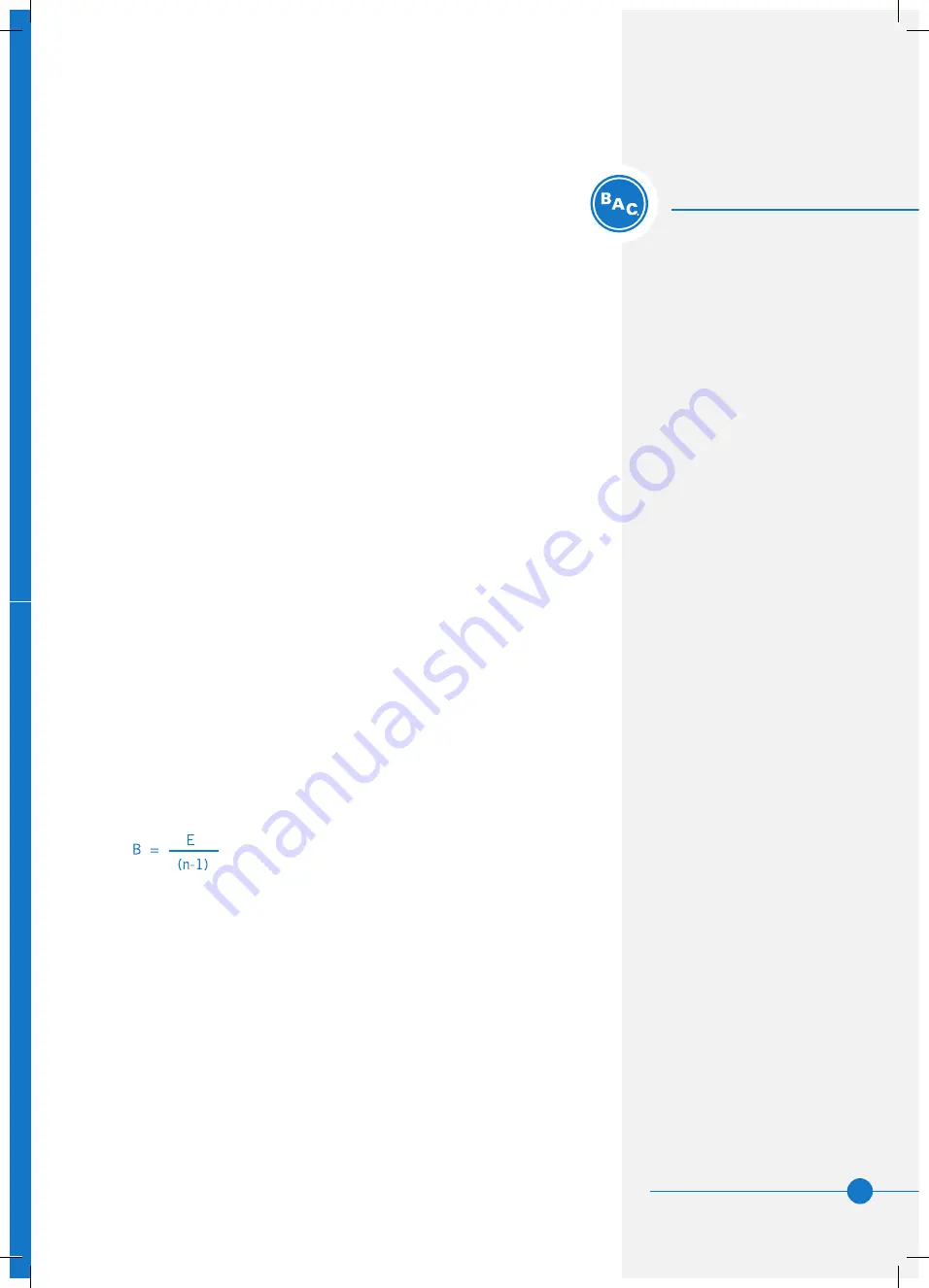
31
W W W . B A L T I M O R E A I R C O I L . C O M . A U
M A R 2 1 0 - 2
RC SERIES
Bleed Rate
Bleed Rate
In evaporative cooling, evaporation of a small portion of the
recirculating spray water as it flows through the equipment causes
the cooling effect. As this water evaporates, the impurities originally
present remain in the recirculating water. The concentration of the
dissolved solids increases over time and can reach unacceptable
levels. In addition, airborne impurities are often introduced into the
recirculating water. If these impurities and contaminants are not
effectively controlled, they can cause scaling, corrosion, and sludge
accumulations that reduce heat transfer efficiency and increase system
operating costs, potentially shortening the useful life of the equipment.
The degree to which dissolved solids and other impurities build up in
the recirculating water may be defined as the cycles of concentration.
Specifically, cycles of concentration equal the ratio of the concentration
of dissolved solids (for example - chlorides, sulfates, etc.) in the
recirculating water to the concentration of the same material in the
make-up water.
• In order to optimise heat transfer efficiency and maximize
equipment life, bleed or blowdown a small amount of recirculating
water from the system. This controls the cycles of concentration to
maintain the quality of the recirculating water within the guidelines
given in Table 2, on page 24.
• Replenish the “bleed” water with fresh make-up water, thereby
limiting the build-up of impurities.
• Bleed/blowdown:
- To minimize water usage, accomplish the bleed automatically
through a solenoid valve controlled by a conductivity meter. The set
point is the water conductivity at the desired cycles of concentration
and should be determined by a water treatment expert.
Bleed Line Calculations:
Bleed rate is determined by the following formula:
Where:
B = Bleed Rate (L/S)
E = Evaporation Rate (L/S) = Q (L/S) x R (ºC) x 0.0018
Q = Process Fluid Flow Rate (L/S)
R = Range (ºC)
n = Desired Number of Cycles of Concentration = CR/CM
The evaporation rate is dependent on the wet bulb temperature and
load. The equation shown above provides the maximum bleed rate
on the design day. Contact your local BAC representative for an exact
calculation based on specific site conditions.