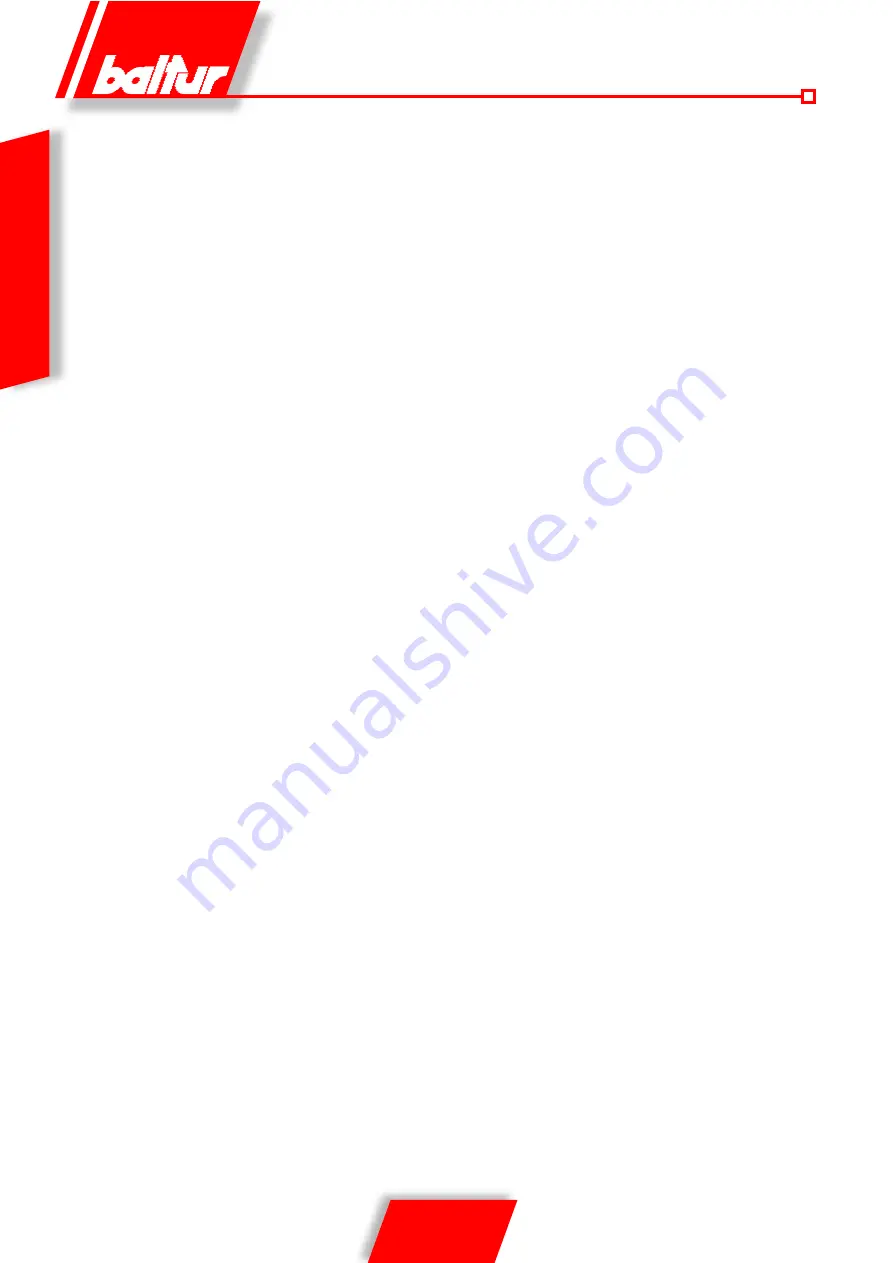
16 / 36
98323_201501
ENGLISH
Burner start-up therefore only begins, provided the
boiler and safety thermostats or pressure switches are
closed, when the resistances have been cut-out and
maximum pre-heater temperature has been reached.
As the burner operates, an appropriate auxiliary relay (part
of the minimum level thermostat) avoids it stopping when the
regulation thermostat commutates the contact to cut-in the
resistances once again (see electric diagram). When the control
box is cut-in the burner ignition stages begin.
The programme involves simultaneous pre-ventilation and pre-
circulation (with hot oil at low pressure) in the entire fuel circuit of
the burner. Burner ignition occurs as described in the previous
chapter (see “Description of operation”), and the burner ignites
at minimum level.
• When the burner is operating on the first flame, the air should be
set (keeping to the specific instructions) for the quantity needed
to ensure good combustion (see BT 8655/1). It is preferable
that air quantity for the first flame be rather low, so that perfect
ignition is guaranteed even under the most difficult conditions.
• After air for the first flame has been set, the burner has to be
stopped by cutting-out current by the main switch, and the
terminals of the second flame thermostat terminal board must
be connected to each other. This connection makes it possible
to cut-in the second flame.
• The main switch must now be cut-in once again causing ignition,
thus automatically proceeding to the second flame, according
to the programme set by the cyclic relay.
• As the burner operates on the second flame, the quantity
of air should now be set (by following the specific
instructions) to ensure good combustion. Combustion
should be controlled by use of the appropriate instruments.
The air regulator must be set to permit a percentage of
carbon dioxide (CO2) in the fumes, varying from a minimum
of 10% to a maximum of 13%. Please remember that
in order to regulate correctly, water temperature in the
plant must be at normal operating level and the burner
must have been operating for at least 15 minutes.
