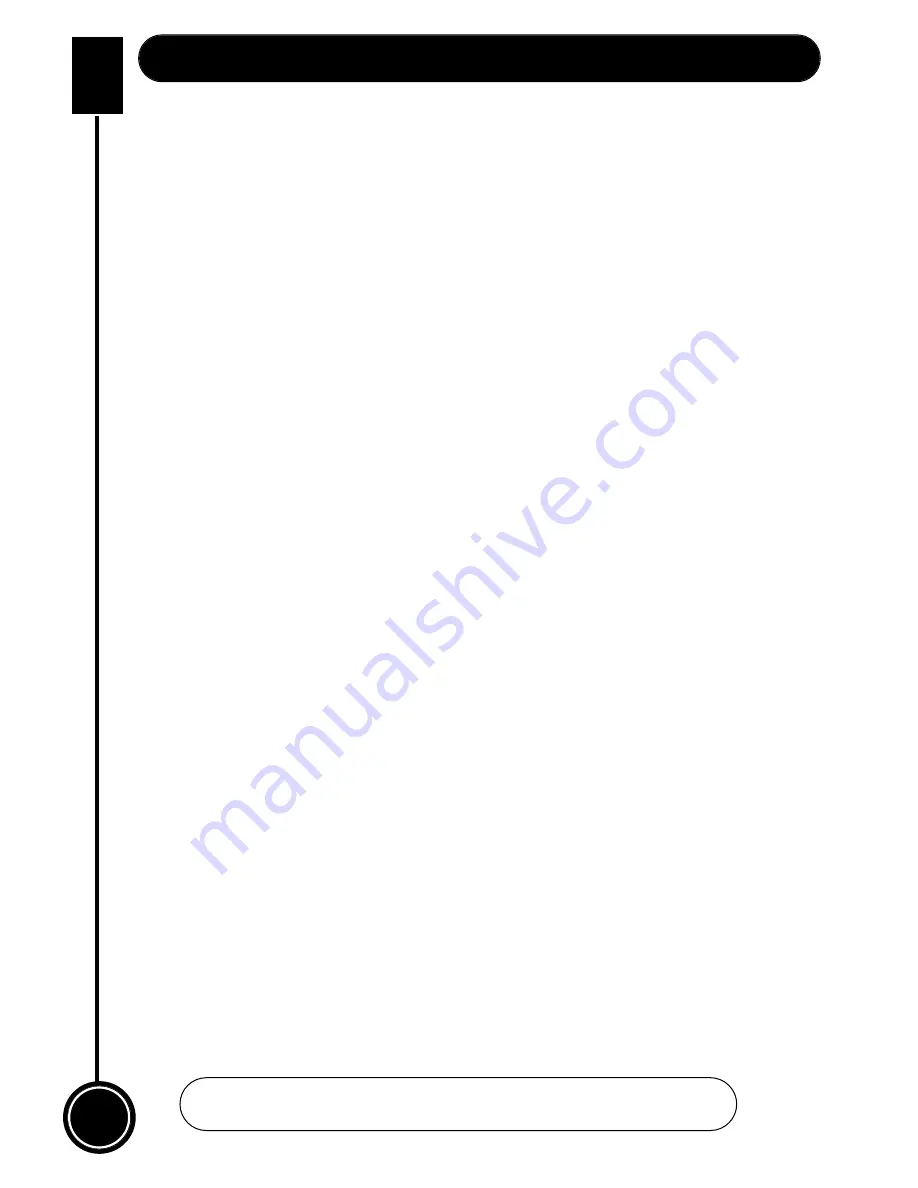
16
W H I T E
A X M I N S T E R
W
Identification and Parts Description...
www.axminster.co.uk
Guide fence
The clamping action is such that both the front and rear of the guide are
(Continued)
clamped to the table, ensuring that the guide fence is held rigidly during
the cutting operation.
Table stabilising
When the table was cast it was a pretty stable lump, however,
bolt and
weathering, machining, drilling and boring etc set up varying
butterfly nut
stresses in the table which, if given the opportunity, (like with a long
slot cut across more than half its width) will cause the table to ‘move’. To
counteract this possibility a small housing is machined at the front of
the slot into which the stabilising bolt is fitted and clamped with the
butterfly nut. This ensures that the two most vulnerable parts of the
casting are clamped together in a single plane, to prevent warping and
twisting (Unseen).
Mitre fence
The mitre fence slide can be engaged in the slot in the saw table,
and acts as an X-feed device, which will enable any angle from right
to 45 degrees left or right to be cut with the saw (See Fig 6).
Tracking control
The tracking control star knob, at the rear of the top compartment, is
star knob
connected to a threaded rod that is engaged in a threaded hole in the
mounting bracket of the upper saw wheel axle assembly. The end of the
rod pushes against the lower end of the hinged tilting plate that carries
the upper saw wheel axle. Driving the rod in or out will cause the plate
to tilt, and by association, the upper saw wheel, thus enabling the blade
to be ‘tracked’. The tilting plate is kept in contact with the end of the
threaded rod by the tension on the saw blade, (the downward ‘pull’). It
should be self-evident therefore, that the blade can only be ‘tracked’
whilst it is in tension.
Tracking control
A butterfly nut that locks the tracking control in position once correct
lock
tracking has been established (See Fig 2).
Lower saw
The lower saw wheel and integral pulley wheel is likewise mounted on
wheel
double bearings, onto an axle that is housed in an adjusting ‘box trap’
mounting. This box trap is used to set the Lower Saw Wheel to DATUM.
It is the base parameter that the rest of the saw is set against. It is highly
recommended that, except in the most dire of circumstances, you
DO
NOT ALTER
the factory setting.
Motor clamping
The drive belt is tensioned by turning the motor against a fixed point,
bolt slot
pulling the belt tight and then locking the motor in position with its
clamping bolt. During the turning operation the clamping bolt moves
within the slot that is machined into the motor mounting flange plate.
Dust extraction
An 80mm diameter dust extraction outlet (See Fig 2 Backview).
outlet
On/Off Button
The On/Off buttons, controlling an NVR switch. The green ‘I’ is the ‘on’
and switch
button, the red ‘O’ is the off button (See Fig 1 Front view).
shroud
Summary of Contents for AWHBS250N
Page 26: ...26 W H I T E AXMINSTER W Parts Breakdown for the Bandsaw ...
Page 27: ...W H I T E AXMINSTER W 27 Parts List for the Bandsaw FREEPHONE 0800 371822 ...
Page 28: ...28 W H I T E AXMINSTER W Parts List for the Bandsaw www axminster co uk ...
Page 29: ...W H I T E AXMINSTER W 29 Parts List Breakdown for the Fence FREEPHONE 0800 371822 ...
Page 30: ...30 W H I T E AXMINSTER W Parts List Breakdown for the Cabinet www axminster co uk ...
Page 31: ...W H I T E AXMINSTER W 31 Notes FREEPHONE 0800 371822 ...