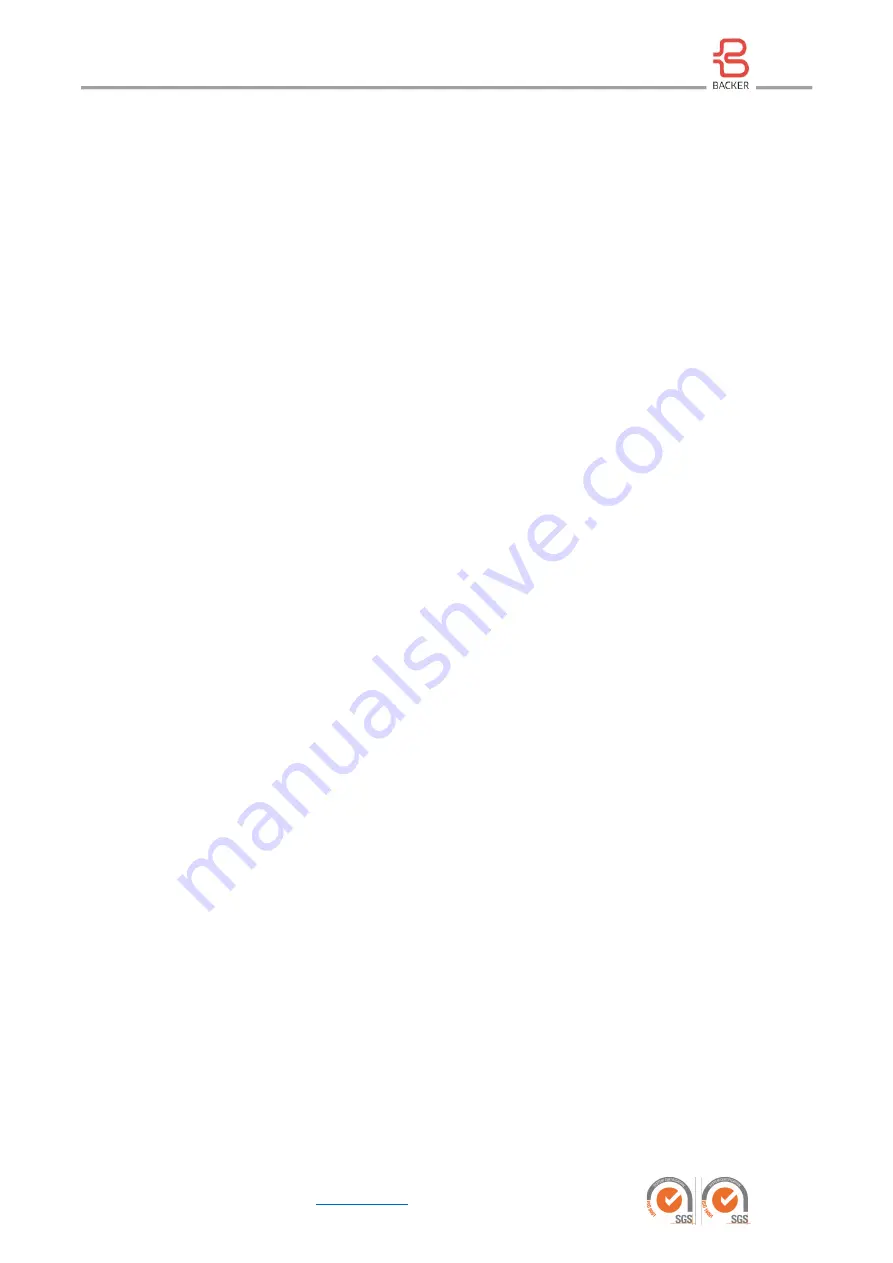
HRDc/HRDi Controller - Operating Manual
Heatrod Elements Ltd. Unit 10 Top Deck, Smethurst lane, Farnworth, Bolton BL4 0AN
Tel:(0161) 727 3713 Fax:(0161) 727 3733 Email:
info@heatr
Printed copies valid on day of print only. Check quality document register QM00 to ensure latest version prior to use
■
This mode is only available if the RTC has been set (which initially require
■
Schedules can only be crated in Devman and with a
○
Timer – see previous description of basic use in
■
Uses Timer Set Value as the target temperature to heat to.
■
Timer Seconds is the duration the heater will heat for irrespective of the attained
temperature.
○
Timer Set Point – see previous
■
Uses Timer Set Value as the target temperature to heat to.
■
Timer Seconds is the duration the heater will heat for once the desired Timer Set Value
temperature has been first measured.