If appropriate instruments are not available, you can judge
by the colour of the flame. Air adjustment is recommended
to achieve a light orange flame colour, avoiding a red
smoky flame, or a white flame due to excessive air.
Check that setting of the pre-heater thermostats do not cause
any inconvenience (poor ignition, smoke, gas formation in
the pre-heater, etc.). If necessary, you may vary these values
upward or downward, but bear in mind that the regulation
thermostat must anyway be set at a temperature about 15
÷ 20° C higher than the minimum level thermostat setting.
The minimum level thermostat must close at he
lowest possible temperature to give a good
atomization (viscosity at the nozzle about 2° E).
See the viscosity-temperature graph relating to the type of oil
used, as a rough guide.
• Disconnect, if already connected, the second flame thermostat
or pressure switch to avoid cutting-in the second flame.
• Check that the setting of the two thermostats (minimum level
and regulation thermostats) is suitable for the type of fuel
intended to be used. If the nominal value of fuel viscosity is
known, the exact value of fuel oil pre-heating temperature can
be verified on the viscosity-temperature graph. Bear in mind
that fuel must reach the nozzle at a viscosity not exceeding
2° E. To avoid snags which would lead to burner stoppage,
the regulation thermostat should be set at a temperature 15 ÷
20° C higher than the minimum level thermostat.
After you have ignited the burner, check that the thermostats
are operating correctly, by reading the appropriate pre-heater
thermometer. Set the resistance control thermostat mounted
on the line filter to about 50 °C.
• Run the auxiliary fuel feed circuit, checking for efficiency and
setting pressure to about 1 bar.
• Remove the plug on the vacuum gauge connection point of the
pump and then slightly open the gate on the fuel supply pipe.
Wait until fuel out of the hole without any air bubbles and then
close the gate.
• Fit a pressure gauge (about 3 bar at the bottom of the scale) at
the connection point of the vacuum gauge on the pump in order
to check the pressure level of the fuel as it enters the burner
pump. Fit a pressure gauge (about 30 bar at the bottom of the
scale) to the pressure gauge connection point on the pump to
check the working pressure of the pump. Fit a pressure gauge
(about 30 bar at the bottom of the scale) to the appropriate
connection point of the first flame return pressure regulator
(see 8713/1) in order to check the first and second flame return
pressure.
• Now open all gates and any other flow stopping valves on the
fuel pipe-line.
• Turn the switch on the control panel into the “O” (OFF) position
to avoid cutting-in resistances when the tank is empty, and cut-
in current to the electric line to which the burner is connected.
Press the relative remote switches manually to check whether
the two motors (fan and pump) turn in the right direction and if
necessary, change over the two main line wires to reverse the
turning direction.
• Run the burner pump, manually pressing the relative remote
switch till the pressure gauge, which shows the pump working
pressure, indicates slight pressure. Low pressure in the circuit
confirms that the pre-heating tank has been filled.
• Cut-in the control panel switch to feed current to the control
box. This way, the resistances heating the fuel in the tank and
the resistance line filter are cut-in by commend of the relevant
thermostat. The heating resistances for the atomizer unit and
the pump are cut-in at the same time. An appropriate pilot-light
on the control panel indicates cutting-in of the resistances.
• The minimum level thermostat closes when fuel contained in the
pre-heater reaches the temperature at which the thermostat is
set. Closure of the minimum level thermostat does not cause
immediate cut-in of the burner control box. This control box cut-
in by the regulation thermostat (contact by commutation) when
the latter cuts-out the resistances because fuel temperature has
reached the level at which the regulation thermostat has been set.
Summary of Contents for BT 75 DSNM-D
Page 2: ......
Page 25: ...23 36 98323_201501 ITALIANO APPARECCHIATURA DI COMANDO E CONTROLLO LAL...
Page 26: ...24 36 98323_201501 ITALIANO...
Page 27: ...25 36 98323_201501 ITALIANO...
Page 28: ...26 36 98323_201501 ITALIANO...
Page 29: ...27 36 98323_201501 ITALIANO...
Page 30: ...28 36 98323_201501 ITALIANO...
Page 31: ...29 36 98323_201501 ITALIANO...
Page 32: ...30 36 98323_201501 ITALIANO...
Page 33: ...31 36 98323_201501 ITALIANO SCHEMA ELETTRICO...
Page 34: ...32 36 98323_201501 ITALIANO...
Page 35: ...33 36 98323_201501 ITALIANO...
Page 36: ...34 36 98323_201501 ITALIANO...
Page 37: ...35 36 98323_201501 ITALIANO...
Page 61: ...23 36 98323_201501 ENGLISH INSTRUCTIONS LAL CONTROL BOX...
Page 62: ...24 36 98323_201501 ENGLISH...
Page 63: ...25 36 98323_201501 ENGLISH...
Page 64: ...26 36 98323_201501 ENGLISH...
Page 65: ...27 36 98323_201501 ENGLISH...
Page 66: ...28 36 98323_201501 ENGLISH...
Page 67: ...29 36 98323_201501 ENGLISH...
Page 68: ...30 36 98323_201501 ENGLISH...
Page 69: ...31 36 98323_201501 ENGLISH WIRING DIAGRAM...
Page 70: ...32 36 98323_201501 ENGLISH...
Page 71: ...33 36 98323_201501 ENGLISH...
Page 72: ...34 36 98323_201501 ENGLISH...
Page 73: ...35 36 98323_201501 ENGLISH...
Page 75: ......