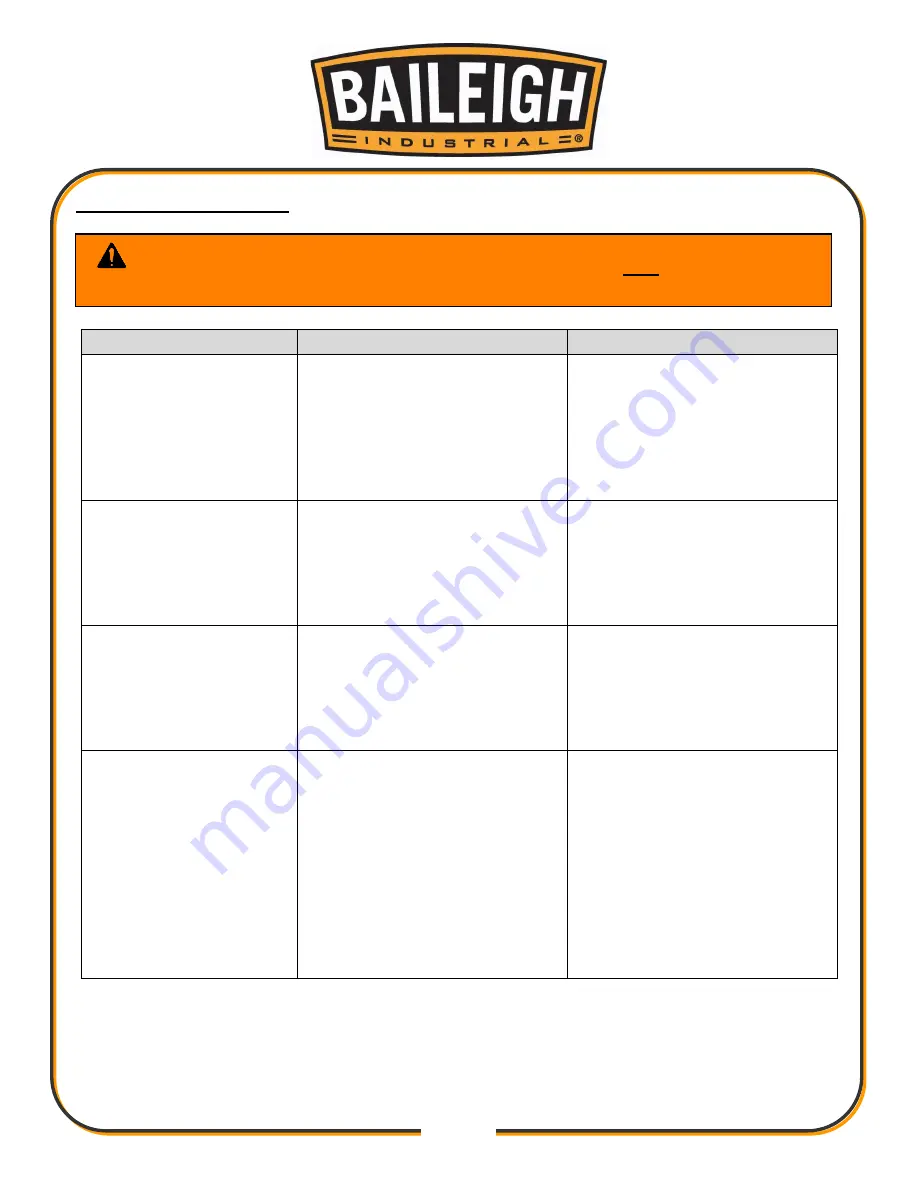
30
30
TROUBLESHOOTING
Symptom
Possible Cause(s)
Corrective Action
1. The motor cannot
start.
1. The power isn't on.
2. The fuse of electric circuit has
blown.
3. The electric cable is
damaged.
4. The switch isn’t “on”.
5. The motor is damaged.
1. Check all the electric circuit.
2. Change the fuse.
3. Repair or change the cable.
4. Check the switch.
5. Change the motor.
2. The saw blade cannot
cut or the cutting speed is
slow.
1.The saw blade is installed
backwards
2. The saw teeth contain
unwanted grit.
3. The saw has not been used
for long time.
1. Turn over the saw blade and
install it again.
2. Remove the grit, re-sharpen
the blade teeth.
3. Repair and re-grind the saw
teeth to make them sharp again.
3. Slipping saw blade.
1. The saw blade is not straight.
2. The upper wheel isn’t parallel
with the lower wheel,
3. The guides are not adjusted
correctly
1. Reinstall the saw blade.
2. Adjust the upper wheel to
make it parallel with the lower
one.
3. Re-adjust the guides so the
blade does not slip
4. Excessive Blade
Breakage.
1. Incorrect blade tension.
2. Incorrect speed or feed.
3. Blade rubs on wheel flange.
4. Teeth too coarse for material.
5. Teeth in contact with the
material before the saw is
started.
6. Misaligned guides.
7. Cracking of blade weld.
1. Adjust to where blade just
does not slip on wheel.
2. Consult machine chart or
handbook.
3. Adjust the wheel alignment.
4. Contact Baileigh Industrial for
recommended blade type.
5. Contact material after blade
has been started.
6. Adjust as necessary.
7. Replace blade
WARNING:
Make sure the electrical disconnect is OFF before working on
the machine.
Summary of Contents for WBS-12
Page 28: ...26 26 PARTS DIAGRAM...
Page 33: ...31 31 NOTES...
Page 34: ...32 32 NOTES...
Page 35: ...33 33 NOTES...