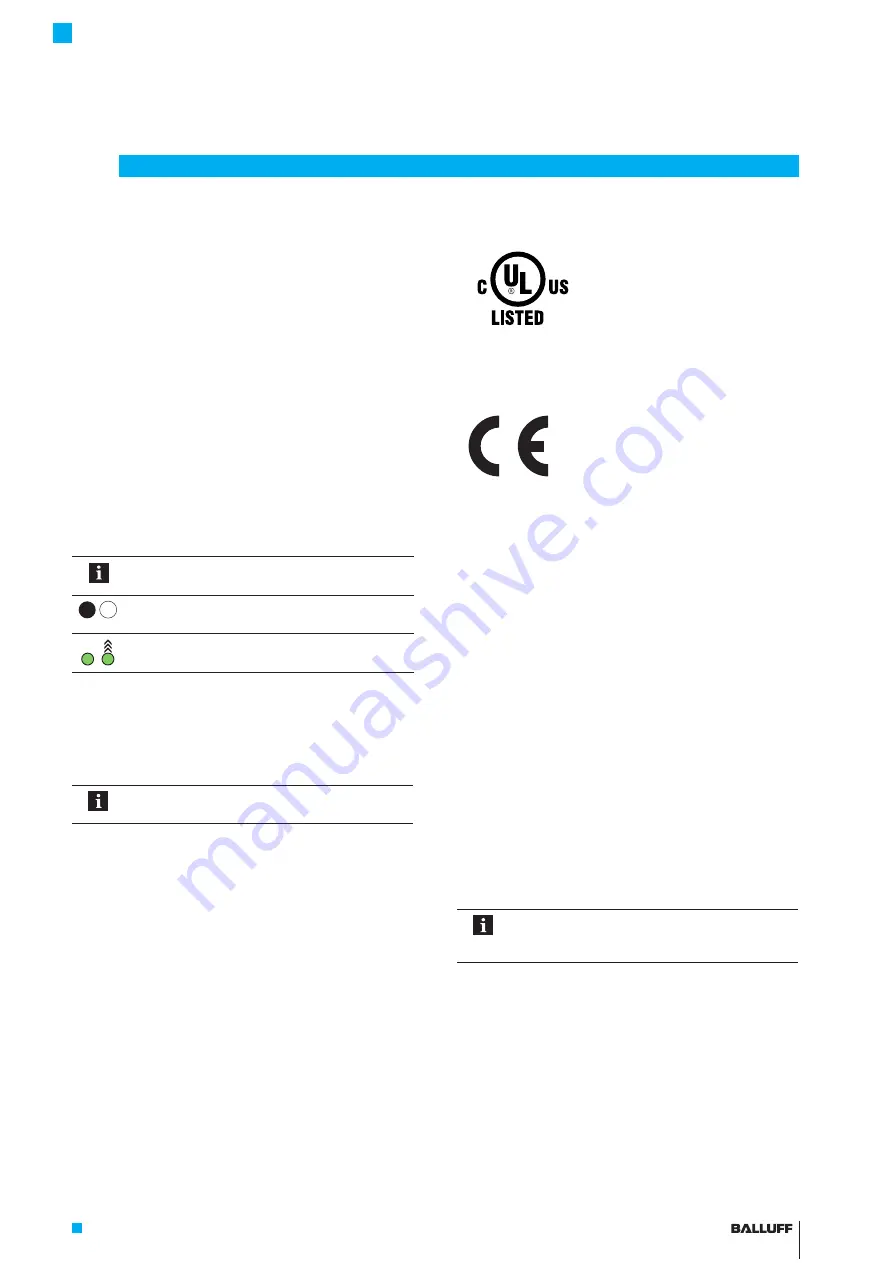
www.balluff.com
5
english
1.1
Validity
This guide describes the construction, function and setup
options for the BTL6 Micropulse Transducer with analog
interface. It applies to types
BTL6-A/C/E/G500-M _ _ _ _ -PF-S115
(see Ordering
code on page 20).
The guide is intended for qualified technical personnel.
Read this guide before installing and operating the trans
ducer.
1.2
Symbols and conventions
Individual
handling instructions
are indicated by a
preceding triangle.
►
Action instruction 1
Action sequences
are numbered consecutively:
1.
Action instruction 1
2.
Action instruction 2
Note, tip
This symbol indicates general notes.
a
b
These symbols indicate the programming
inputs.
Symbols of this type indicate the LED display.
1.3
Scope of delivery
– BTL6 transducer
– Mounting clamps with insulating sleeves and screws
– Condensed guide
The magnets are available in various models
and must be ordered separately.
1.4
Approvals and markings
UL approval
File no.
E227256
US Patent 5 923 164
The US patent was awarded in connection with this
product.
The CE Mark verifies that our products
meet the requirements of the current
EMC Directive.
The transducer meets the requirements of the following
product standard:
– EN 6132623 (noise immunity and emission)
Emission tests:
– RF emission
EN 55011
Noise immunity tests:
– Static electricity (ESD)
EN 6100042
Severity level 3
– Electromagnetic fields (RFI)
EN 6100043
Severity level 3
– Electrical fast transients (burst)
EN 6100044
Severity level 3
– Surge
EN 6100045
Severity level 2
– Conducted interference induced
by highfrequency fields
EN 6100046
Severity level 3
– Magnetic fields
EN 6100048
Severity level 4
More detailed information on the guidelines,
approvals, and standards is included in the
declaration of conformity.
1
Notes to the user
BTL6-A/C/E/G500-M _ _ _ _ -PF-S115
Micropulse Transducer in a Flat Profile Housing