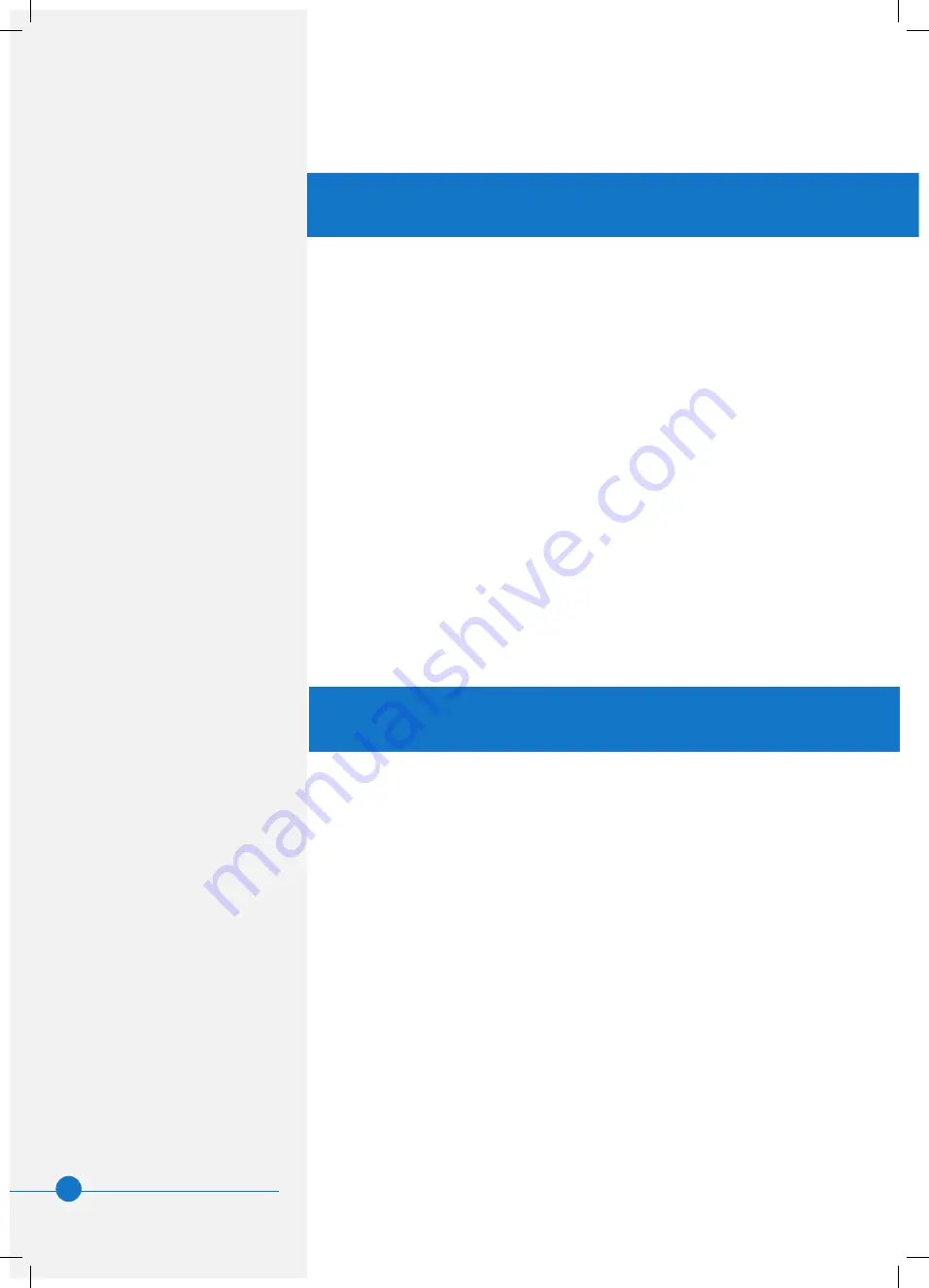
26
W W W . B A L T I M O R E A I R C O I L . C O M . A U
M A R 2 1 0 - 2
• Passivation is the formation of a protective, passive, carbonate
layer on galvanized steel surfaces, including unit panels and
galvanized coils.
• To provide maximum protection from corrosion on newly installed
units take special measures to passivate galvanized steel surfaces.
• To ensure proper passivation of the galvanized steel, keep the pH of
the circulating water between 7.0 to 8.2 for four to eight weeks after
start-up, or until new zinc surfaces turn dull gray in colour.
• If white rust forms on galvanized steel surfaces after the pH is returned
to normal service levels, the passivation process must be repeated.
Passivation
Chemical Treatment Requirements
Chemical treatment programs must meet the following requirements:
• The chemicals must be compatible with the unit materials of
construction as well as other materials used in the system (pipe,
heat exchanger, chiller, etc.)
• Chemical scale and corrosion inhibitors, particularly acid (if used),
should be introduced into the circulating water through automatic
feeders. This should be done at a point in the system where
total mixing and dilution occur before reaching the evaporative
cooling equipment. The preferred injection point for chemical
scale and corrosion inhibitors is on the discharge side of the
system circulating pump(s). These chemicals should not be batch
fed directly into the unit’s cold water basin or water distribution
system, as this can severely damage areas directly contacted.
• When chlorine is added to the system, free residual chlorine should
not exceed 1 ppm, except during start-up if biological shock
treatment is utilized during treatment. Refer to “Start-Up” on page
5 for limits. Exceeding this limit may accelerate corrosion.