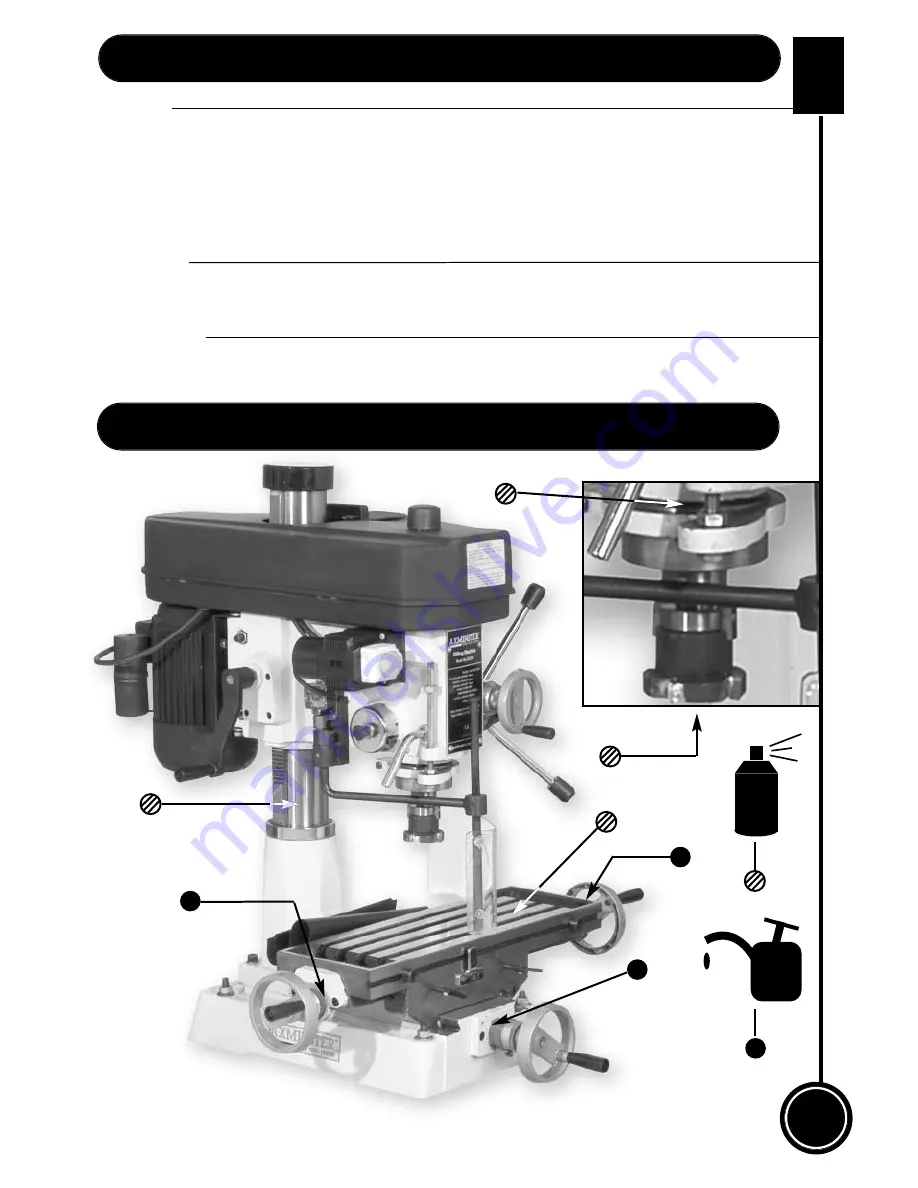
W H I T E
A X M I N S T E R
W
21
Maintenance (Continued)...
Monthly
a) Check the belt tensions. If necessary reset the belt tensions by loosening the two swing arm
clamping bolts, retension the belts and re-secure the bolts.
b) Give the motor a good ‘blow through’ to remove any dust, dirt etc,
c) Check all the interlocks function correctly.
d) Check the greasing of the quill in the sleeve.
6 Monthly
When checking the belt tensions, slip off the belts and check and if necessary lubricate the
jockey pulley tower bearings.
Accessories
There are numerous accessories listed for the machine listed in the Axminster catalogue
in section 1.
Oil
OIL
Mill/Drill Oiling Points...
Summary of Contents for ZX25M
Page 22: ...22 W H I T E AXMINSTER W Mill Drill Oiling Points Continued www axminster co uk Oil OIL ...
Page 24: ...24 W H I T E AXMINSTER W Parts Breakdown ...
Page 25: ...W H I T E AXMINSTER W 25 Parts Breakdown FREEPHONE 0800 371822 ...
Page 26: ...26 W H I T E AXMINSTER W www axminster co uk Parts LIst ...
Page 27: ...W H I T E AXMINSTER W 27 Parts List FREEPHONE 0800 371822 ...