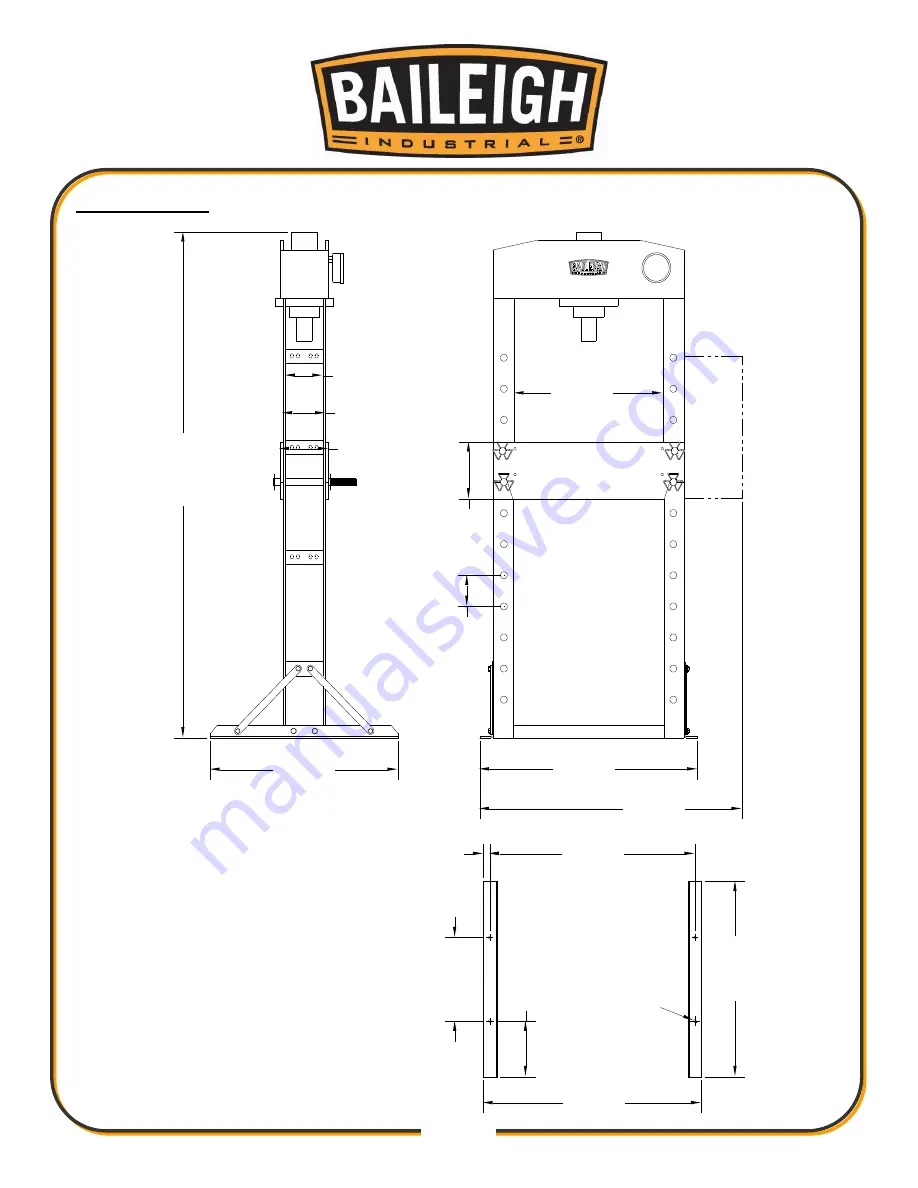
13
13
DIMENSIONS
Pne
umati
c
R
71
.0
0
"
[1
80
3
.4
0
]
27.50"
[698.50]
32.00"
[812.80]
38.50"
[977.90]
30.12"
[765.05]
0.94"
[23.88]
27
.5
0
"
[69
8.5
0
]
32.00"
[812.80]
7.81
"
[19
8.3
7
]
11
.7
5
"
[29
8.4
5
]
Ø0
.41"
[Ø1
0.31]
5.45"
[138.43]
6.25"
[158.75]
7.17"
[182.12]
21.76"
[552.70]
4.38
"
[11
1.1
3
]
8.00
"
[20
3.2
0
]
Summary of Contents for HSP-30A
Page 10: ...8 8 MACHINE SAFETY LABELS...
Page 17: ...15 15 GETTING TO KNOW YOUR MACHINE 7 13 11 9 12 31 Hardware 5 10 6...
Page 28: ...26 26 PARTS DIAGRAM FRAME...
Page 30: ...28 28 Item Description Qty 34 Pump Assembly 1 35 Release Valve 1 36 Plug 1 37 Oil Hose 2...
Page 31: ...29 29 PARTS DIAGRAM HYDRAULIC ASSEMBLY...
Page 34: ...32 32 PARTS IDENTIFICATION MAIN CYLINDER...
Page 36: ...34 34 HYDRAULIC SCHEMATIC Handle Air P...
Page 38: ...36 36 NOTES...
Page 39: ...37 37 NOTES...