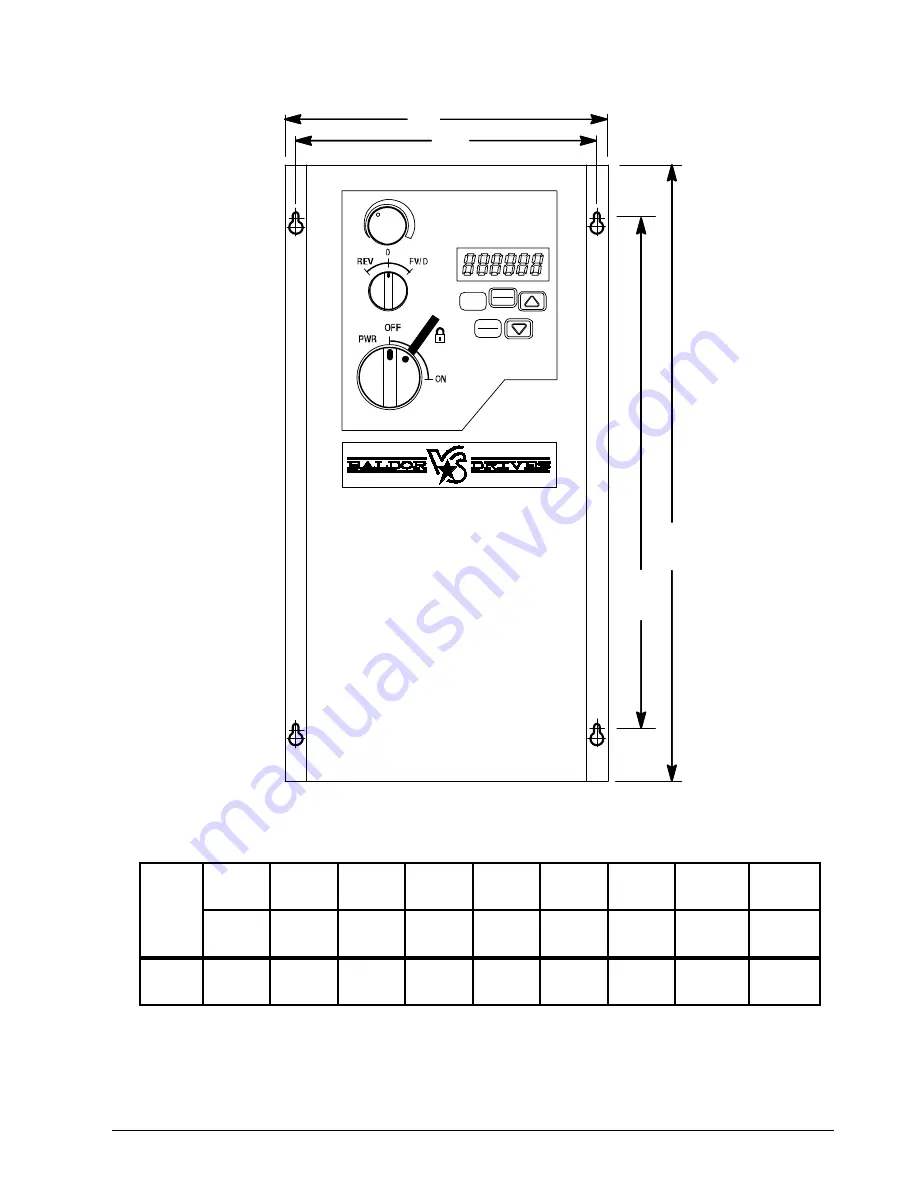
Installing the Drive 3-3
MN762S
Figure 3-2 NEMA 12 / IP55 Mounting Hole Locations
A1
A
B 1
B
STOP
RESET
START
PROG
ENT
Table 3-2 NEMA 12 / IP55 Dimensions
Frame
A
A1
A2
B
B1
I
Φ
J
Φ
C
(Depth)
Weight
in
(mm)
in
(mm)
in
(mm)
in
(mm)
in
(mm)
in
(mm)
in
(mm)
in
(mm)
lb
(kg)
B
12.20
(310)
12.20
(310)
1.30
(33)
6.46
(164)
6.02
(153)
0.17
(4.2)
0.33
(8.4)
7.09
(180)
9.92
(4.5)
Control Terminal Torque Settings of 4.5 lb-in (0.5 Nm)
Power Terminal Torque Settings of 9 lb-in (1 Nm)
Summary of Contents for VS1MXS series
Page 1: ...03 11 Installation Operating Manual MN762S VS1MXS AC Extreme Duty Microdrive...
Page 28: ...5 10 Control Wiring MN762S...
Page 58: ...7 24 Parameter Descriptions MN762S...
Page 60: ...8 2 Customizing Your Application MN762S...
Page 80: ...D 2 Options and Kits MN762S...
Page 85: ......
Page 86: ......