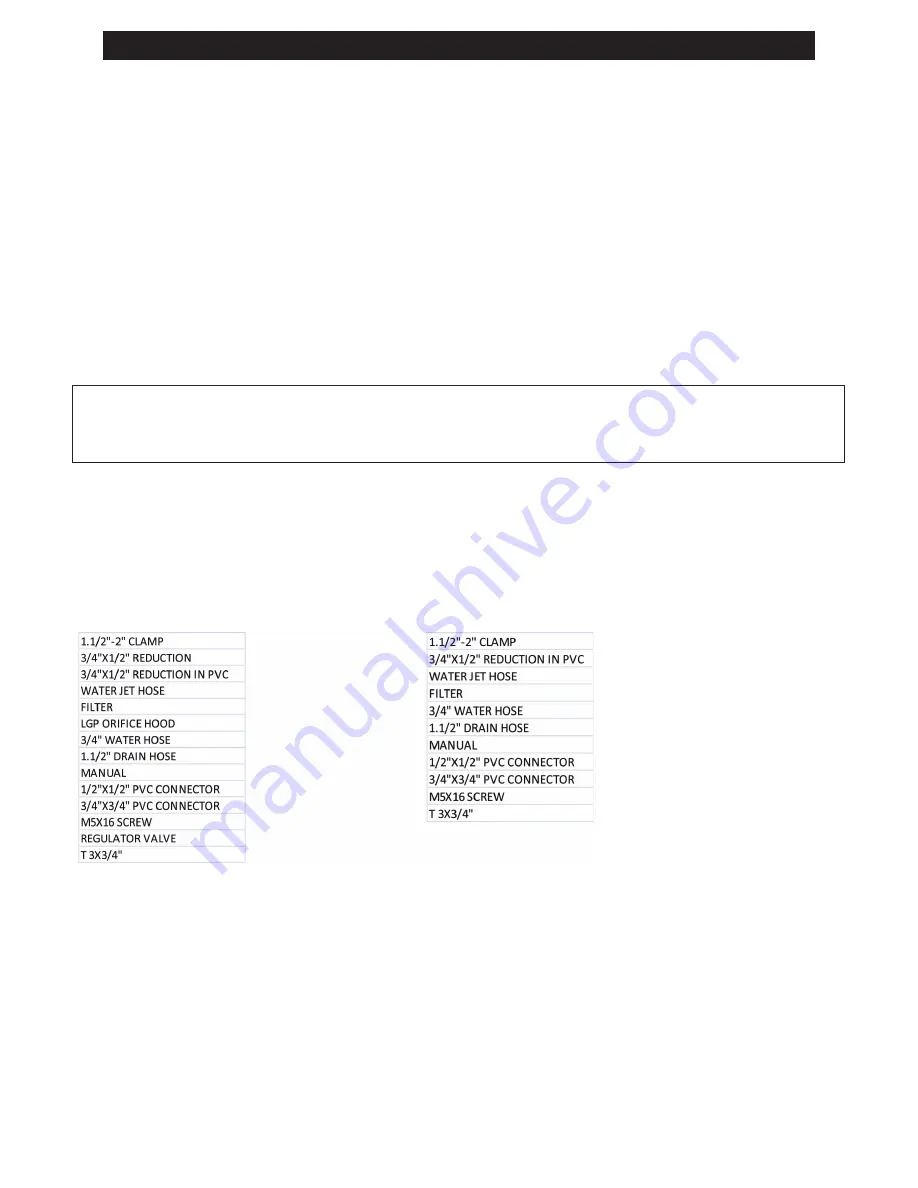
UNPACKING
1. Remove all packaging and transit protection including all protective plastic coating from the exterior stainless steel panels.
2. Check the oven and supplied parts for damage. Report any damage immediately to the carrier and distributor.
3. Check that the following parts have been supplied with your oven:-
4. Report any de ciencies to the distributor who supplied your oven.
5. Check that the available electrical supply is correct to that shown on the Technical Data Plate located on the front right hand
side panel.
LOCATION
1. Position the oven in its approximate working position.
2. The unit should be positioned so that the control panel and oven shelves are easily reachable for loading and unloading.
CLEARANCES
To ensure correct ventilation for the motor and controls, the following minimum installation clearances are to be adhered to:
Top
8”. 20/ 0 mm
Rear
300mm / 12”.
Left-hand side
450mm / 18”.
Right-hand side
900mm / 36”.
·
Installation shall comply with local elec
trical, health and safety requirements.
·
It is most important that this oven is installed correctly and that oven operation is correct before use.
·
If you have any questions regarding the proper installation and / or operation of this oven, please contact your local
distributor.
Quali ed installation personnel are individuals, a rm or a company which either in person or through a representative are engaged
in and responsible for the installation of electrical wiring from the electric meter, main control box or service outlet to the electric
appliance.
Quali ed installation personnel, licensed and bonded, must be experienced in such work, familiar with all precautions required and
have complied with all requirements of state or local authorities having jurisdiction.
U.S. and Canadian Installations - All ovens, when installed, must be electrically grounded in accordance with local codes, or in the
absence of codes, with the National Electrical Code ANSI/NFPA 70 - Latest Edition and/or Canadian National Electrical Code C22.2
as applicable.
The ventilation of these ovens should be in accordance with local codes. In absence of local codes, refer
to the national ventilation code titled, Standard for the Installation of Equipment for the Removal of
Smoke and Grease Laden Vapors from Commercial Cooking Equipment, NFPA-96-Latest Edition.
The appliance is to be installed with a check valve in accordance with applicable federal, province and local codes.
FCT6/7G
FCT6/7E
IMPORTANT
INSTALLATION REQUIREMENTS
Summary of Contents for TCO6G
Page 1: ...Combi Oven Touch TCO6G MODELS TCO6E TCO7G TCO7E...
Page 15: ......
Page 19: ...Perforated GN 65 mm Deep perforated GN 65 mm deep Flat GN 65 mm Deep...
Page 34: ...Setting the cooking cycle Setting the cooking type Setting the operating set point...
Page 36: ...Cycle setting screen Defined cycle summary screen...
Page 40: ...Cycle summary screen to access My recipes My recipes screen Recipe replacement screen...
Page 45: ...Access to a special cycle Start of a special cycle...
Page 70: ......
Page 80: ......
Page 91: ......