●
Duty Control Modes
○
Single Element – just one relay will be energized during duty
○
Single Element Two Pole
similar to tandem but informs the relay self
○
Two Element Tandem
○
Three Element Tandem
○
Two Element stepped
subsequently switch a second relay w
field “Stepped Mode Threshold (2)”
○
Three Element stepped
Threshold (3) to determine when a
●
Up to three Outputs for each controller can be selected to support the above tandem and stepped control
modes a single PID controller can
○
Note – there is no “collision” checking in the UI to prevent mor
output, however the controller itself will not
controller (prioritised by increasing
●
PID (Proportional, Integral &
response for a give process under control
○
Default values give conservative control without integration to avoid overshoot of delay
locations.
○
Auto PID tune is availab
●
Ramp (s / C) allows changes in setpoint to be limited to change at rate
seconds. This parameterapplies to all modes including schedule, ma
following section on Built-in Timer Modes
●
User calibration values
○
PID 1’s sensor values can be offset and scaled using the following formula:
■
Temperature =
○
The temperature can also be dynamically scal
flow affects or to include
measure output whenever an output relay is energised for PID1. I.e.
■
Temperature =
■
Built-in Timer modes
HRD units can perform accurate relative timed setpoint profiling with or without an internet connection using the
internal Real Time Clock (RTC). For date and time of day based
a clock source to initialise HRD’s RTC, hence this latter type of scheduling is only configurable in the Devman UI.
Operating Manual
Heatrod Elements Ltd. Unit 10 Top Deck, Smethurst lane, Farnworth, Bolton BL4 0AN
Printed copies valid on day of print only. Check quality document register QM00 to ensure latest version prior to use
This mode is only available if the RTC has been set (which initially require
Schedules can only be crated in Devman and with a Backer IoT service plan
see previous description of basic use in ‘Getting Started’
Uses Timer Set Value as the target temperature to heat to.
Timer Seconds is the duration the heater will heat for irrespective of the attained
temperature.
see previous description of basic use in Getting Started
Uses Timer Set Value as the target temperature to heat to.
Timer Seconds is the duration the heater will heat for once the desired Timer Set Value
temperature has been first measured.
just one relay will be energized during duty
Single Element Two Pole – two relays are used to switch a single element (
similar to tandem but informs the relay self-check to know only one has live ac connected.
t Tandem – switches two element circuits simultaneously.
Three Element Tandem – switches three elements simultaneously
Two Element stepped – will switch the first selected element on for the initial duty requirement and
subsequently switch a second relay when the duty required exceeds the
field “Stepped Mode Threshold (2)”.
Three Element stepped – is similar toabove but will use the additional threshold “Stepped Mode
Threshold (3) to determine when a third relay would be energised for the highest duty requirements.
Up to three Outputs for each controller can be selected to support the above tandem and stepped control
modes a single PID controller can be configured for.
there is no “collision” checking in the UI to prevent more than one controller using the same
output, however the controller itself will not energise any output that is being used by another
ed by increasing Control number).
Differential) parameters can be entered to minimise error,
response for a give process under control.
Default values give conservative control without integration to avoid overshoot of delay
Auto PID tune is available in a subsequent firmware release (Q3 2021).
Ramp (s / C) allows changes in setpoint to be limited to change at rate of 1°C over the given duration in
applies to all modes including schedule, manual, timer and Timer Set
in Timer Modes.
PID 1’s sensor values can be offset and scaled using the following formula:
Temperature = “Calibration 1” + (“calibration 2”+1) x sensor value.
The temperature can also be dynamically scaled depending on the heating duty to compensate for
flow affects or to include hysteresis-like effects. The temperature will add Calibration 3 to the
measure output whenever an output relay is energised for PID1. I.e.
Temperature = “Calibration 1” + “calibration 3” + (“calibration 2”+1) x sensor value.
HRD units can perform accurate relative timed setpoint profiling with or without an internet connection using the
. For date and time of day based scheduling an Internet connection is required to provide
, hence this latter type of scheduling is only configurable in the Devman UI.
pg. 14
This mode is only available if the RTC has been set (which initially requires Internet access)
acker IoT service plan
Timer Seconds is the duration the heater will heat for irrespective of the attained
Timer Seconds is the duration the heater will heat for once the desired Timer Set Value
two relays are used to switch a single element (live and neutral) - this is
check to know only one has live ac connected.
r the initial duty requirement and
hen the duty required exceeds the thresholdentered into the
above but will use the additional threshold “Stepped Mode
for the highest duty requirements.
Up to three Outputs for each controller can be selected to support the above tandem and stepped control
e than one controller using the same
energise any output that is being used by another
Differential) parameters can be entered to minimise error, overshoot, and
Default values give conservative control without integration to avoid overshoot of delay-heavy sensor
C over the given duration in
ual, timer and Timer Set Point - see
“Calibration 1” + (“calibration 2”+1) x sensor value.
ed depending on the heating duty to compensate for
The temperature will add Calibration 3 to the
ation 3” + (“calibration 2”+1) x sensor value.
HRD units can perform accurate relative timed setpoint profiling with or without an internet connection using the
scheduling an Internet connection is required to provide
, hence this latter type of scheduling is only configurable in the Devman UI.