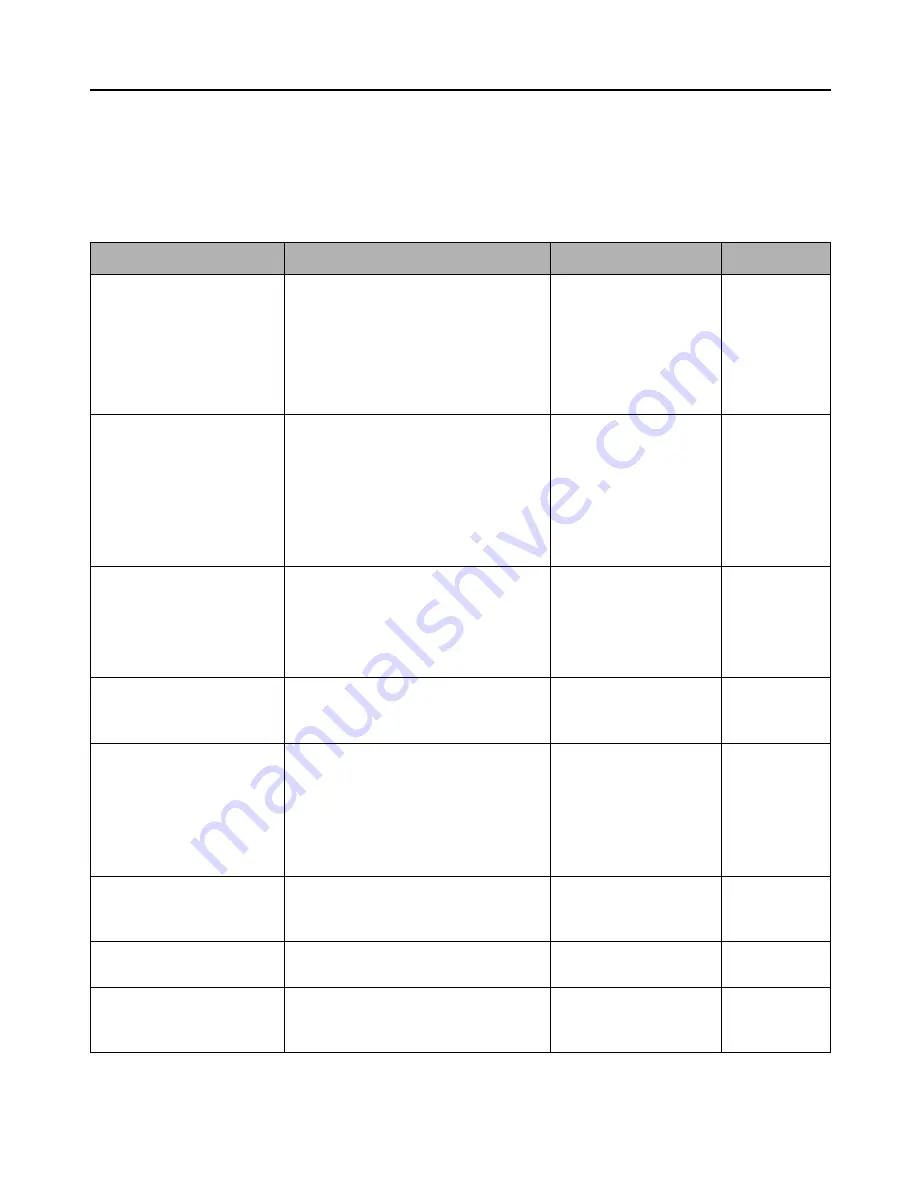
24
BEFORE YOU CALL FOR SERVICE
Your new serger was carefully inspected and tested at the factory and was in perfect working order when
shipped.
Under normal conditions, if you carefully follow instructions for threading, operating and maintenance, your
machine will give you years of trouble-free service.
Occasional difficulties are usually caused by a condition that can be easily remedied with a minor adjustment.
Some possible problems, their causes and corrections are given here.
REF. PAGE
5
11, 13, 15, 17
5
6-9
6-9
5
5
13
5
6-9
11, 13, 15, 17
10
5
5
13
23
12
12
11, 13, 15, 17
12
11, 13, 15, 17
23
4
4
CORRECTION
Reset needle
Loosen thread tensions
Insert new needle
Rethread machine
Rethread machine
Insert new needle
Reset needle
Increase pressure
Insert correct needle
Rethread machine
Loosen thread tensions
Do not pull fabric
Choose correct needle
and thread
Reset needle
Increase pressure
Change lower blade
Readjust stitch length
Readjust differential feed
Loosen thread tensions
Readjust seam width
Check thread tensions
Clean the machine
Check plug
Turn on the switch
CAUSE
• Needle inserted incorrectly
• Thread tensions are too tight
• Bent or blunt needle
• Machine not properly threaded
• Threads are caught in incorrect guide
• Bent or blunt needle
• Needle inserted incorrectly
• Pressure on foot insufficient
• Incorrect needle size or type
• Machine incorrectly threaded
• Tensions set too high
• Pulling fabric while sewing
• Incorrect size needle or thread for
fabric being sewn
• Needle inserted incorrectly
• Pressure on presser foot insufficient
• Lower blade is dull
• Stitch length not suitable for fabric
• Differential feed not suitable
• Thread tensions are too tight
• Seam width not suitable for fabric
• Tensions not adjusted properly
• Dirt or lint in stitching mechanism
• Cord not plugged into electrical outlet
• Light and power switch not on
PROBLEM
THREAD BREAKS
MACHINE SKIPS
STITCHES
NEEDLE BREAKS
MACHINE DOES NOT
FEED PROPERLY
FABRIC PUCKERS
LOOSE STITCHES OR
LOOPS FORMED
MACHINE RUNS HEAVILY
MACHINE WILL NOT SEW
Summary of Contents for A-LINE Lauren BL450A
Page 1: ......
Page 28: ...62180 BL450A B8...