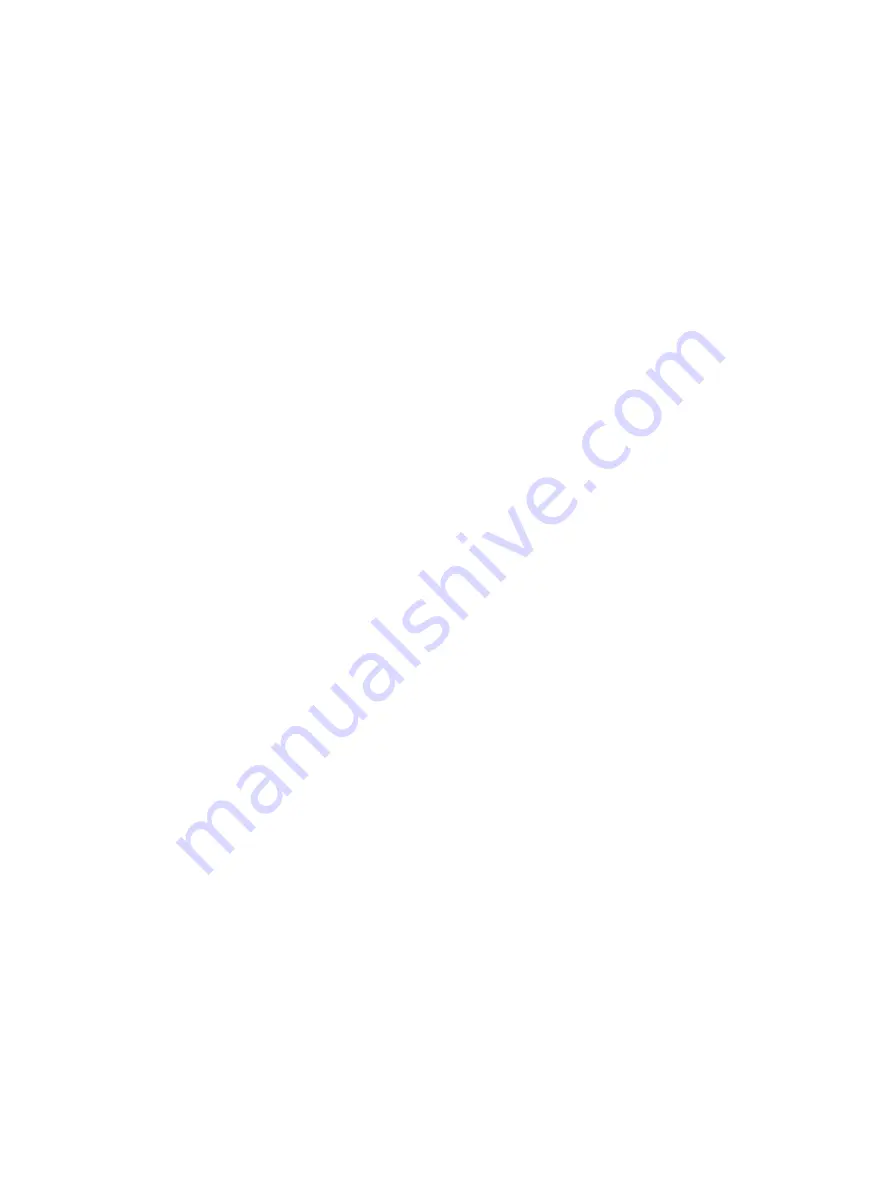
66 | Baker Hughes.
© 2021 Baker Hughes Company. All rights reserved.
2. Use + and – buttons to change the value.
3. Press * to return to menu and move to next item. SIG LO must be between 3.8 and
14.0 mA.
4.
SIG HI
displays the input signal that corresponds to the full open, ATO, or full closed,
ATC position.
5. If the displayed value is:
• Correct, press + to advance to the next item.
• Not correct
,
press * to display value of
SIG HI
.
6. Use + and – buttons to change the value.
7. Press * to return to menu and move to next item.
SIG HI
must be between 8.0 and 20.2
mA. SIG HI must be larger than SIG LO by at least 5 mA.
Calibration of the positioner is now complete.
4.3.12 FAILSAFE Mode
FAILSAFE mode cannot be selected from any of the previous menus. FAILSAFE mode
and display are initiated by detection of a critical fault in the positioner or the valve system.
There are two ways to deal with a FAILSAFE condition: correct the problem and clear the
error messages
or
run through the FAILSAFE menu, view error messages, enter MANUAL
mode and RESET
.
RESET
restarts operation.
When failsafe occurs:
1. Press + to move to
VIEW ERR
.
2. Press * to view the first error message. Press + to scroll through all fault messages.
3. Correct the cause of the problem [Refer “Device Status Diagnostics” on page 76] and
press + to move to
CLR ERR
.
4. Press * to remove all error messages from memory
.
5. Move to the
MANUAL
menu. If you have cleared the errors
RESET
no longer appears.
or
1. Press + to move to
VIEW ERR
.
2. Press * to view the first error message. Press + to scroll through all the fault messages
in turn.
3. Move to
MANUAL
menu and enter Manual mode
.
4. Select RESET to start the valve from its failsafe condition.
NOTE : SIG HI and SIG LO allow adjustment of the input current range that
corresponds to full valve travel. Normally they are set to 4 and 20 mA.
Adjustment is normally required only for split range applications and provides
flexibility for unusual applications. A separate ValVue calibration procedure
enables adjustment of the current sensing circuit to a precision current
reference standard.