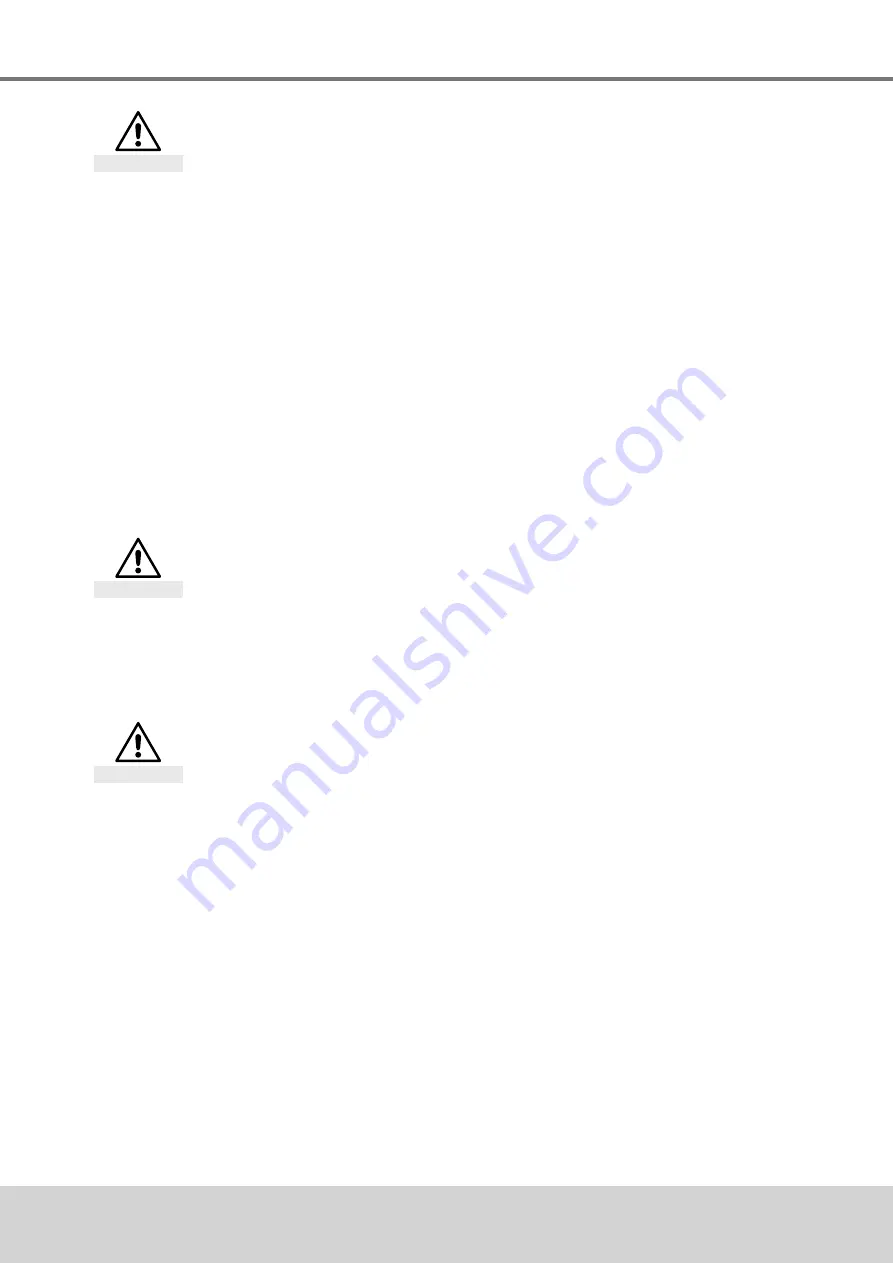
BA_1
11_00_DEF_MJ_0419
13 |
23
W. Baelz & Sohn GmbH & Co.
· Koepffstrasse 5 · 74076 Heilbronn · Germany ·
www.baelz.de Seite | Page
Straight-Tube Heat Exchanger baelz 111 / baelz 112
5.3 During operation
If vibration, noise, reduced power or other disturbances occur during operation, please refer to the
Troubleshooting table on page 16 and contact Baelz customer service if necessary.
Observe the following instructions for safe commissioning!
Beware
12. Open the condensate manual control and isolating valve very slowly to put the steam heat transfer
station into operation: First open the manual control valve by only one turn. After 15 minutes, check
the resulting temperature rise. If the maximum supply temperature (secondary output, 04) is already
exceeded, the condensate control valve is too large. Turn the manual control valve back accordingly. If
the supply temperature is not reached, open the manual control valve by one more turn. Wait another
15 minutes and repeat the temperature check and, if necessary, correct the hand wheel position. Now
secure the manual control valve so that it cannot be unintentionally misadjusted.
13. Since the temperature provides only limited information about the heat output, the correct condensate
discharge rate must in certain cases be set on the manual control valve using a condensate meter. The
approx. condensate discharge capacity in l/min, which must flow at nominal capacity, is obtained by
dividing the heat output in kcal/h by the numerical value 33000. If the capacity is given in kW, it must be
divided by the numerical value 38 in order to obtain the approx. condensate quantity in l/min. Particularly
advantageous is when the condensate control valve contains a built-in flow limiter. It can be easily
adjusted to the maximum flow rate.
14. Now you can switch on the automatic operation. The automatic condensate control valve is controlled by
the controller by means of Open and Close pulses depending on the power consumption. Observe the
system for a few more hours and note the pressure and temperature values. Check the safety devices
for correct function by simulating controls as they may occur during operation.
After 1-2 hours of operation, tighten the screws of the seals!
Caution
15. It is imperative to tighten the screw connections of all seals gradually and evenly after 1-2 hours of operation.
See also chapter 6.4. This measure is necessary because seals change under the influence of heat. If
the retightening is not carried out in time, the seals may be damaged and the device may leak. This can
result in seals having to be replaced and, under certain circumstances, sealing surfaces having to be
reworked.
In new systems, strainers must be cleaned after the first few days.
Caution
16.
Clean the strainers to remove debris that may have been flushed from the system's recently put into
service pipes and fittings.
17. Security valves are usually set for the pressure value ordered. Corrections must be made at the
manufacturer's factory. Installations subject to inspection must be inspected after completion by the body
designated in accordance with the PED. The certificate of a factory construction and water pressure test
must be submitted.