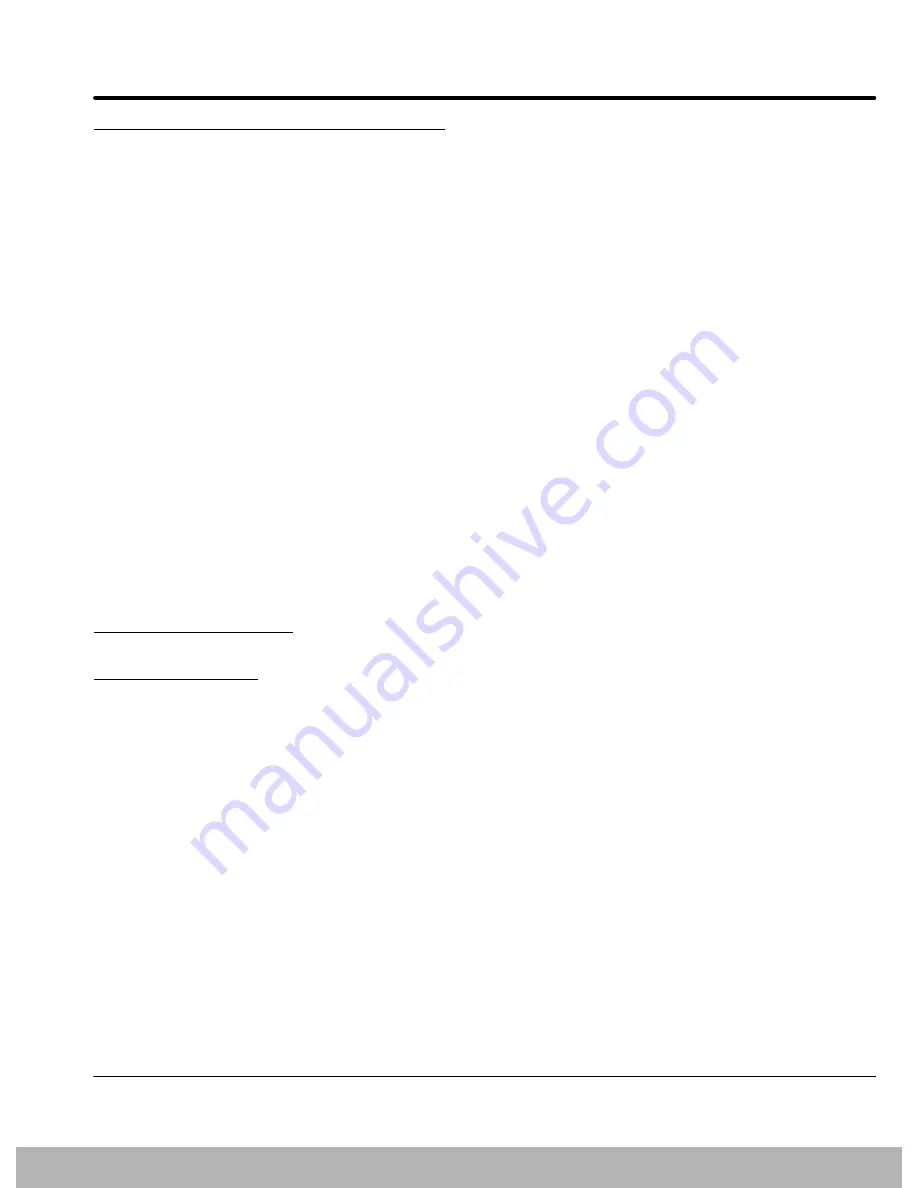
Maintenance & Troubleshooting 3-7
MN409
Sleeve/Anti
−
Friction Bearing Bracket Removal
1.
For anti
−
friction bearing motors the inner cap bolts must be removed before removing the end
shield.
2.
For sleeve bearing motors the bearing cartridge must be removed before disassembly of the
end shield. (See G5000, G315, G5810 and G40 Sleeve Bearing & Cartridge Removal).
3.
Remove all bolts that secure the end shield to the frame.
4.
Using a hoist, support the bracket.
5.
To remove the G50 bracket from rabbet fit, jacking holes have been provided next to the four
bracket bolts located at 45
°
. Tighten jack bolts evenly to avoid axial misalignment of the end
shield. To remove the G5000, G315, G5810 and G40 brackets from the rabbet fit, pry bar slots
have been provided on the lugs.
Anti
−
Friction Bearing Removal/Replacement
1.
Remove the end shield (see Sleeve/Anti
−
Friction Bearing Bracket Removal).
2.
The bearing can now be removed by using a conventional bearing puller with the puller arms
located behind the bearing race. Protect the shaft center by using a spacer block of bass or
some other soft material between the shaft and bearing puller.
3.
Clean and inspect all parts. Remove all old grease.
4.
All shaft bearing shoulders and journals should be free of nicks before replacing bearing.
Dress shaft with emery cloth or stone as necessary.
5.
Heat bearing to 250
°
F (120
°
C) for at least 30 minutes.
6.
Place bearing onto shaft. Make certain that the bearing is contacting the locating shoulder on
shaft. Do not use impact force on bearing.
7.
Let the bearing cool. Grease the outboard side cavity of the bearing 100%. Grease inner caps
and bracket bearing housing to 60% full.
8.
Assemble end shield in reverse order. (See Sleeve/Anti
−
Friction Bearing Bracket Removal).
Rotor And Stator Removal
Consult your local Baldor District office for proper removal procedures.
Winding Maintenance
WARNING:
Solvents can be toxic and/or flammable. Follow manufacturer’s safety procedures and
directions. Failure to observe this precaution could result in bodily injury.
Caution:
Do not use solvents containing trichloroethane to clean interior or exterior of motor. Damage
may occur to paint and insulation systems.
Disconnect and lockout the power source. Ensure no power is applied to the motor. To inspect the ends
and outside surface of the windings, remove the brackets from the motor. Inspection of these portions of
the windings will provide a good indication of their general condition. To thoroughly inspect and clean the
windings it may be necessary to remove the rotor.
There are numerous methods for cleanings windings. The following methods are most commonly used,
in order of preference.
Note: Before cleaning the windings check for loose blockings, evidence of damage to insulation,
distortion or movement of coils, etc. If any of these conditions exist, contact your local Baldor
District office for recommendations.
Dry Wiping
This method is satisfactory when the surfaces to be cleaned are accessible and when only dry dirt is to
be removed. Use a clean dry, lint free cloth. The lint will adhere to the insulation and increase dirt
collection. Lint is particularly objectionable on high voltage insulation systems as it tends to concentrate
corona discharge.
This Manual:http://www.manuallib.com/baldor/mn409-large-ac-motors-handbook.html