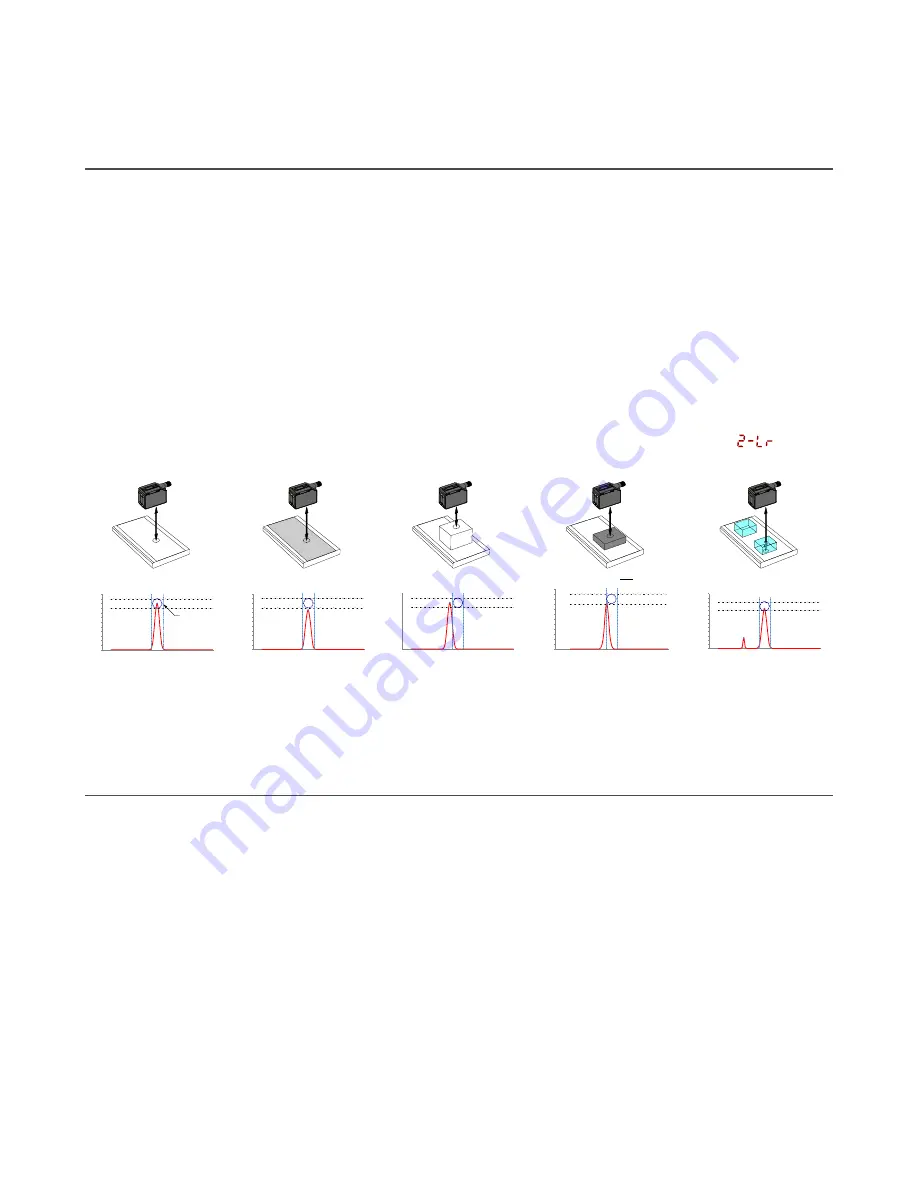
6 Additional Information
6.1 Dual (Int Distance) Mode
In background suppression (DYN, 1-pt, 2-pt) and foreground suppression (FGS) TEACH modes, the Q5X sensor compares
changes in the measured distance between the sensor and target to control the output state. Dual TEACH mode, dual
int distance window, expands the applications the Q5X can solve by combining distance-based detection with light
intensity thresholds. In dual TEACH mode, the user teaches the Q5X a fixed reference surface, and the sensor compares
intensity and distance readings against the reference surface it was taught. After teaching the reference target, the
displayed value is calibrated to 100P, or a 100% match. When an object enters the sensor’s field of view, the degree of
consistency with the reference surface becomes lower and causes a change in sensor output.
