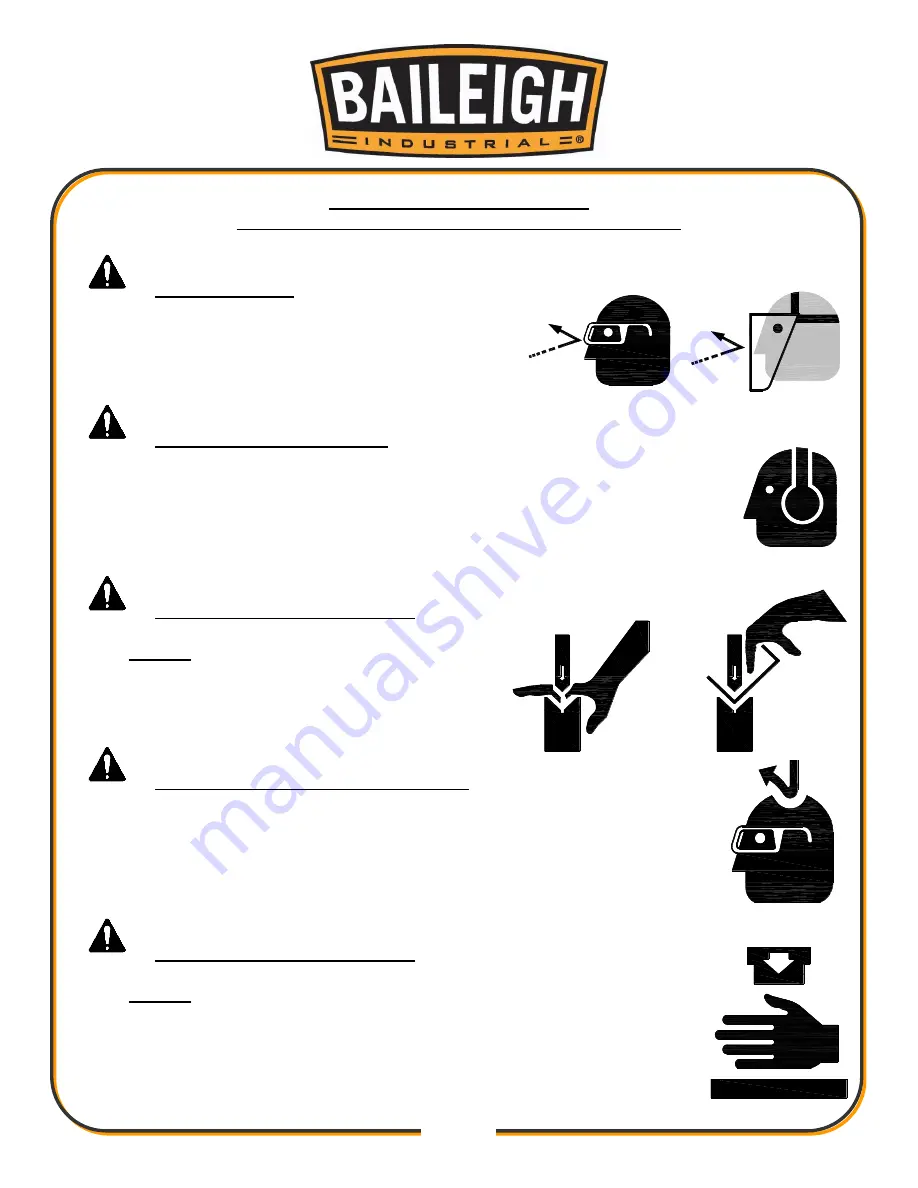
5
5
SAVE THESE INSTRUCTIONS.
Refer to them often and use them to instruct others.
PROTECT EYES
Wear safety glasses or suitable eye protection
when working on or around machinery.
PROTECT AGAINST NOISE
Prolonged exposure to loud noise can cause impairment or loss of
hearing. Wear suitable hearing protective devices such as ear muffs or
earplugs to protect against objectionable or uncomfortable loud noises.
BEWARE OF CRUSH HAZARD
NEVER
place your hands, fingers, or any
part of your body in the die area of this
machine.
KEEP CLEAR OF MOVING OBJECTS
Always be aware of the position of the material as it is being formed.
The material can be heavy and can swing back suddenly causing
serious body or head injuries.
BEWARE OF CRUSH HAZARD
NEVER
place your hands, fingers, or any part of your body in the die
area of this machine.
Summary of Contents for BP-3305CNC
Page 3: ...Back Gauge Adjustment 48 BEND TONNAGE CHART 50...
Page 17: ...14 14...
Page 21: ...18 18 GETTING TO KNOW YOUR MACHINE A B M L K D C E F G I H J I G...
Page 22: ...19 19 N S T U X V O Q P R W...
Page 44: ...41 41 INCLUDED LOWER AND UPPER TOOLING Lower Tool Die Upper Tool Punch...
Page 54: ...51 51 NOTES...
Page 55: ...52 52 NOTES...