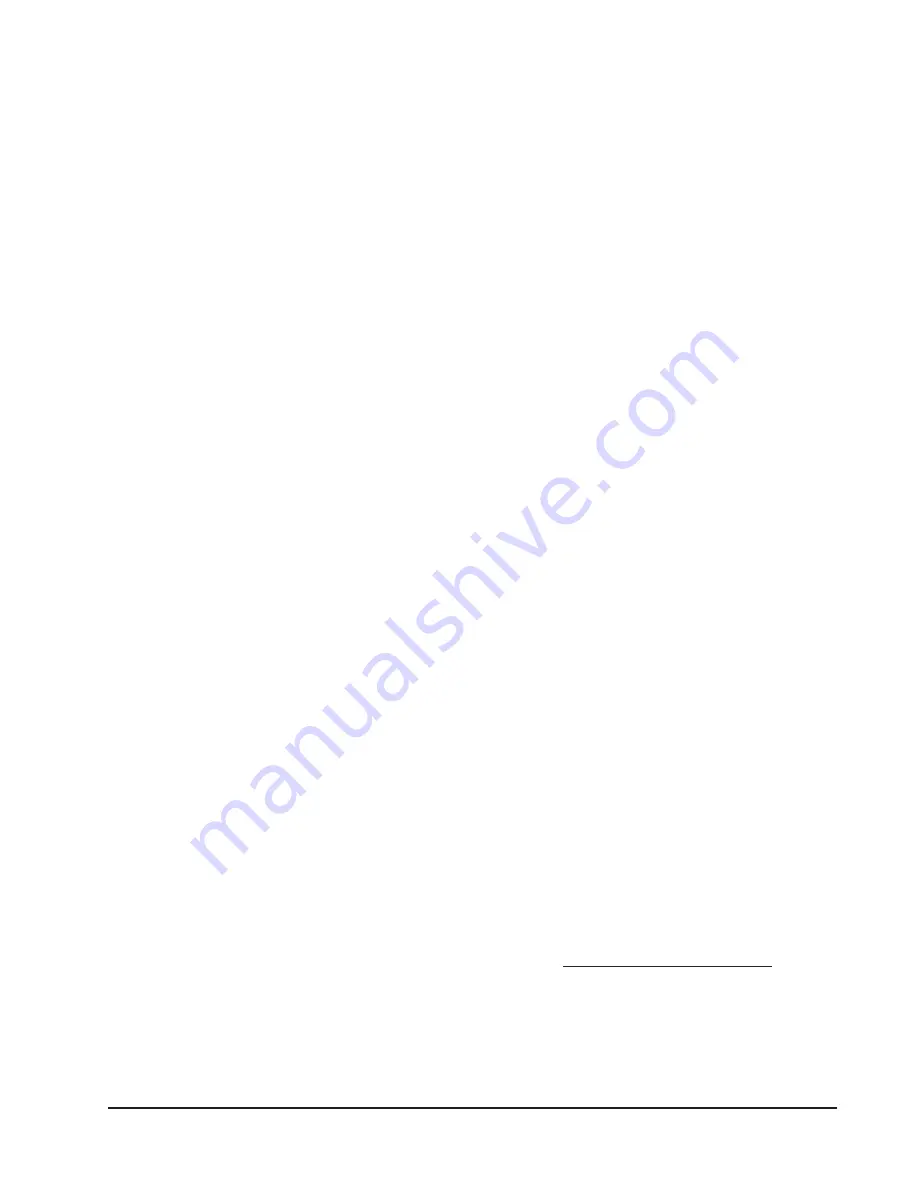
Manual 2100-586G
Page
15 of 25
Since there is a 50-50 chance of connecting power
in such a way as to cause rotation in the reverse
direction, verification of proper rotation must be made.
Verification of proper rotation direction is made by
observing that suction pressure drops and discharge
pressure rises when the compressor is energized.
Reverse rotation also results in an elevated sound level
over that with correct rotation, as well as substantially
reduced current draw compared to tabulated values.
Verification of
proper rotation
must be made at the time
the equipment is put into service. If improper rotation
is corrected at this time, there will be no negative
impact on the durability of the compressor. However,
reverse operation for over 1 hour may have a negative
impact on the bearing due to oil pump out.
NOTE:
If compressor is allowed to run in reverse
rotation for an extended period of time, the
compressor’s internal protector will trip.
All three phase ZP compressors are wired identically
internally. As a result, once the correct phasing is
determined for a specific system or installation,
connecting properly phased power leads to the same
Fusite terminal should maintain proper rotation
direction.
The direction of rotation of the compressor may be
changed by reversing any two line connections to the
unit.
Phase Monitor
All units with three phase scroll compressors are
equipped with a three phase line monitor to prevent
compressor damage due to phase reversal.
The phase monitor in this unit is equipped with two
LEDs. If the Y signal is present at the phase monitor
and phases are correct, the green LED will light.
If phases are reversed, the red fault LED will be lit and
compressor operation is inhibited.
If a fault condition occurs, reverse two of the supply
leads to the unit.
Do not reverse any of the unit factory
wires as damage may occur.
Service Hints
1. Caution owner/operator to maintain clean air filters
at all times and also not to needlessly close off
supply and return air registers. This reduces airflow
through the system, which shortens equipment
service life as well as increasing operating costs.
2. Check all power fuses or circuit breakers to be sure
they are the correct rating.
3. Periodic cleaning of the outdoor coil to permit full
and unrestricted airflow circulation is essential
.
Sequence of Operation
Cooling Stage 1
– Circuit R-Y makes at thermostat
pulling in compressor contactor, starting the
compressor and outdoor motor. The G (indoor motor)
circuit is automatically completed on any call for
cooling operation or can be energized by manual fan
switch on subbase for constant air circulation.
Cooling Stage 2
– Circuit R-Y1 makes at the
thermostat, energizing the 2nd stage solenoid in
the compressor. Default position is not energized.
Compressor will run at low capacity until this solenoid
is energized.
Heating Stage 1
– A 24V solenoid coil on reversing
valve controls heating cycle operation. Two thermostat
options, one allowing “Auto” changeover from cycle to
cycle and the other constantly energizing solenoid coil
during heating season and thus eliminating pressure
equalization noise except during defrost, are to be
used. On “Auto” option, a circuit is completed from
R-B and R-Y on each heating “on” cycle, energizing
reversing valve solenoid and pulling in compressor
contactor starting compressor and outdoor motor. R-G
also make, starting indoor blower motor. Heat pump
heating cycle now in operation. The second option has
no “Auto” changeover position, but instead energizes
the reversing valve solenoid constantly whenever the
system switch on subbase is placed in “Heat” position,
the “B” terminal being constantly energized from R.
A thermostat demand for Stage 1 heat completes R-Y
circuit, pulling in compressor contactor and starting
compressor and outdoor motor. R-G also make, starting
indoor blower motor.
Heating Stage 2
– Circuit R-Y2 makes at the thermostat,
energizing the 2nd stage solenoid in the compressor.
Pressure Service Ports
High and low pressure service ports are installed on
all units so that the system operating pressures can be
observed. Pressure tables 6A and 6B cover all models.
It is imperative to match the correct pressure table to
the unit by model number.
This unit employs high-flow Coremax valves instead of
the typical Shrader type valves.
WARNING! Do NOT use a Schrader valve core removal
tool with these valves. Use of such a tool could result in
eye injuries or refrigerant burns!
To change a Coremax valve without first removing the
refrigerant, a special tool is required which can be
obtained at www.fastestinc.com/en/SCCA07H. See the
replacement parts manual for replacement core part
numbers.