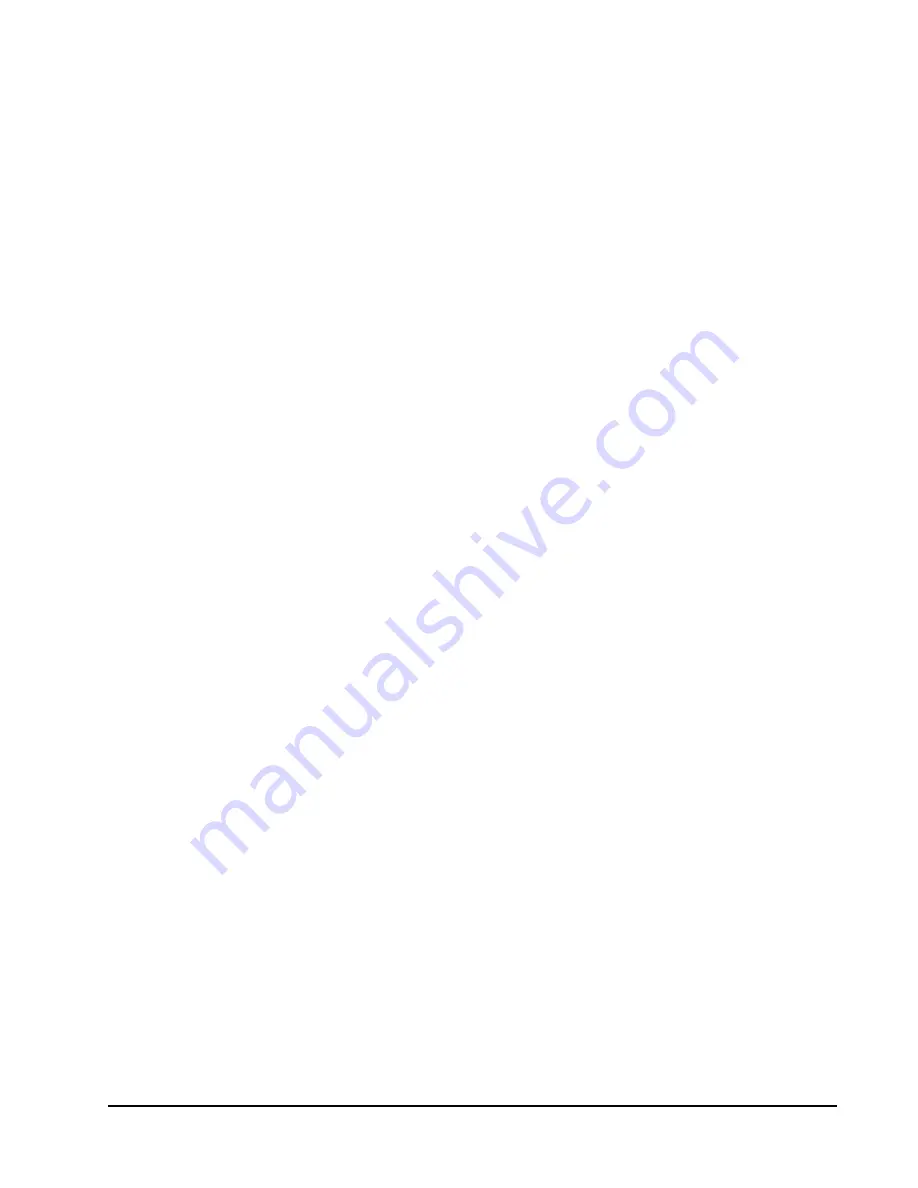
Manual 2100-715B
Page
13 of 25
Wiring – Main Power
Main electrical power must be supplied to the unit
from a clean, reliable power source. Verify voltage being
supplied to the unit is consistent during all times of the
day and within the range specified for the unit in the
unit specifications and on the unit serial plate. Voltage
must be measured at the field power connection point
in the unit and while the unit is operating at full load
(maximum amperage operating condition).
