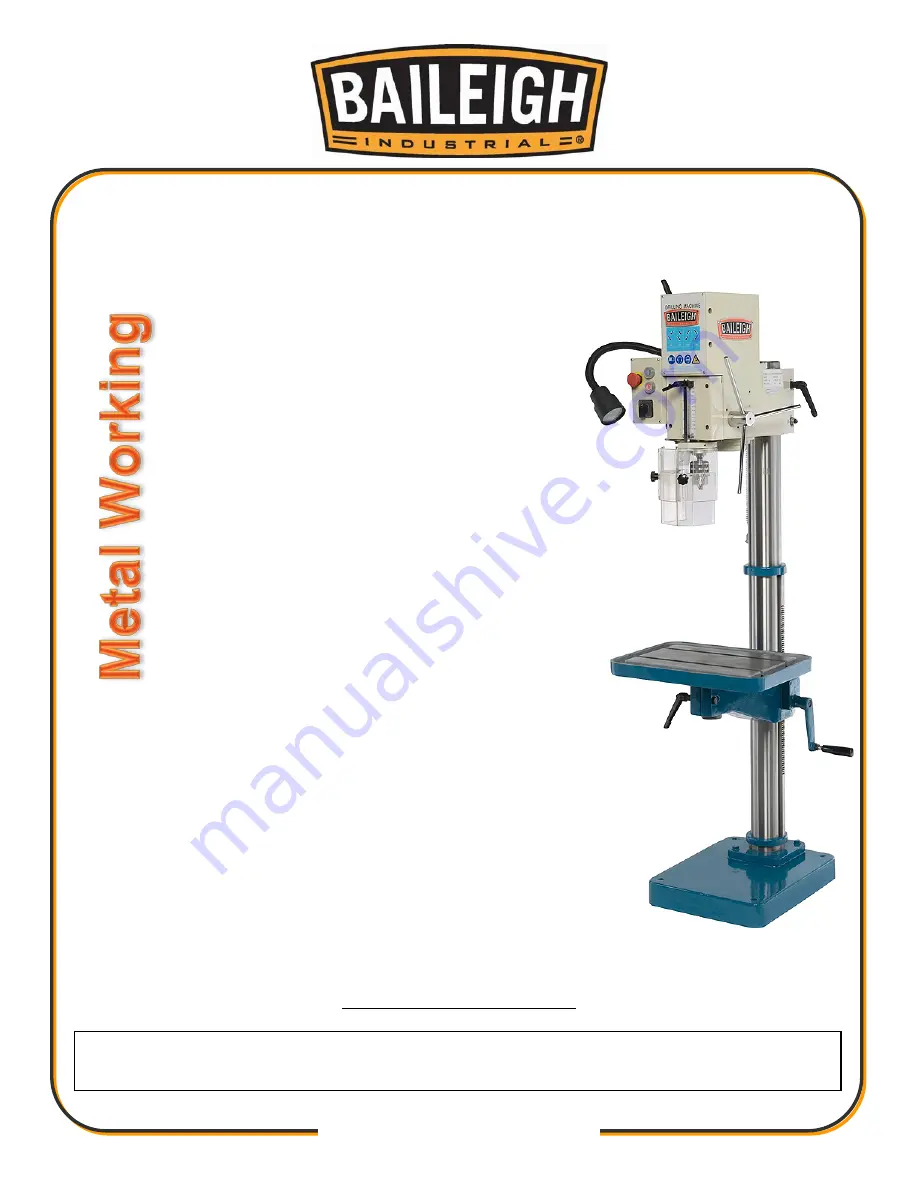
OPERATOR’S MANUAL
GEAR DRIVE DRILL PRESS
MODEL: DP-1000G
© 2015 Baileigh Industrial, Inc.
REPRODUCTION OF THIS MANUAL IN ANY FORM WITHOUT WRITTEN APPROVAL OF BAILEIGH INDUSTRIAL, INC.
IS PROHIBITED. Baileigh Industrial, Inc. does not assume and hereby disclaims any liability for any damage or loss
caused by an omission or error in this Operator’s Manual, resulting from accident, negligence, or other occurrence.
Rev. 05/2015
Baileigh Industrial, Inc.
P.O. Box 531
Manitowoc, WI 54221-0531
Phone: 920.684.4990
Fax: 920.684.3944
Summary of Contents for DP-1000G
Page 3: ...ELECTRIC BOX DIAGRAM 39 Electrical Box Parts List 40 ELECTRICAL SCHEMATIC 41 ...
Page 15: ...12 12 OVERALL DIMENSIONS ...
Page 16: ...13 13 GETTING TO KNOW YOUR MACHINE F B L N M R G U A P H J C E O D K I S T Q ...
Page 24: ...21 21 DRILL HEAD DIAGRAM ...
Page 26: ...23 23 GEARBOX DIAGRAM ...
Page 28: ...25 25 ROTOR SHAFT DIAGRAM ...
Page 30: ...27 27 2nd SHAFT DIAGRAM ...
Page 32: ...29 29 3rd SHAFT DIAGRAM ...
Page 34: ...31 31 COLUMN DIAGRAM ...
Page 36: ...33 33 WORM GEAR BOX COMPLETE DIAGRAM ...
Page 38: ...35 35 FEEDSHAFT DIAGRAM ...
Page 40: ...37 37 SPINDLE SLEEVE DIAGRAM ...
Page 42: ...39 39 ELECTRIC BOX DIAGRAM ...
Page 44: ...41 41 ELECTRICAL SCHEMATIC ...
Page 46: ...43 43 NOTES ...
Page 47: ...44 44 NOTES ...