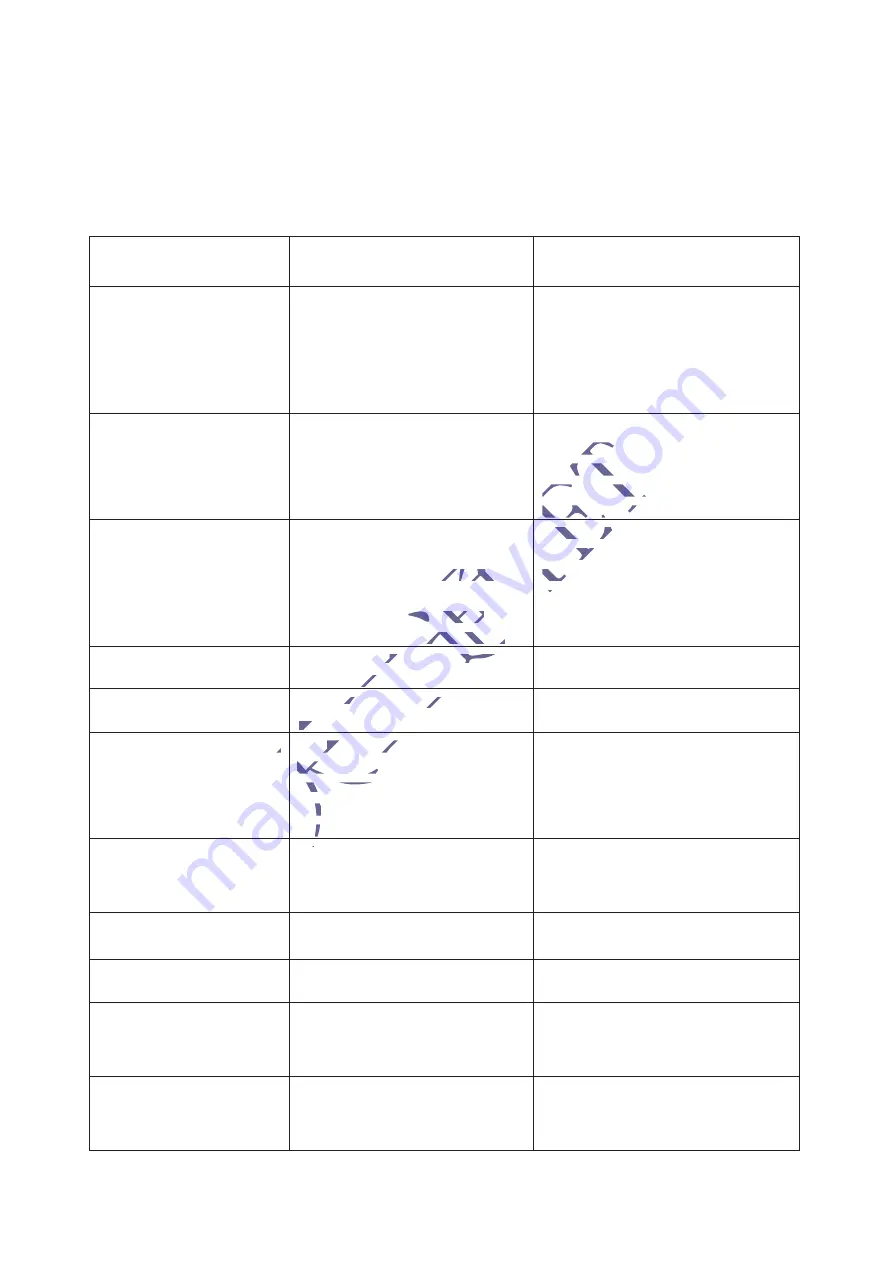
12
within 24 hours. If necessary, we will send technical personnel to the user site within 72 hours in the city, 3-5
days reaches the user site according to the distance outside the city until the problem is solved.
Complaints Tel: 022-26740033; Hotline: 022-26740033
(Note: The electric actuator should be stored in dry and non-corrosive circumstance.)
12.Trouble-shooting and remedy
Table 1
Trouble Cause
Remedy
1. Motor can’t started.
1. No power supply.
2. Too low power voltage.
3. Thermore lay (KH)acts.
4. T.SW acts.
5. Operation torque of valve is too high.
1. Inspect power supply.
2. Inspect voltage.
3. Wait for KH restoring to normal state.
4. Adjust T.SW to increase torque.
5. Forcibly starting.
6. Inspect valve.
2. Motor stops during open or
close operation.
1. T.SW act caused by overload.
2. Thermorelay acts.
3. Poor status of valve, excessive load.
1. In crease set value of torque if maximum
output torque allows.
2. Adjust thermorelay
3.1 Inspect valve and correct it into normal.
3.2 Operate the valve periodically if possible.
3.Motor can’t be stopped by
G.L.SW
1.The motor runs in reverse direction
2.Misadjustment of switch
3.Reset of screw is forgotten after
adjustment
4.Trouble on control power source
5. The gear of limit switch is damaged
1.Reverse the phase sequence
2.Readjust
3.Reset the adjusting screw
4.Inspect and remedy
5.Inspect and replace it with a new one if
necessary.
4. T.SW, G.L.SW acts, but the
motor can’t be stopped.
1.The motor runs in reverse direction
2.Trouble of grounding
1. Reverse the phase-sequence.
2. Inspect and measure resistance.
5. Indicating lamps for full open,
full close can’t be lighted up.
The T.SW acts, but the valve has not been
seated in position
Adjust T.SW
6.Remote position indication not
effective
1. The gear of signal output potentiometer
becomes loose so that the potentiometer
axle couldn’t be turned.
2. Improper power supply
3. The potentiometer is damaged.
1.Tighten the screw
2.Inspect the power supply
3.Replace it with a new one
7.The motor runs but valve is not
actuated
1. The Manual/Electric change over
mechanism is abnormal.
2.Locknut becomes loose
1. Dismantle, inspect and restore it to normal
operation.
2. Tighten and chisel the locknut
8. Manual operation can’t actuate
the valve.
The jaws of clutch and jaws of handwheel
body are out of meshing.
Turn the hand wheel a little to bring the jaws
into meshing.
9. Valve stem vibrates during
starting.
Stem nut becomes loose or improperly
tightened.
Dismantle the stem or pipe tap and tighten the
locknut.
10.Improper insulation
Invasion of rain water (improper sealing
of wire in wet)
1. Repair sealing parts.
2. Dry the electric elements and motor.
3. Pay attention to the sealing of wire inlet
11.Oil leakage
1. Sealing is damaged.
2.The ambient temperature is too high.
Internal pressure of main horsing rises up.
1.Inspect and repair
2.Loosen a screw which not affecting
working to vent air out (oil plug is preferred)
ཙҼ䙊7(7
rease
put torque a
torque
2. Adjust thermor
djust th
3.1 Inspect valve and c
3.1 Inspect valve an
3.2 Operate the valve
3.2 Operate the va
7(
tion
forgotten after
forgotten
rol power source
power source
f limit switch is damaged
tch is damaged
1.Reverse the pha
Reverse the
2.Readjust
djus
3.Reset th
3.Re
4.Insp
I
5
7(7
䙊7(
or runs in reverse direction
ns in reverse direction
uble of grounding
f gr
Ҽ䙊
he T.SW acts, but the valve h
W acts, but the valv
seated in position
sea
Ҽ
ཙ
not
ot
1. The gear of signal ou
he gear of sign
becomes loose so
becomes loose
axle couldn’t b
xle couldn’t b
2. Improper
Im
3. The p
Th
ཙҼ
ཙ
ཙ