Refer to the unit serial plate and unit specifications
for wire sizing information and maximum fuse or
circuit breaker size. Each outdoor unit is marked with
a “Minimum Circuit Ampacity”. This means that the
field wiring used must be sized to carry that amount
of current. Depending on the installed KW of electric
heat, there may be two field power circuits required. If
this is the case, the unit serial plate will so indicate.
All models are suitable only for connection with copper
wire. Each unit and/or wiring diagram will be marked
“Use Copper Conductors Only”. These instructions
must be adhered to. Refer to the National Electrical
Code (NEC) for complete current carrying capacity data
on the various insulation grades of wiring material. All
wiring must conform to NEC and all local codes.
The electrical data on the serial plate, in the unit
specifications and also in Table 8 on page 23 list fuse
and wire sizes (75°C copper) for all models including
the most commonly used heater sizes. Also shown are
the number of field power circuits required for the
various models with heaters. The unit rating plate lists
a “Maximum Time Delay Relay Fuse” or circuit breaker
that is to be used with the equipment. The correct type
and size must be used for proper circuit protection and
also to ensure that there will be no nuisance tripping
due to the momentary high starting current of the
compressor motor.
Wiring – Low Voltage
All 230/208V 1 phase and 3 phase equipment have
dual primary voltage transformers. All equipment leaves
the factory wired on 240V tap. For 208V operation,
reconnect from 240V to 208V tap. The acceptable
operating voltage range for the 240 and 208V taps are:
Tap: 240
Range: 253 – 216
Tap: 208
Range: 220 – 187
NOTE:
The voltage should be measured at the field
power connection point in the unit and while
the unit is operating at full load (maximum
amperage operating condition).
For low voltage wiring, an 18 gauge copper, color-coded
cable is recommended. See Table 4 on page 14 for
more information.
Low Voltage (24VAC) Connections
These units use a 24-volt AC low voltage circuit.
C
terminal is the
24VAC common and is grounded.
G
terminal is the
indoor blower input
.
Y1
terminal is the
1st Stage input for cooling.
Y2
terminal is the
2nd Stage compressor input for cooling
(if equipped with an economizer) or
Y2 disables Balanced
Climate mode if the Y1-Y2 jumper is removed
B/W1
terminal is the
1st stage electric heat
.
A
terminal is the
ventilation input
. This terminal
energizes any factory-installed ventilation option and
indoor blower.
L
terminal is
24 volt alarm active output
.
For units equipped with an alarm relay:
1 terminal
is the
normally closed contact on the relay.
2 terminal
is the
normally open contact on the relay.
3 terminal
is the
common contact on the relay.
Unit Shutdown Feature (Standard on All Models)
The RT terminal is the 24VAC transformer output,
and the R terminal is the 24VAC hot terminal for the
operation of the equipment. RT and R are connected
with a brass jumper bar which can be removed and RT
and R connected to an external NC (normally closed)
contact such as a fire/smoke detector that will cause
shutdown of the equipment upon activation.
Balanced Climate™ Feature (Standard on All Models)
All units are equipped with the capability of running
in Balanced Climate mode. This mode is designed to
enhance the comfort level by reducing the indoor airflow
amount and extending the run time to help extract more
humidity during cooling operation. The Y1 terminal
is the 24VAC input for Balanced Climate compressor
cooling operation. The Y2 terminal is the 24VAC input
for compressor cooling standard operation. Y1 and Y2
are connected with a brass jumper bar which can be
removed to enable Balanced Climate mode. Units with
an economizer will not have the brass jumper installed.
Refer to vent manuals for instructions on how Balanced
Climate works with each vent.
To operate in Balanced Climate mode, a 2-stage
cooling thermostat is required. The lower indoor airflow
operation is overridden by utilizing a 2-stage thermostat.
If the call for cooling is not satisfied within a given
time frame or temperature differential (specified by
the thermostat), the thermostat will send a signal to
Y2 which then increases the blower speed back to the
selected speed. See pages 24 – 25 for blower speed
selection options.
Refer to page 18 for additional Balanced Climate
requirements and limitations.