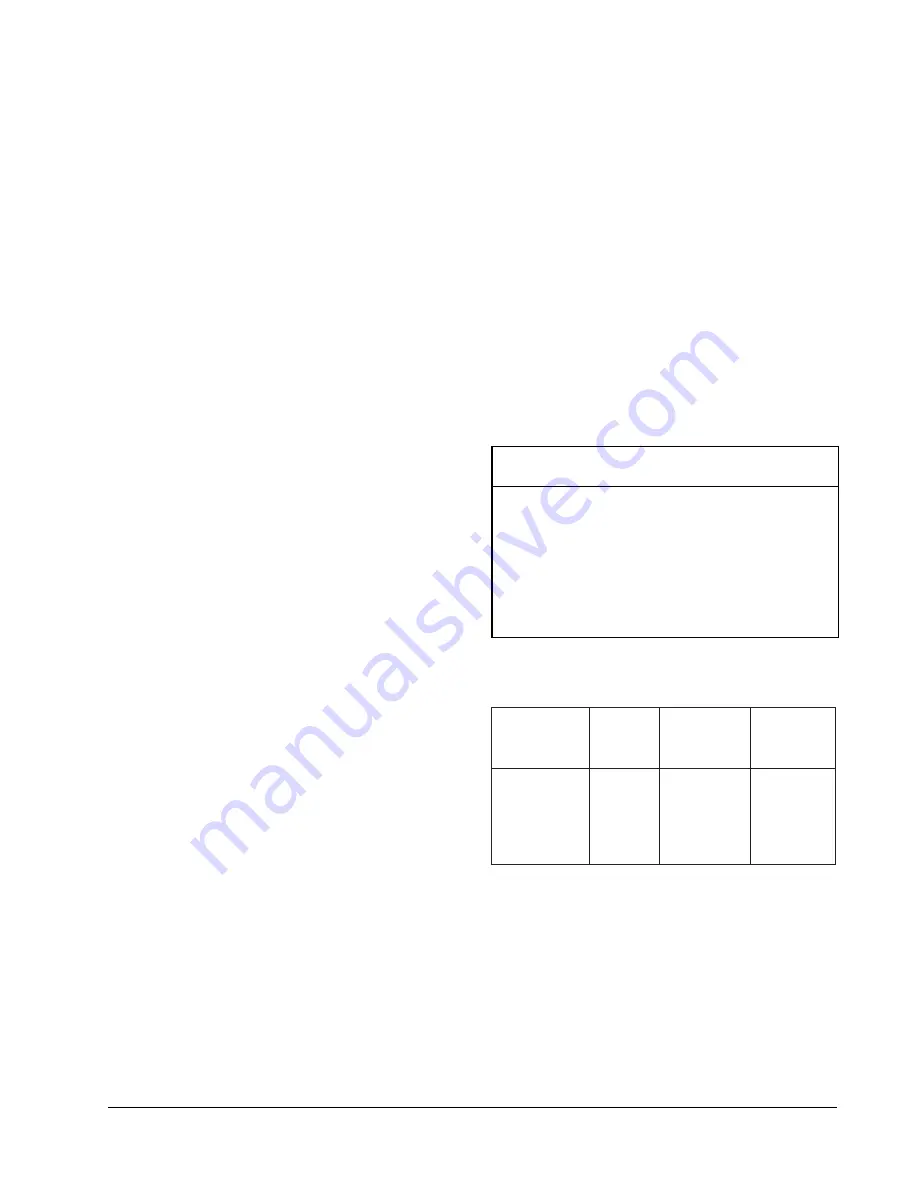
Manual 2100-414C
Page
11
WIRING – MAIN POWER
Refer to the unit rating plate for wire sizing
information and maximum fuse or “HACR” type
circuit breaker size. Each outdoor unit is marked
with a “Minimum Circuit Ampacity”. This
means that the field wiring used must be sized to
carry that amount of current. Depending on the
installed KW of electric heat, there may be two
field power circuits required. If this is the case,
the unit serial plate will so indicate. All models
are suitable only for connection with copper wire.
Each unit and/or wiring diagram will be marked
“Use Copper Conductors Only”. These
instructions
must be
adhered to. Refer to the
National Electrical Code (NEC) for complete
current carrying capacity data on the various
insulation grades of wiring material. All wiring
must conform to NEC and all local codes.
The electrical data lists fuse and wire sizes (75° C
copper) for all models including the most
commonly used heater sizes. Also shown are the
number of field power circuits required for the
various models with heaters.
The unit rating plate lists a “Maximum Time
Delay Relay Fuse” or “HACR” type circuit
breaker that is to be used with the equipment. The
correct size must be used for proper circuit
protection and also to assure that there will be no
nuisance tripping due to the momentary high
starting current of the compressor motor.
The disconnect access door on this unit may be
locked to prevent unauthorized access to the
disconnect. To convert for the locking capability,
bend the tab locate in the bottom left hand corner
of the disconnect opening under the disconnect
access panel straight out. This tab will now line
up with the slot in the door. When shut, a
padlock may be placed through the hole in the tab
preventing entry.
See “Start Up” section for important information
on three phase scroll compressor start ups.
IMPORTANT
WIRING – LOW VOLTAGE WIRING
230 / 208V, 1 phase and 3 phase equipment dual
primary voltage transformers. All equipment leaves the
factory wired on 240V tap. For 208V operation,
reconnect from 240V to 208V tap. The acceptable
operating voltage range for the 240 and 208V taps are:
TAP
RANGE
240
253 – 216
208
220 – 187
NOTE: The voltage should be measured at the field
power connection point in the unit and while
the unit is operating at full load (maximum
amperage operating condition)
Nine (9) wires should be run from thermostat subbase to
the 24V terminal board in the unit. A nine conductor,
18 gauge copper color-coded thermostat cable is
recommended. The connection points are shown in
Figure 9.
TABLE 3
THERMOSTAT WIRE SIZE
r
e
m
r
o
f
s
n
a
r
T
A
V
A
L
F
e
g
u
a
G
e
r
i
W
m
u
m
i
x
a
M
e
c
n
a
t
s
i
D
t
e
e
F
n
i
5
5
3
.
2
e
g
u
a
g
0
2
e
g
u
a
g
8
1
e
g
u
a
g
6
1
e
g
u
a
g
4
1
e
g
u
a
g
2
1
5
4
0
6
0
0
1
0
6
1
0
5
2
Only the thermostat and subbase
combinations as shown in this manual are
assured by Bard to work with this equipment.
The thermostat and subbase
must
be
matched, and the correct operation can be
assured only by proper selection and
application of these parts.