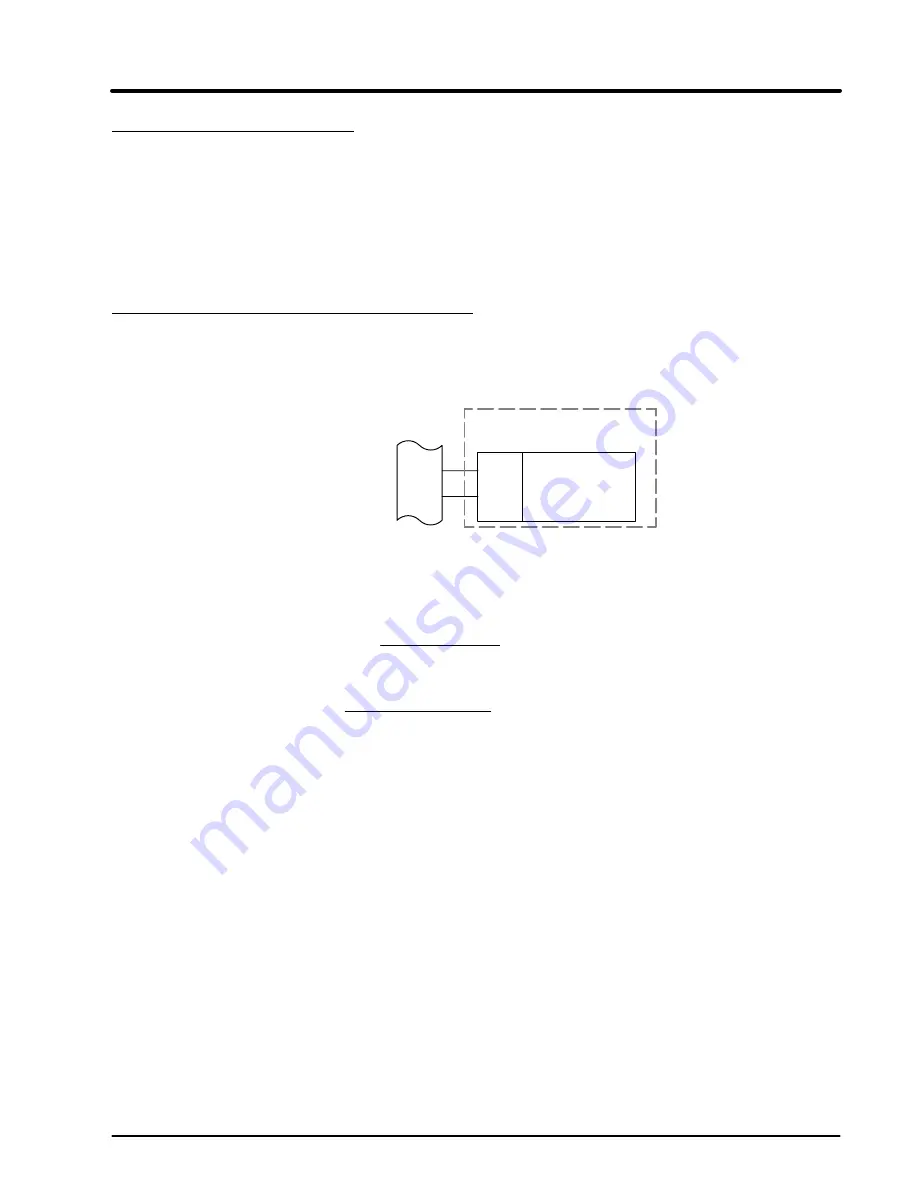
MN715P
Receiving and Installation
3-8
Motor Brake Connections
For motors with spring set brakes, connect the brake power leads and the
motor power leads separately. Because the inverter has variable voltage
output to the motor, the inverter may not supply enough power at low
frequencies for proper brake operation. If using a motor with an internally
connected brake, the brake power leads must be connected to a separate
power source for proper brake operation. Refer to Figure 3-2 for terminal
locations.
Optional Dynamic Brake Hardware
Dynamic Brake (DB) Hardware must be installed on a flat, non-flammable,
vertical surface to obtain effective cooling and operation. The ambient
temperature must not exceed 80
°
C. DB connections are shown in Figure 3-6.
Figure 3-6 Wiring for RGA Assembly
See recommended Terminal
Tightening Torques in Section 6.
R1
Optional
Dynamic Brake
Resistor
J5
Power Terminal Strip
DB
Terminals
R1
R2
R2
Note: Although not shown, metal conduit should be used to shield all power wires
and motor leads.
General Machinery Load Calculations:
1.
Calculate braking duty cycle:
Duty Cycle
+
Braking Time
Total Cycle Time
2.
Calculate deceleration torque:
T
Decel
+
RPM change
Wk
2
308
time
*
Friction
(Lb.Ft.)
where:
T
Decel
= Deceleration torque in lb-ft.
Wk
2
= Inertia in lb-ft
2
time = In seconds
3.
Calculate watts to be dissipated in dynamic braking resistor:
Watts
+
T
Decel
ǒ
S
max
*
S
min
Ǔ
Duty Cycle
(0.0712)
where: S
max
= Speed to start braking
S
min
= Speed after braking
4.
Multiply watts calculated in step 3 by 1.25 to allow for unanticipated
loads (safety factor).