In dual mode, you can detect when the target is present at the right distance and when it returns the right amount of light.
This is useful in error-proofing applications where you need to know not only that the part is present (distance), but also that
it is the correct part (intensity).
In dual mode, the Q5X requires a reference surface (far left). Once taught, the distance and intensity of the reference surface
are recorded and used as a baseline. A user-adjustable switching threshold is set, and changes in distance and/or intensity
outside the switching threshold creates a sensor output change. The example uses a 90% (90P) match condition with a
10% change in intensity and/or distance from the reference surface required to change the output state. The default-
switching threshold is a 75% match to the reference condition (75P); this sets the threshold 25% from the distance and
intensity of the reference surface. A transparent object can be detected either by a change in intensity, distance, or by a
double peak reflection (far right). When a double peak reflection is detected, the display alternates between
and the
percent match.
Reference Condition
0
10
20
30
40
50
60
70
80
90
100
110
120
0
25
50
75 100 125 150 175 200 225 250 275 300
10% Switching
Threshold
100% matched di Intensity after Dual teach
In
te
nsi
ty
(%
of
ta
ug
ht
r
ef
er
en
ce
)
Distance (mm)
Change in Intensity
0
10
20
30
40
50
60
70
80
90
100
110
120
0
25
50
75 100 125 150 175 200 225 250 275 300
Output switches with intensity change
In
te
nsi
ty
(%
of
ta
ug
ht
r
ef
er
en
ce
)
Distance (mm)
Change in Distance
0
10
20
30
40
50
60
70
80
90
100
110
120
0
25
50
75 100 125 150 175 200 225 250 275 300
Output switches with distance change
In
te
nsi
ty
(%
of
ta
ug
ht
r
ef
er
en
ce
)
Distance (mm)
Change in Distance and Intensity
0
10
20
30
40
50
60
70
80
90
100
110
120
0
25
50
75 100 125 150 175 200 225 250 275 300
Output switches with intensity and distance change
In
te
nsi
ty
(%
of
ta
ug
ht
r
ef
er
en
ce
)
Distance (mm)
Reduced Intensity and/or Second Peak
0
10
20
30
40
50
60
70
80
90
100
110
120
0
25
50
75 100 125 150 175 200 225 250 275 300
Output switches with intensity and/or second peak (Clear Object Detection)
In
te
nsi
ty
(%
of
ta
ug
ht
r
ef
er
en
ce
)
Distance (mm)
Figure 25. Dual Mode Example
The Q5X sensor can be taught non-ideal reference surfaces, such as surfaces outside of the sensor’s range, very dark
surfaces, or even empty space. These situations may enable applications requiring a long range detection but are subject to
typical diffuse mode detection challenges.
6.2 Dual Mode Reference Surface Considerations
Optimize reliable detection by applying these principals when selecting your reference surface, positioning your sensor
relative to the reference surface, and presenting your target. The robust detection capabilities of the Q5X allows successful
detection even under non-ideal conditions in many cases. Typical reference surfaces are metal machine frames, conveyor
side rails, or mounted plastic targets. Contact Banner Engineering if you require assistance setting up a stable reference
surface in your application.
1. Select a reference surface with these characteristics where possible:
• Matte or diffuse surface finish
• Fixed surface with no vibration
• Dry surface with no build-up of oil, water, or dust
2. Position the reference surface between 200 mm (20 cm) and the maximum sensing range.
3. Position the target to be detected as close to the sensor as possible, and as far away from the reference surface as
possible.
4. Angle the sensing beam relative to the target and relative to the reference surface 10 degrees or more.
Q5X Laser Triangulation Sensor with Background Suppression
34
www.bannerengineering.com - Tel: +1.763.544.3164