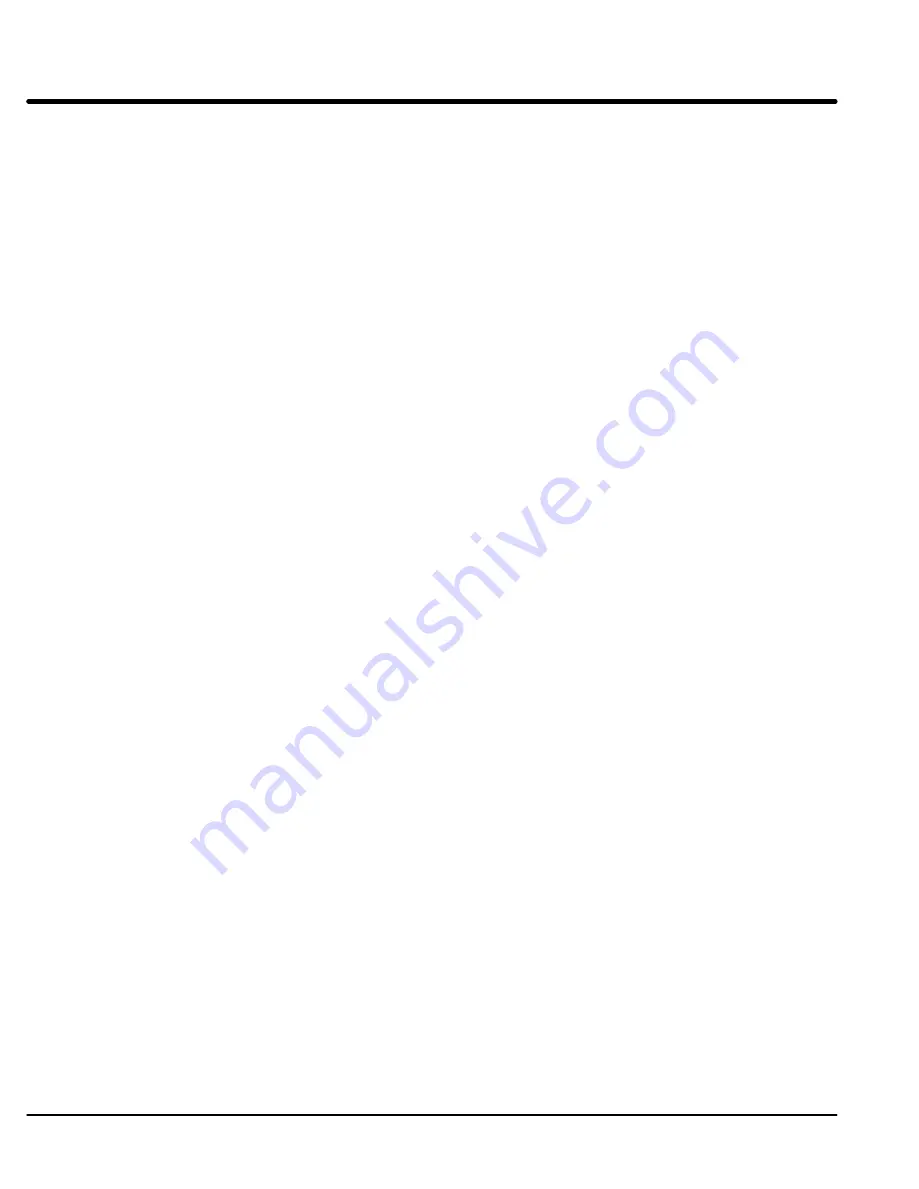
3-8 Maintenance & Troubleshooting
MN605
Field Coil Overheating
The blowers or external cooling systems should be left in operation if the main field
windings remain fully energized with the motor at standstill. Failure to do so may cause too much heat
build-up which could cause reduced insulation life.
When using field economy circuits to reduce voltage to the main fields during standstill, blowers do not
need to be operating. The most common failure with overheated field coils is a short in one or more of the
shunt coils.
Shorted coils show less than half the line voltage for two pole motors. This is with the fields connected for
high voltage (in series). Shorted four pole motor coils will read less than 1/4 of the line voltage with the
coils connected for high voltage (in series).
A grounded coil may cause overheating. This defect may be tested as shown by the ground test for an
armature. With brushes lifted, measure the motor winding resistance. If the armature is grounded, less
than 1 meg ohm is measured.
An open field coil on a motor will cause the armature to have no torque. The motor may run at a very high
speed at no load. The commutator may be flashing. To locate an open coil, apply line voltage to the shunt
coils (brushes lifted). A voltmeter will show no reading across a good coil. It will show about the line
voltage across the open coil.
These tests should be done by experienced and qualified personnel. If you find any of the above defects,
don’t run the motor. First contact your local Baldor District Office or an Authorized Baldor Service Center
for repairs.
Excessive Load
Excessive load may be found by checking the DC armature ampere input and comparing it with the
rating on the nameplate. An excessive load may prevent the motor from starting or accelerating to full
load speed. It could finally result in premature failure of the motor or control. Be sure to use an averaging
type ammeter if the motor’s power is coming from a rectifier or SCR control.
Jogging and Repeated Starts
Repeated starts or jogs of motors may reduce the life of the brushes and winding insulation. The heat
produced by excessive starting may be more than what can be dissipated by the motor under a constant
full load conditions. If you must frequently start or jog a motor, you should check the application with the
local Baldor District Office.
Heating
Duty cycle and maximum ambient temperature are shown on the nameplate of the motor. If there is any
question about safe operation, contact the local Baldor District Office.
Motor overheating may be caused by improper ventilation, excessive ambient temperature, dirty
conditions or an inoperable blower or dirty filter. Electrical causes may be due to excess current caused
by an overload or over-voltage to the fields.
Thermostat
Most stock Baldor DC motors 180 frame and above have a standard temperature-sensing thermostat
mounted to their interpole winding. This normally closed thermostat opens when the temperature limit is
exceeded. Another option available is a normally open thermostat that closes with temperature.
On blower cooled or separately ventilated motors, the protection capabilities of the thermostats are
greatly reduced at low speeds. This is because the interpoles have the same amount of heat transfer
regardless of speed. Armature heat transfer is less at low speed. There is less internal air turbulence at
low speeds causing higher temperatures at the armature.
The thermal time constant for interpoles can be as much as five times longer than the armature’s time
constant. Because of this, the thermostat cannot be relied upon to protect the armature during extreme
overloads lasting a short time.
The ripple of the rectified power supply and manufacturing tolerances of mounting the device affect the
thermostat’s accuracy.
For thermostat contact ratings, refer to Thermostats in Section 2 of this manual.
Artisan Technology Group - Quality Instrumentation ... Guaranteed | (888) 88-SOURCE | www.artisantg.com