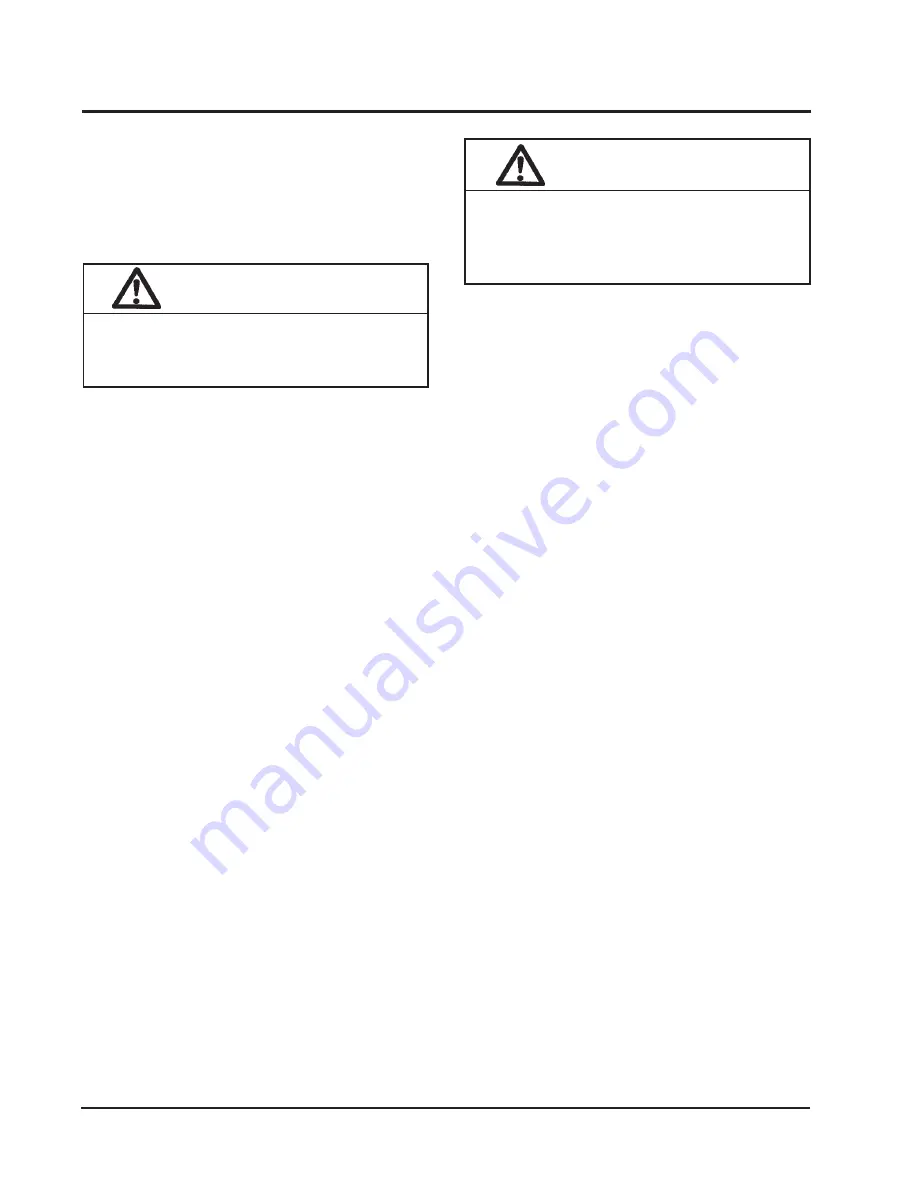
Manual 2100-411G
Page
8 of 23
INSTALLATION INSTRUCTIONS
WALL MOUNTING INFORMATION
1. Two holes for the supply and return air openings
must be cut through the wall as shown in Figure 3.
2. On wood frame walls, the wall construction must be
strong and rigid enough to carry the weight of the
unit without transmitting any unit vibration.
3. Concrete block walls must be thoroughly inspected
to insure that they are capable of carrying the weight
of the installed unit.
MOUNTING THE UNIT
1. These units are secured by wall mounting brackets,
which secure the unit to the outside wall surface at
both sides. A bottom mounting bracket is provided
for ease of installation, but is not required.
2. The unit itself is suitable for 0 inch clearance, but
the supply air duct flange and the first 3 feet of
supply air duct require a minimum of 1/4 inch
clearance to combustible material. If a combustible
wall, use a minimum of 30½" x 10½" dimensions for
sizing. However, it is generally recommended that a
1-inch clearance is used for ease of installation and
maintaining the required clearance to combustible
material. The supply air opening would then be
32" x 12". See Figures 3 and 4 for details.
3. Locate and mark lag bolt locations and bottom
mounting bracket location. See Figure 3.
4. Mount bottom mounting bracket.
5. Hook top rain flashing under back bend of top. Top
rain flashing is shipped with unit attached to back of
unit on the right side.
6. Position unit in opening and secure with 5/16 lag
bolts; use 3/4 inch diameter flat washers on the lag
bolts.
7. Secure rain flashing to wall and caulk across entire
length of top. See Figure 3.
8. For additional mounting rigidity, the return air and
supply air frames or collars can be drilled and
screwed or welded to the structural wall itself
(depending upon wall construction). Be sure to
observe required clearance if combustible wall.
9. On side-by-side installations, maintain a minimum
of 20 inches clearance on right side to allow access
to control panel and heat strips, and to allow proper
airflow to the outdoor coil. Additional clearance
may be required to meet local or national codes.
WARNING
Fire hazard can result if 1/4 inch clearance to
combustible materials for supply air duct is
not maintained. See Figure 4.
WARNING
Failure to provide the 1/4 inch clearance
between the supply duct and a combustible
surface for the first 3 feet of duct can result in
fire causing property damage, injury or death.