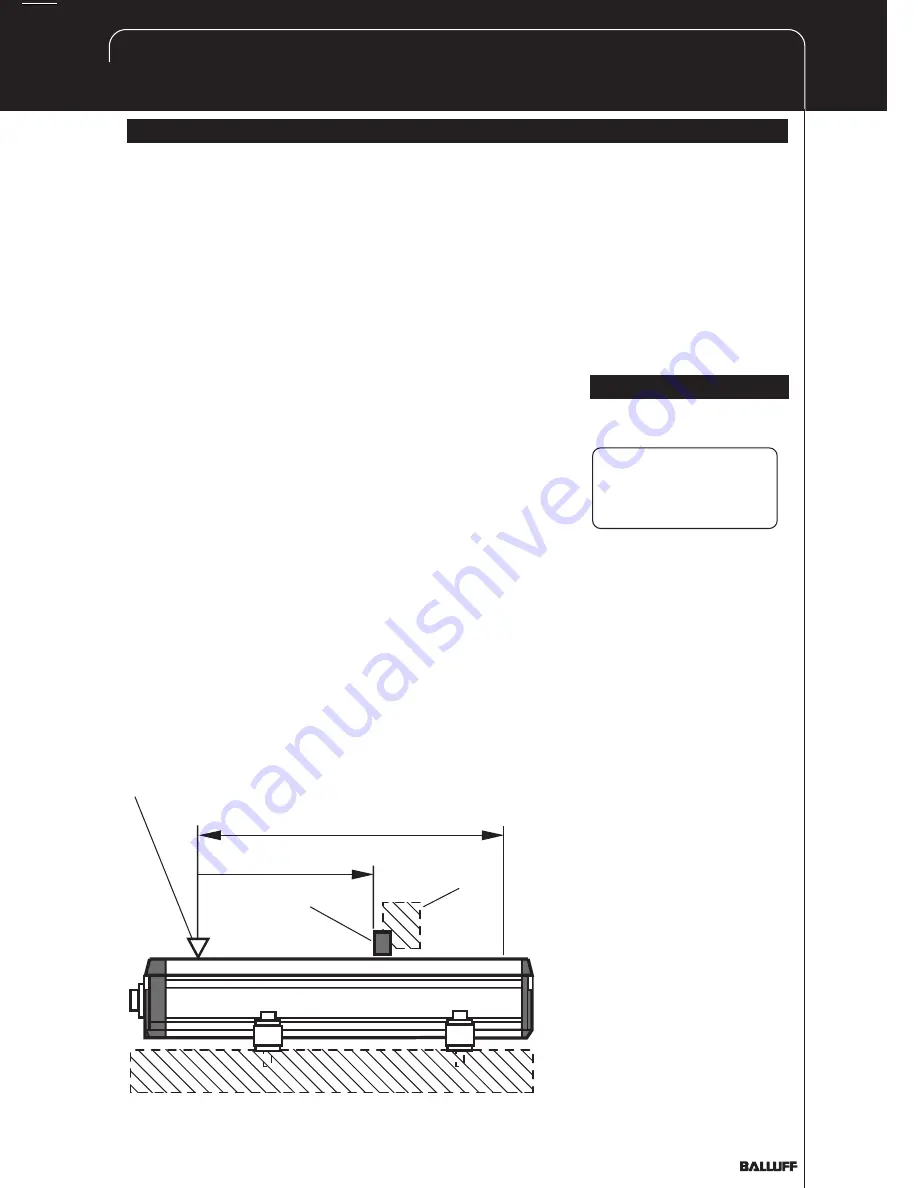
WWW.BALLUFF.COM
•
1-800-543-8390
BTL5-P/I/K/L/M_-
M/U_ _ _ _-P-S32/KA_ _
Micropulse Linear Transducer
Digital Output / Profile Housing
2 Function and Characteristics
2.1 Characteristics
Micropulse transducers feature:
—
Very high resolution,
repeatability and linearity
—
Bus-compatible interface
(BTL5-I...)
—
Immunity to shock, vibration,
contamination and electrical
noise
—
An absolute output signal
—
BTL to processor cable
lengths up to 500 m
—
IP 67 per IEC 529
2.2 Function
The Micropulse transducer
contains a tubular waveguide
enclosed by an extruded
aluminum housing. A magnet
attached to the moving member
of the machine is moved across
the top of the housing and its
position constantly updated.
The magnet defines the
measured position on the
waveguide. An externally
generated INIT pulse interacts
with the magnetic field of the
magnet to generate a magneto-
strictive torsional wave in the
waveguide which propagates at
ultrasonic speed.
The torsional wave arriving at the
end of the waveguide is absorbed
in the damping zone. The wave
arriving at the beginning of the
waveguide creates an electrical
signal in the coil surrounding the
waveguide. The propagation time
of the wave is used to determine
the position, which is presented
on the output in various digital
formats. This takes place with
high precision and repeatability
within the measuring range
indicated as the nominal
stroke length.
On both ends of the nominal
stroke length is an area which
provides an unreliable signal, but
which may be entered.
The electrical connection between
the transducer, the processor/
controller and the power supply is
via a cable, which depending on
the version is either fixed or
connected using a female
connector.
Dimensions for installing the
Micropulse transducer and for the
magnets and control arm are
found on pages 4 and 5.
2.3 Available stroke length
To provide for optimum fit in any
application, a wide range of
standard stroke lengths and
magnets in various form factors
are available. Magnets and control
arms must therefore be ordered
separately.
See inside front cover for
available stroke lengths.
3.1 Transducer installation
Ensure that no strong
electrical or magnetic fields
are present in the
immediate vicinity of the
transducer.
Any orientation is permitted.
The mounting brackets and
cylinder head screws allow the
transducer to be mounted on a
flat machine surface. These
should be evenly spaced (Figs.
3-1 and 3-5). The recom-
mended spacing for long
transducers and extreme
conditions (e.g. strong shock or
vibration):
A = 80 mm; spacing between
the individual brackets
B = 250 mm.
The isolation bushings are used
to electrically insulate the
transducer from the machine
(Fig. 3-1and 3-5 and chapter 5.6
Noise elimination).
The Micropulse transducer in
profile housing is suitable both
for floating, i.e. non-contacting
magnets (Page 4) and for
captive magnets (Page 5).
3 Installation
Notch on housing to mark the beginning of the stroke range
Current position of magnet
Micropulse Transducer
Nominal stroke =
Measuring range
Fig. 2-1: Basic arrangement
El. connection
Damping zone
Moving machine
part
and magnets
Summary of Contents for BTL5-P
Page 2: ......