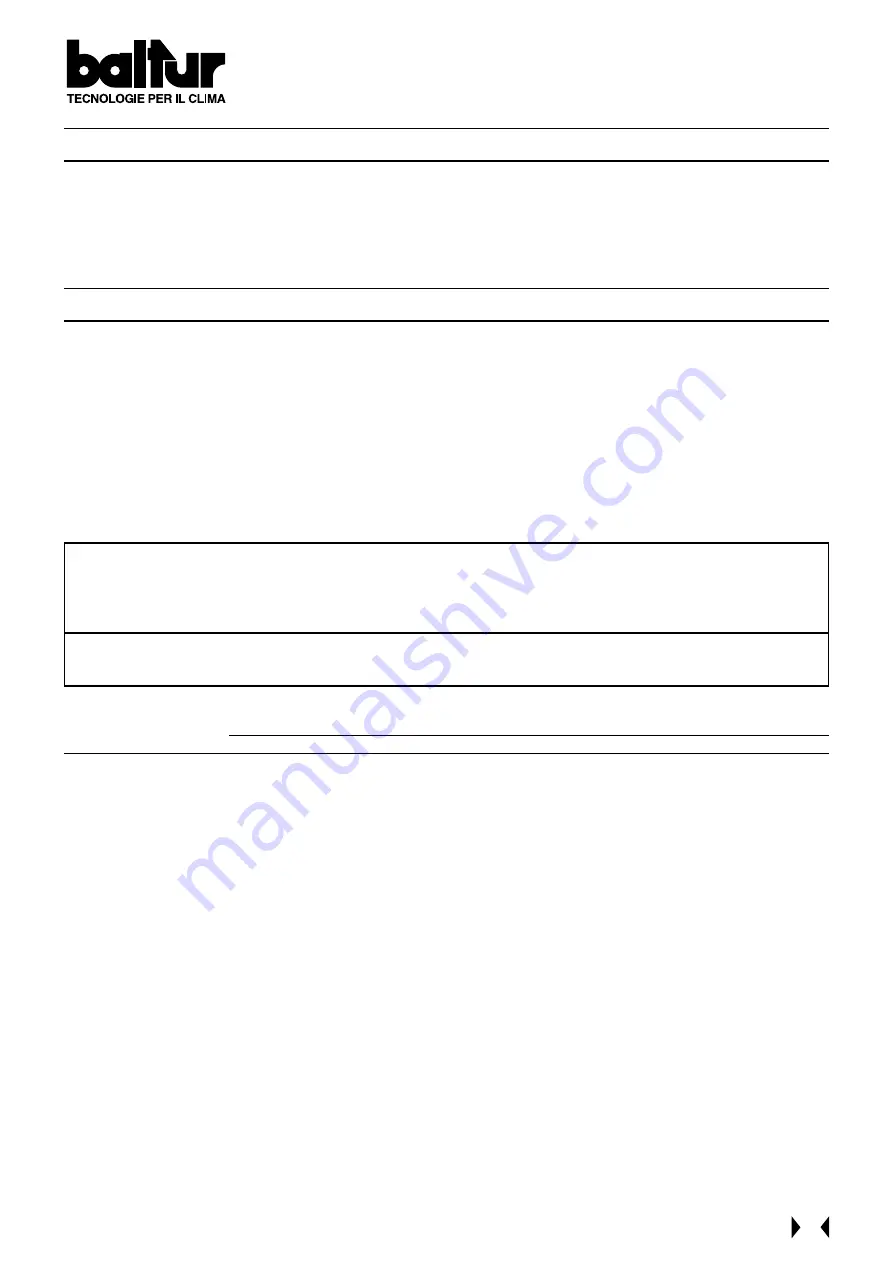
11
ELECTRIC CONNECTIONS
The burner electrical connections have been kept to a minimum. We recommend that all connections are made of
flexible electric wire. Electric lines must be installed at a suitable distance from hot parts.
Make sure that the electric line you wish to connect to the apparatus is fed with voltage and frequency values suitable
for the burner. Make sure that the main line, the relative fuse switch (fuses are essential) and the limiting device, if any,
are suitable for bearing the maximum current absorbed by the burner.
DESCRIPTION OF OPERATION
(see BT 8713/1)
During the fuel oil pre-heating stage, voltage passes through the pre-heater regulation thermostat and reaches the coil
of the resistances remote switch. This remote switch shuts and takes current to the pre-heater resistances, which heat
the fuel contained in the pre-heater. The resistances heating the pump, the unit for atomizing fuel and regulating first-
flame return pressure are also cut-in, through the panel ( I ) switch.
