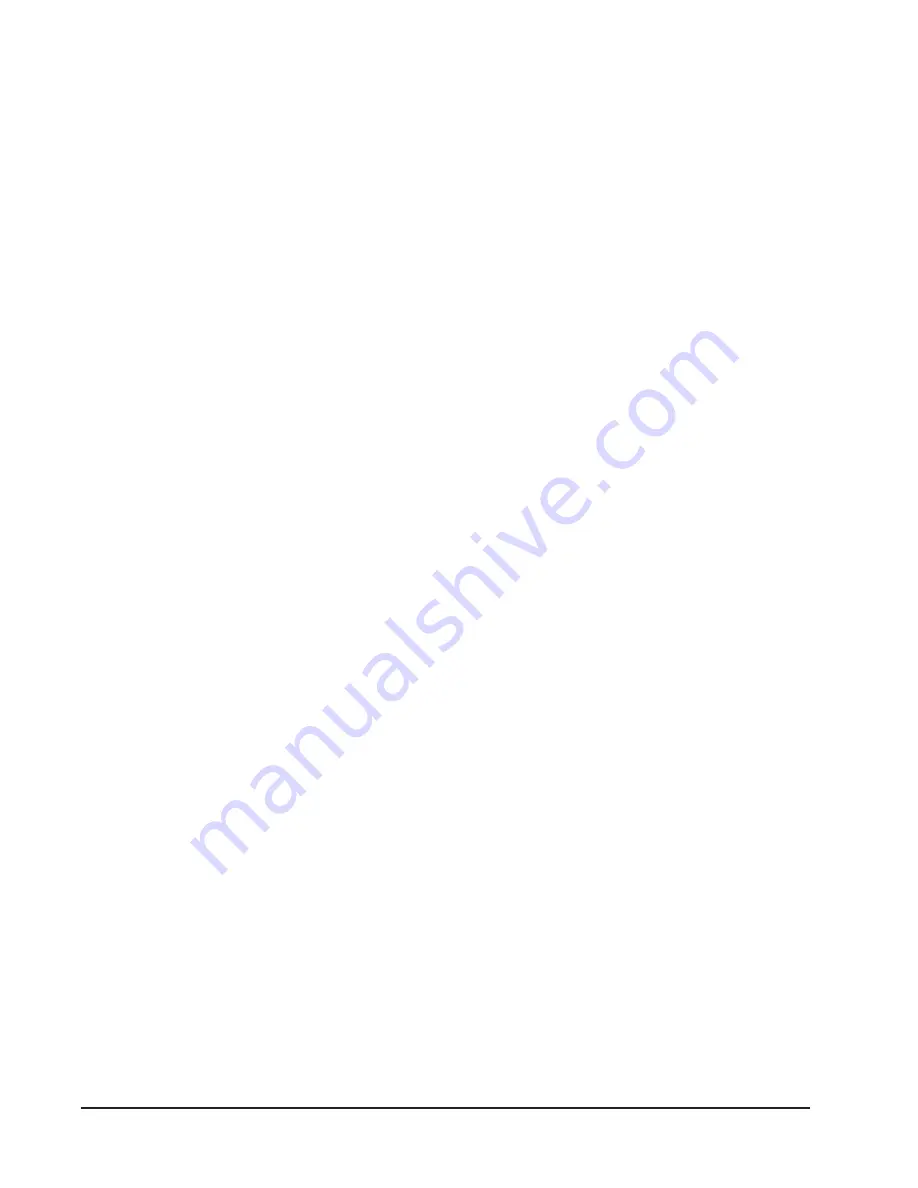
Manual 2100-737A
Page
16 of 25
IMPORTANT INSTALLER NOTE
For improved start up performance wash the indoor coil
with a dish washing detergent.
HIGH AND LOW PRESSURE SWITCH
All T**S wall mounted air conditioner series models
are supplied with a remote reset for the high and low
pressure switch. If tripped, this pressure switch may
be reset by turning the thermostat off then back on
again.
THREE PHASE SCROLL COMPRESSOR
START UP INFORMATION
Scroll compressors, like several other types of
compressors, will only compress in one rotational
direction. Direction of rotation is not an issue with
single phase compressors since they will always start
and run in the proper direction.
However, three phase compressors will rotate in either
direction depending upon phasing of the power.
Since there is a 50-50 chance of connecting power
in such a way as to cause rotation in the reverse
direction, verification of proper rotation must be made.
Verification of proper rotation direction is made by
observing that suction pressure drops and discharge
pressure rises when the compressor is energized.
Reverse rotation also results in an elevated sound level
over that with correct rotation, as well as substantially
reduced current draw compared to tabulated values.
Verification of
proper rotation
must be made at the
time the equipment is put into service. If improper
rotation is corrected at this time, there will be no
negative impact on the durability of the compressor.
However, reverse operation for over 1 hour may have a
negative impact on the bearing due to oil pump out.
NOTE:
If compressor is allowed to run in reverse
rotation for an extended period of time, the
compressor’s internal protector will trip.
All three phase ZP compressors are wired identically
internally. As a result, once the correct phasing
is determined for a specific system or installation,
connecting properly phased power leads to the same
Fusite terminal should maintain proper rotation
direction.
The direction of rotation of the compressor may be
changed by reversing any two line connections to the
unit.
PHASE MONITOR
All units with three phase scroll compressors are
equipped with a three phase line monitor to prevent
compressor damage due to phase reversal.
The phase monitor in this unit is equipped with two
LEDs. If the Y signal is present at the phase monitor
and phases are correct the green LED will light.
If phases are reversed, the red fault LED will be lit and
compressor operation is inhibited.
If a fault condition occurs, reverse two of the supply
leads to the unit.
Do not reverse any of the unit factory
wires as damage may occur.
SERVICE HINTS
1. Caution owner/operator to maintain clean air filters
at all times and to not needlessly close off supply
and return air registers. This reduces airflow
through the system, which shortens equipment
service life as well as increasing operating costs.
2. Check all power fuses or circuit breakers to be sure
they are the correct rating.
3. Periodic cleaning of the outdoor coil to permit full
and unrestricted airflow circulation is essential.
SEQUENCE OF OPERATION
Cooling
Circuit R-Y makes at thermostat pulling in compressor
contactor, starting the compressor and outdoor motor.
The G (indoor motor) circuit is automatically completed
on any call for cooling operation or can be energized
by manual fan switch on subbase for constant air
circulation.
Heating
A 24V solenoid coil on reversing valve controls heating
cycle operation. Two thermostat options, one allowing
“Auto” changeover from cycle to cycle and the other
constantly energizing solenoid coil during heating
season and thus eliminating pressure equalization
noise except during defrost, are to be used. On “Auto”
option a circuit is completed from R-B and R-Y on
each heating “on” cycle, energizing reversing valve
solenoid and pulling in compressor contactor starting
compressor and outdoor motor. R-G also make starting
indoor blower motor. Heat pump heating cycle now in
operation. The second option has no “Auto” changeover
position, but instead energizes the reversing valve
solenoid constantly whenever the system switch on
subbase is placed in “Heat” position, the “B” terminal
being constantly energized from R. A thermostat
demand for Stage 1 heat completes R-Y circuit, pulling
in compressor contactor starting compressor and outdoor
motor. R-G also make starting indoor blower motor.