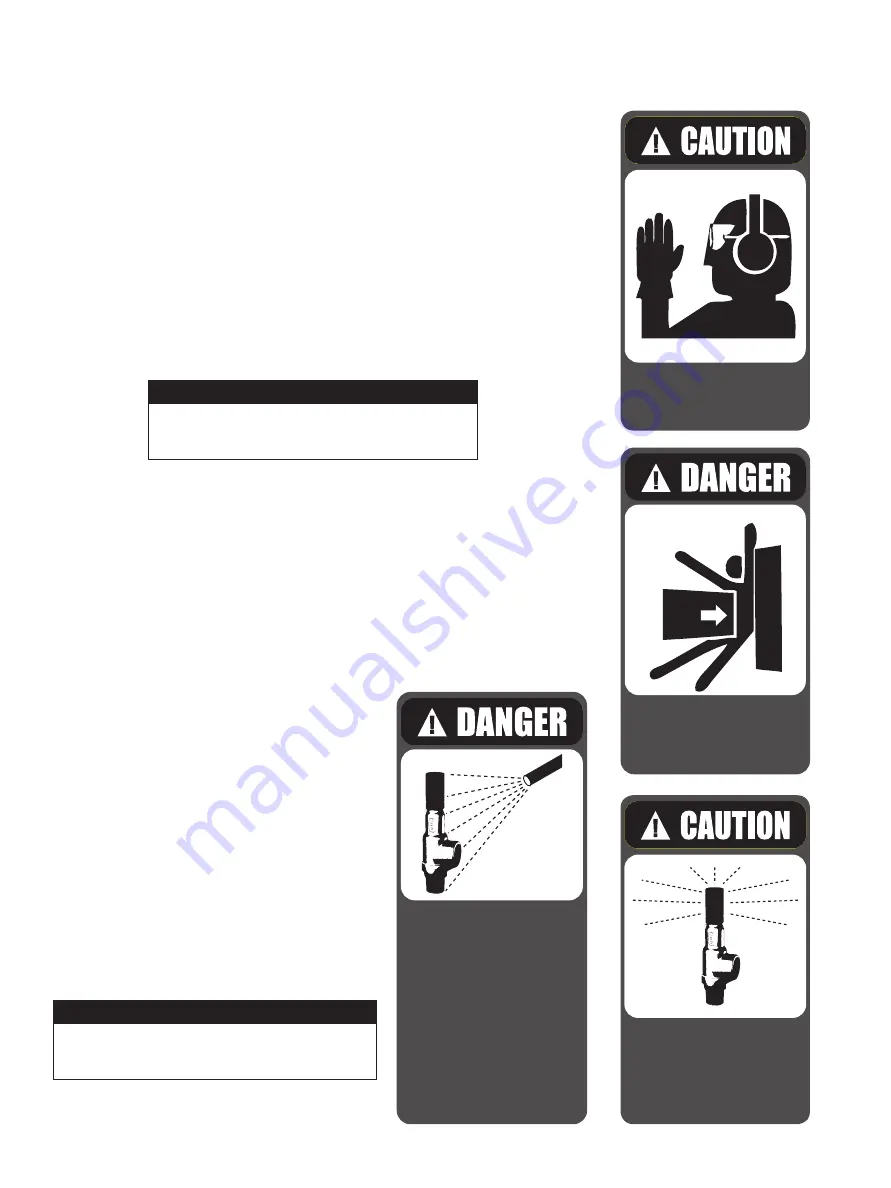
18 |
Baker Hughes
© 2020 Baker Hughes Company. All rights reserved.
XI. Recommended Installation Practices (Contd.)
XII. Disassembly of 19000 Series SRV
A. General Information
Consolidated SRVs can be easily disassembled for inspection, the reconditioning of
seats or the replacement of internal parts. Appropriate set pressure can be established
after reassembly. (See Figures 1 through 6 for parts nomenclature.)
Notes:
• Before starting to disassemble the valve,
be sure there is no material pressure in the
vessel.
• Many pressure vessels that are protected
by Consolidated safety relief valves contain
dangerous materials.
• Decontaminate and clean the valve inlet and
outlet and all external surfaces in accordance
with the cleaning and decontaminating
recommendations in the appropriate Material
Safety Data Sheet.
• Parts from one valve should not be
interchanged with parts from another valve.
Wear necessary
protective equipment to
prevent possible injury
Valve caps and bonnets
cantrapfluids.Use
caution when removing
to prevent injury or
environmental damage.
Before disassembling
the valve, ensure there is
no media pressure in the
vessel.
Many pressure vessels
protected by Consolidated
safety relief valves contain
dangerous materials.
Decontaminate and
clean the valve inlet,
outlet, and all external
surfaces in accordance
with the cleaning
and decontaminating
recommendations in the
appropriate Material Safety
Data Sheet.
ATTENTION!
!
Do not interchange parts from one valve with
parts from another valve.
the opening of one (or more) valve(s) may cause a superimposed backpressure in
the remaining valves. Under these conditions, the use of the 19096-DA-BP model is
recommended.
In every case, the nominal discharge pipe size should be at least as large as the nominal
size of the SRV outlet flange. In the case of long discharge piping, the nominal discharge
pipe size must sometimes be much larger.
As a final point, the discharge piping size is never less than the size of the valve outlet,
nor heavier than schedule 40 pipe size. In addition, the discharge piping must be
designed to limit the total backpressure to a maximum of 10 percent of the valve set
pressure, or 400 psig (27.58 barg), whichever is smaller.
ATTENTION!
!
Undersized discharge piping could create
built-up backpressure.
Summary of Contents for Consolidated 19000 DA
Page 2: ......