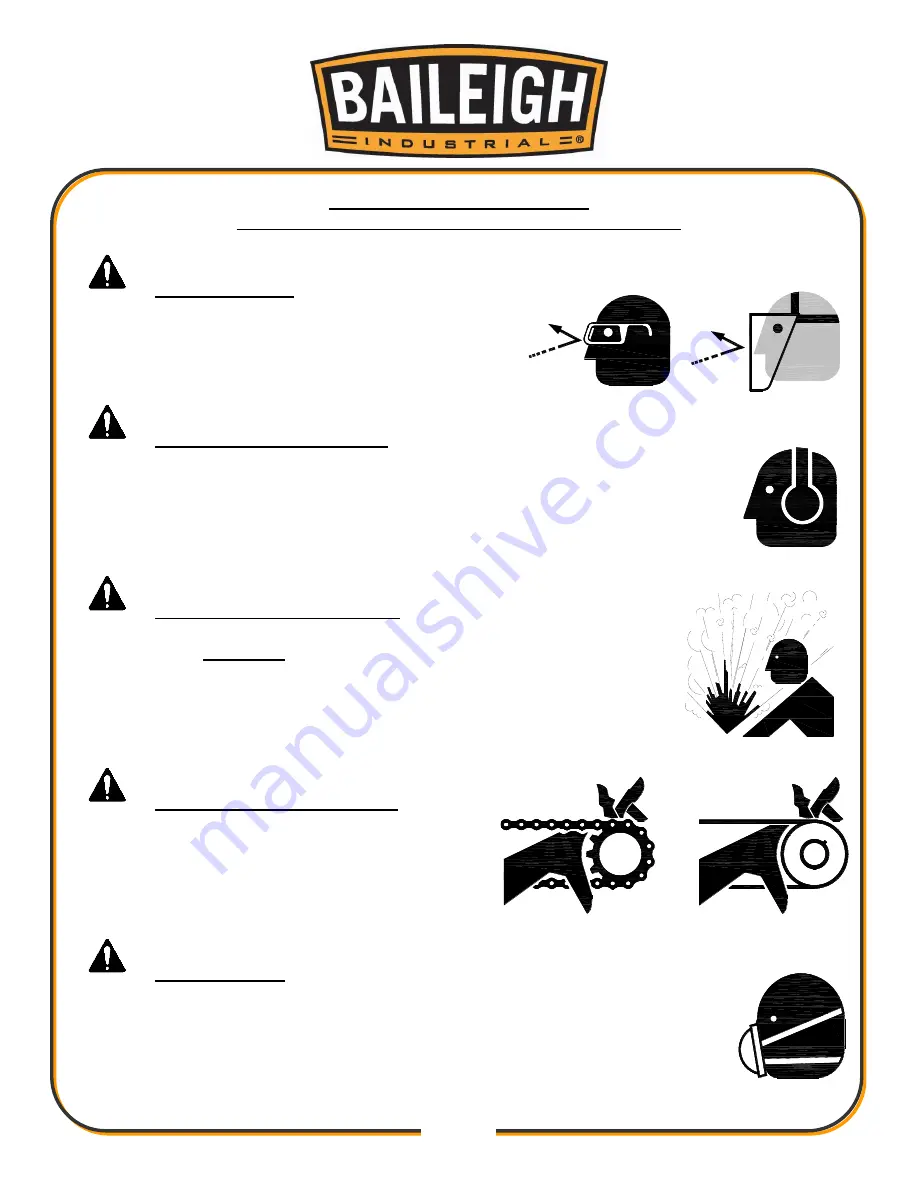
5
5
SAVE THESE INSTRUCTIONS.
Refer to them often and use them to instruct others.
PROTECT EYES
Wear safety glasses or suitable eye protection
when working on or around machinery.
PROTECT AGAINST NOISE
Prolonged exposure to loud noise can cause impairment or loss of
hearing. Wear suitable hearing protective devices such as ear muffs or
earplugs to protect against objectionable or uncomfortable loud noises.
HYDRAULIC HOSE FAILURE
Exercise
CAUTION
around hydraulic hoses in case of a hose or
fitting failure.
BEWARE OF PINCH POINTS
Keep hands and fingers clear of all potential
pinch points. These include sprockets and
chains along with belts and pulleys.
DUST HAZARD
Wear appropriate dust mask. Dust created while using machinery can
cause cancer, birth defects, and long term respiratory damage. Be aware
of the dust hazards associated with all types of materials.
Summary of Contents for BSVT-18P
Page 18: ...15 15 OVERALL DIMENSIONS...
Page 19: ...16 16...
Page 22: ...19 19 GETTING TO KNOW YOUR MACHINE A B C D F E I H G J K L M O P Q R S N...
Page 40: ...37 37...
Page 51: ...48 48 ELECTRICAL DIAGRAM...
Page 52: ...49 49 PNUEMATIC HYDRAULIC DIAGRAM...
Page 53: ...50 50 NOTES...
Page 54: ...51 51 NOTES...
Page 55: ...52 52 NOTES...