The pre-heater minimum level thermostat shuts off when the temperature reaches the value at which the pre-heater is
set. The equipment is only cut-in when the temperature at which resistances are cut-out (opening of the regulation
thermostat contact) is reached in the pre-heater. This is therefore achieved when fuel oil in the pre-heater is at maximum
temperature. The burner control box (a cyclic relay) is then cut-in by the heating tank regulation thermostat when the
latter cuts-out the resistances by switching off the relative remote switch.
Control box specifications
The control box cyclic relay carries out the ignition programme, by putting into operation the fan motor for executing
the preventilation stage. If the pressure of the air supplied by the fan is sufficient to put the relative pressure switch
into action, cutting in also occurs of the motor of the pump that carries out hot oil pre-circulation in the burner pipes.
Oil from the pump reaches the pre-heater, passes through it, reaching the temperature envisaged, exits through a
filter and then reaches the atomizing unit. The oil circulates in the atomizing unit without flowing out of the nozzle
because the channels leading towards the nozzle (outward flow) and from the nozzle (return flow) are closed. Closure
is carried out by “closing cones” fixed to the rod ends. These “cones” are pressed against their seats by strong
springs located at the opposite end of the rods. Oil circulates and flows out of the return end of the atomizing unit,
passes through the trap where the TRU thermostat is and reaches the 1st flame return pressure regulator, passes
through it, goes through the 2nd flame solenoid valve (usually open), reaches the pump return pipe and from this it
discharges into the feed system return pipe. Hot oil circulation as described above is carried out at slightly higher
pressure (a few bar) compered to the minimum pressure at which the 1st flame return pressure regulator is set (10 ÷
12 bar). This oil precirculation and preventilation phase lasts 22,5 seconds. This time can be prolonged (infinitely, in
theory) because the electric circuit is built in such a way that it does not enable the control box to continue carrying out
the ignition programme, until the fuel temperature, in the nozzle return piping, has reached the level at which the TRU
thermostat is set. This particular design does not allow fuel to pass through the nozzle until the fuel itself reaches at
least the temperature at which the TRU thermostat is set. Usually, the TRU thermostat operates within normal
preventilation time (22,5 seconds), otherwise the fuel oil preventilation and pre-circulation stages are prolonged until
the TRU goes into action. TRU operation (oil circulating is sufficiently hot) enables the control box to continue executing
the ignition programme, by cutting-in the ignition transformer which feeds high voltage to the electrodes.
High tension between the electrodes triggers the electric charge (spark) to ignite the air-fuel mixture.
2,5 seconds after the ignition spark begins, the control box takes voltage to the magnet which, through suitable
levers, moves back the two rods that intercept the flow of fuel (outgoing and return) to the nozzle. The moving back of
the rods also closes the by-pass inside the atomizing unit, and consequently pump pressure reaches the normal level
of about 20 ÷ 22 bar. Withdrawal of the two rods from the closure seats now enables fuel to enter the nozzle at a
pressure of 20 ÷ 22 bar set at the pump and to exit the nozzle, sufficiently atomized.
Return pressure, which determines oil flow to the combustion chamber, is now regulated by the 1st flame return
pressure regulator.
Control box
& relative
Programmer
LAL 1.25
Cyclic relay
Safety Time
in seconds
5
Pre-Ventilation & Oil
Pre-circulation Time
in seconds
22,5
Pre-ignition Time
in seconds
2,5
Post-ignition
Time
in seconds
5
Time between
1st and 2nd
flames
in seconds
20
Summary of Contents for BT 75 DSNM-D
Page 7: ...7 WORKING FIELD N 0002921710 N 0002921701 WORKING FIELD...
Page 23: ...23 INSTRUCTIONS LAL CONTROL BOX N 7153 Rev 04 1996...
Page 24: ...24 INSTRUCTIONS LAL CONTROL BOX N 7153 Rev 04 1996...
Page 25: ...25 INSTRUCTIONS LAL CONTROL BOX N 7153 Rev 04 1996...
Page 26: ...26 INSTRUCTIONS LAL CONTROL BOX N 7153 Rev 04 1996...
Page 27: ...27 INSTRUCTIONS LAL CONTROL BOX N 7153 Rev 04 1996...
Page 28: ...28 INSTRUCTIONS LAL CONTROL BOX N 7153 Rev 04 1996...
Page 29: ...29 N 7153 Rev 04 1996 INSTRUCTIONS LAL CONTROL BOX...
Page 30: ...30 N 7153 Rev 04 1996 INSTRUCTIONS LAL CONTROL BOX...
Page 32: ......
Page 33: ......
Page 34: ......
Page 35: ......
Page 36: ......
Page 37: ......
Page 38: ......
Page 39: ......