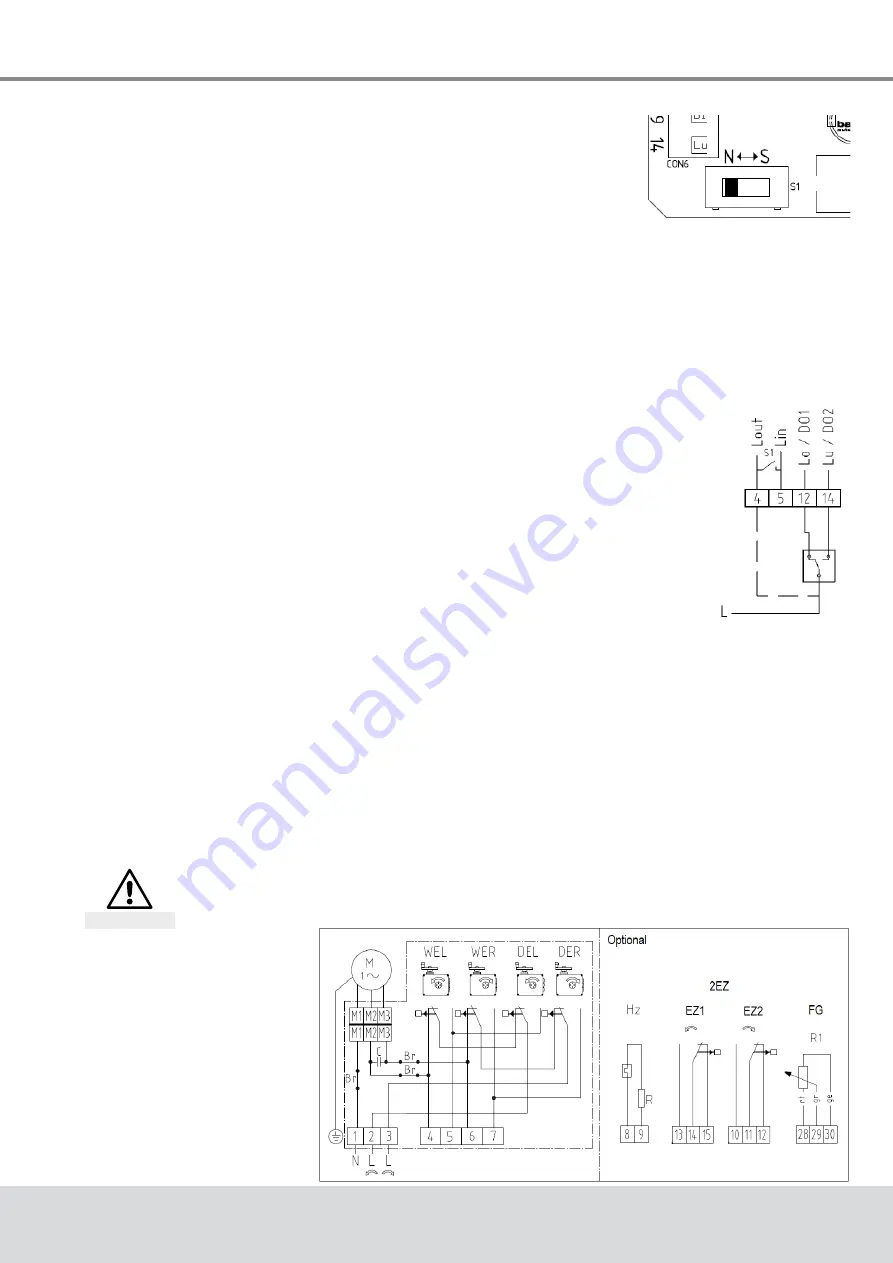
BA_375-E42_01_DEF_MJ_4419
19 |
32
W. Baelz & Sohn GmbH & Co.
· Koepffstrasse 5 · 74076 Heilbronn · Germany ·
www.baelz.de Seite | Page
Motorized Rotary Actuator
baelz 375-E42
7.2.4 Normal and safety modes
In normal mode the position of the valve is controlled by the set
value at analogue input AI2. The N↔S switch shown in the picture
on the right is set to normal mode (N). In normal mode, no external
control systems can be connected to terminals 12 and 14.
7.2.5 Safety mode: freeze protection and excessive temperature
In safety mode the actuator can be sent to a safe position (extended / retracted, depending on
the direction of action of the valve) in case of failure or malfunctioning of the microcontroller.
To operate the Baelz 7020 in connection with an external freeze protection and/or excessive
temperature thermostat, set the N↔S switch to safety mode (S).
Connect the freeze protection and/or excessive temperature thermostat according to desired
function and priority. Be sure to take the direction of action into account! See wiring diagrams
in the baelz 7020 operating instructions.
7.2.6 3-point control with a continuous output signal
1. Set the positioner up and wire to power supply as described
previously and initialize as described in section 7.5.2.
2. To deactivate the error signal, if desired, set the DIP-switch 11 to 1
("ON") and change the following values in the menu item "CA" using
WinBas Tools (on PC, see baelz 7020 operating instructions
)
:
●
AD to 0
●
EFP to 0.0%
●
LA to 1
(If you don't mind the red LED error signal, step 2 can be left out
completely. This has no effect on the function of the positioner.)
3.
Set the N↔S switch (
) to "S" and wire as shown in
(the positioner must
remain connected to the power supply throughout).
4. The required signal can now be picked up on AO1 and AO2.
IMPORTANT NOTE
: Before any further re-initialization of the device, disconnect terminals 12
and 14 and set the N↔S switch to normal operation (N).
7.3 Wiring diagrams and allocation of connection terminals
Disconnect actuator from power supply before starting work
Danger
7.3.1 Wiring diagram
Fig. 7: N
↔
S-switch
Fig. 8: Wiring diagram
3-point-signal
Fig. 9: Wiring diagram
basic actuator