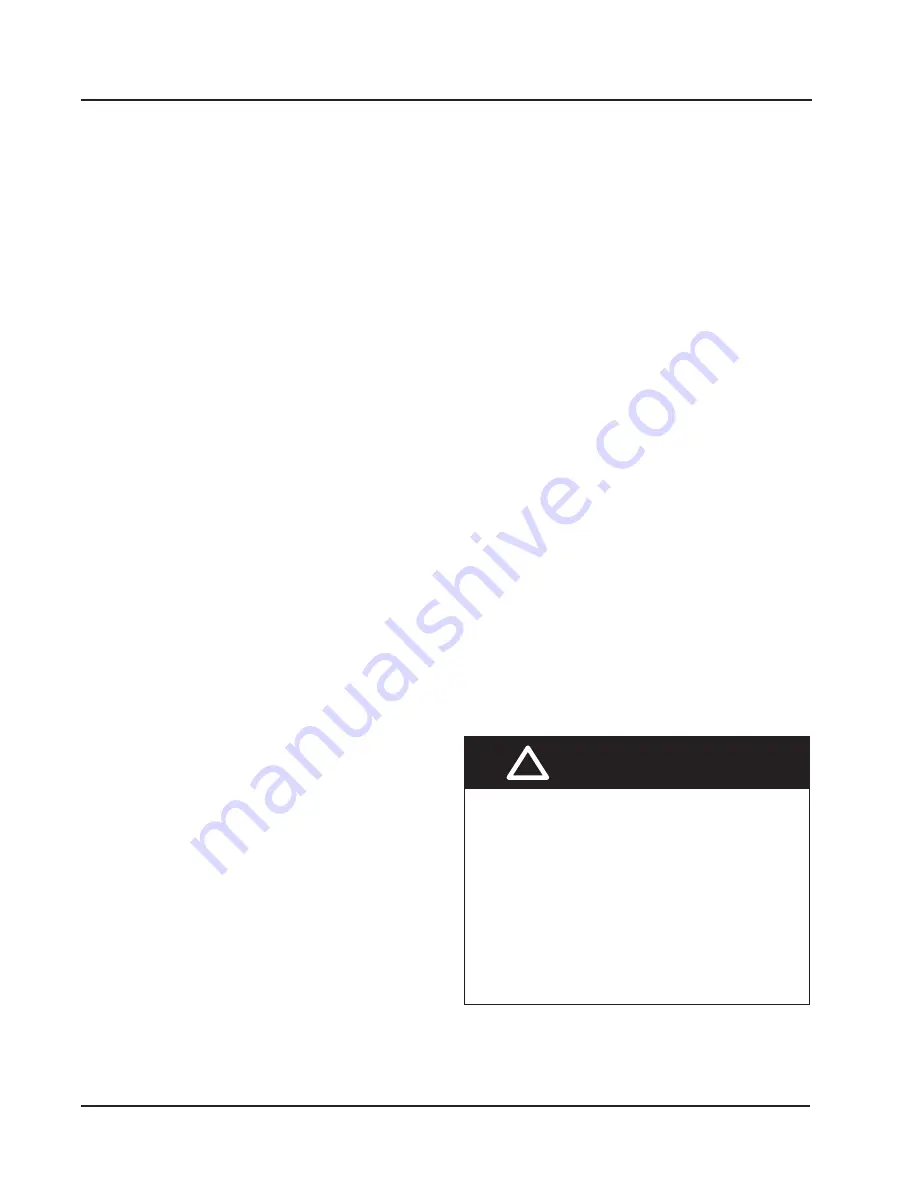
Manual 2100-742B
Page
46 of 57
!
WARNING
Exposure to high pressure refrigerant hazard.
This unit is equipped with an electronic
expansion valve (EEV). In order to fully
recover refrigerant or evacuate system during
repairs, either use service tool P/N 2151-
021 to manually open the EEV or be sure to
recover and evacuate from all service ports:
suction, liquid and discharge.
Failure to do so could result in eye injuries
and/or refrigerant burns.
DO NOT connect to the high pressure service port on
the front of the unit with the RED circular label. This
connection point is under very high pressure and could
cause injury and/or refrigerant burns.
DEHUMIDIFICATION UNIT INSTRUCTIONS
Q**H4D dehumidification models provide a unique
dehumidification circuit for periods of low outdoor
ambient temperature and high indoor humidity
conditions.
Refer to Spec Sheet S3607 for the standard features of
the base units and this manual for electrical data.
Dehumidification Circuit
The dehumidification circuit incorporates an
independent heat exchanger coil in the supply air
stream. This coil uses discharge gas to reheat the
supply air after it passes over the cooling coil without
requiring the electric resistance heater to be used for
reheat purposes. This results in very high mechanical
dehumidification capability from the air conditioner on
demand without using electric resistance reheat.
The dehumidification refrigerant reheat circuit is
controlled by a dehumidification valve directing
the refrigerant gas to the normal condenser during
periods when standard air conditioning is required.
During periods of time of low ambient temperature
(approximately 65° to 75° outdoor) and high indoor
humidity, a humidistat senses the need for mechanical
dehumidification. It then energizes both the compressor
circuit and dehumidification valve, thus directing
the hot refrigerant discharge gas into a separate
desuperheating condenser circuit, which reheats the
conditioned air before it is delivered to the room. The
refrigerant gas is then routed from the desuperheating
condenser to the system condenser for further heat
transfer. When the humidistat is satisfied, the system
automatically switches back to normal operation and
either continues to operate or turns off based on the
signal from the wall thermostat. The result is separate
humidity control at minimum operating cost.
Dehumidification Sequence of
Operation
Dehumidification is controlled through the thermostat
(if capable) or through a separate humidistat. On a call
for dehumidification mode of operation, the compressor
and dehumidification valve of the unit are energized
through circuit R - D to provide dehumidification.
Dehumidification will continue until the humidistat is
satisfied.
Any time there is a call for circuit R - Y1, the
dehumidification mode will cancel and the system will
return to cooling or heat pump operation.
Balanced Climate
TM
Mode
Enable Balanced Climate mode for cooling operation
ONLY and utilize a 2-stage thermostat to enhance the
comfort. To activate this mode, the jumpers between Y1
and Y2 on both low voltage terminal strips (blower section
and control panel) need to be removed. Refer to unit
wiring diagram for clarity.
This mode will allow the indoor blower to run at a
reduced airflow on the first stage of cooling. A 2-stage
thermostat connected to Y2 will then allow the airflow
to return to normal rated speed if the call for cooling is
not satisfied within the allotted time frame specified by
the thermostat.
Electronic Expansion Valve
Operation
This model employs an electronic expansion valve
(EEV) which meters the refrigerant to the evaporator.
In the heat pump application, the EEV is used bi-
directionally to meter the refrigerant in both heating
and cooling modes. The EEV is made of a stepper
motor that is controlled with a step output from the
controller. The valve is capable of 480 steps which
drives a needle valve that in turn regulates the flow of
refrigerant. The EEV allows for tighter control and better
capacity management in varying operating conditions
than a standard TXV. The EEV system consists of the
electronic valve and stator, control board, relay, suction
temperature sensor and suction pressure transducer.
The pressure transducer and temperature sensor
monitor the suction line to provide real time data to
the control board so that a real time superheat can be
calculated. This then determines the EEV position. The
controller is set to maintain around 19° superheat. The
relay is used to activate the EEV system’s controller
anytime that the compressor is energized.
EEV Instructions for Vacuuming, Reclaiming and
Charging Unit