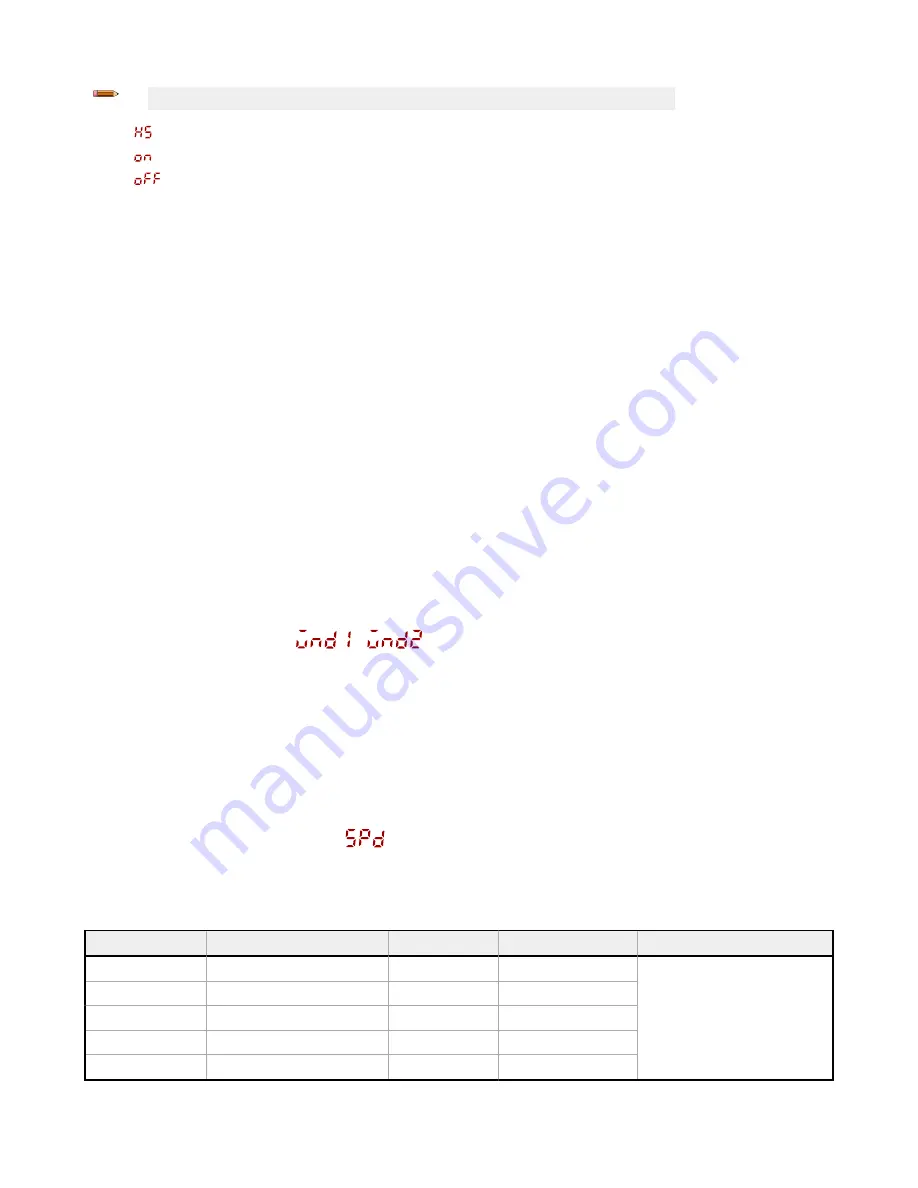
Note: The number that follows trc on the display indicates which channel is selected.
•
—High-Speed Adaptive Tracking On
•
—Adaptive Tracking On
•
—Adaptive Tracking Off (default)
OFF disables the Adaptive Tracking Algorithm—Prevents the sensor from adjusting the thresholds around the taught
reference surface while the sensor is in dual mode. The sensor will not adapt to or learn any target. Environmental changes
may cause the displayed value to deviate from 100P (100%) over time. A periodic re-teach of the reference surface may be
required to restore the displayed value to 100P if this is important to the application.
There are some cases in which disabling adaptive tracking is useful. For example, disable adaptive tracking if the target
passes very slowly through the sensing beam, if the target might stop while partially blocking the beam, and if the
environmental conditions are stable.
ON enables the Adaptive Tracking Algorithm at the standard speed—Recommended for many applications detecting low
contrast targets. Standard adaptive tracking adjusts the thresholds around slowly changing background and environmental
conditions. It adjusts the sensor for stable detection when the environment changes due to gradual dust accumulation,
machine vibration, or ambient temperature changes which influence the signal from the reference surface. Standard
adaptive tracking will not easily adapt to or learn slow moving, low contrast targets (for example, clear targets entering and
exiting the beam over approximately 2 seconds).
HS enables the Adaptive Tracking Algorithm at high speed—Optional adaptive tracking setting used with dual mode. Use
high speed adaptive tracking when the signal from the reference surface changes quickly due to unstable environmental
conditions and high contrast and high-speed targets are being detected. High speed adaptive tracking adjusts the sensor
for stable detection in challenging environmental conditions such as dust accumulation, machine vibration, ambient
temperature changes, or a non-stable reference surface (for example, a running belt or web which influences the signal from
the reference surface). For example, if the signal from the reference surface changes by 10% due to environmental effects,
high speed adaptive tracking adjusts the displayed value back to 100P (100%) over 2 to 3 seconds.
High speed adaptive tracking addresses certain applications where the reference surface is not stable, but the sensor must
detect high speed and high contrast targets reliably. With high speed adaptive tracking there is the potential for the sensor
to adapt the thresholds to slow moving or low contrast targets, leading to missed detection events. If the detection events
are generating small signal changes of similar magnitude to the background changes, detection problems are likely.
Stabilize the reference surface to avoid this problem.
3.2.4 Window Size
Use this menu to manually set a window size for subsequent TEACH operations. This menu is available only if one-point
window (foreground suppression) mode is selected. The default selection is Auto, where the foreground suppression (FGS)
window size is automatically calculated.
This setting is automatically applied during any subsequent teach operation. The window size value represents a ±cm value,
so the total window size is twice this value. For example, a window set of 10 cm gives a 20 cm window centered around the
taught point. The window size can also be changed directly from Run mode after changing the setting to any value except
Auto. For Channel 2, the output must be set to light operate or dark operate.
Values: 0.1 cm to 191 cm
3.2.5 Response Speed
—2000 mm Models
Use this menu to select the response speed.
Default: 25 milliseconds
Table 1: Tradeoffs
Response Speed
Response Speed in Sync Mode
Repeatability
Ambient Light Rejection Excess Gain
3 ms
6 ms
1000 µs
Disabled
See Excess Gain in
Specifications
on
page 30
5 ms
10 ms
1600 µs
Enabled
15 ms
30 ms
3 ms
Enabled
25 ms
50 ms
5 ms
Enabled
50 ms
100 ms
10 ms
Enabled
Q5X Laser Triangulation Sensor with Background Suppression
12
www.bannerengineering.com - Tel: +1.763.544.3164