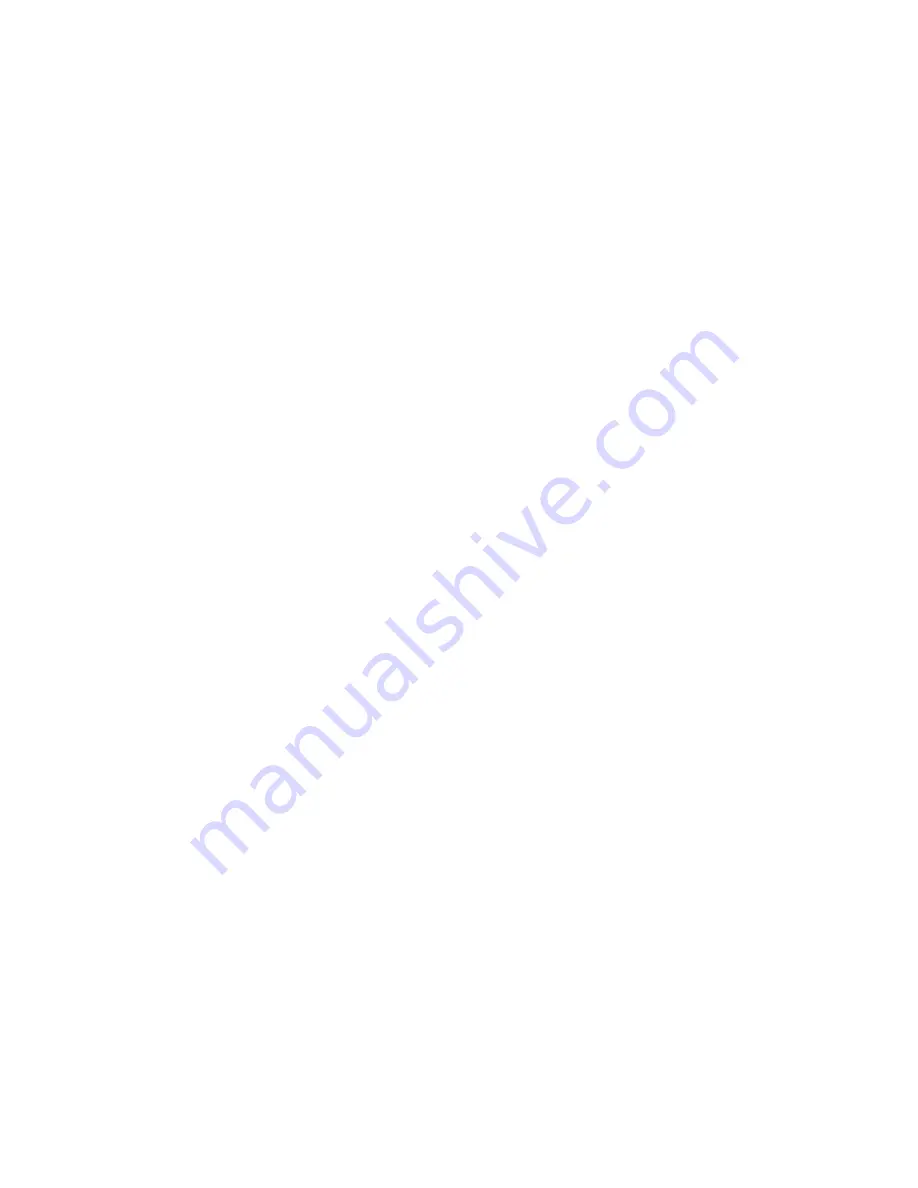
Model 5100E
–
Introduction and Overview
1.5.4
7-Segment Alphanumeric Display
The 7-Segment alphanumeric display feeds back information from the Model 5100E to the user via the
control panel. The primary purpose of the 7-Segment display is to show the oxygen concentration readout.
It is also used for feedback of operational status, fault codes, and other information necessary to perform
system setup and maintenance.
1.5.5
RUN Indicator LED
The purpose of the RUN Indicator LED is to inform the user via the control panel that the Model 5100E is
measuring the concentration of the sample gas and updating the display.
1.5.6
Alarm-1 Indicator LED
The purpose of the Alarm-1 Indicator LED is to inform the user via the control panel that the measured
oxygen concentration has exceeded the alarm-1 threshold; alarm-1 LED and its associated relay are in
active mode.
1.5.7
Alarm-2 Indicator LED
The purpose of the Alarm-2 Indicator LED is to inform the user via the control panel that the measured
oxygen concentration has exceeded the alarm-2 threshold; alarm-2 LED and its associated relay are in
active mode.
1.5.8
Fault Indicator LED
The purpose if the Fault Indicator LED is to inform the user via the control panel that at least one system
fault is active. Note that when the fault Indicator LED is active, the fault relay will also be active (open).