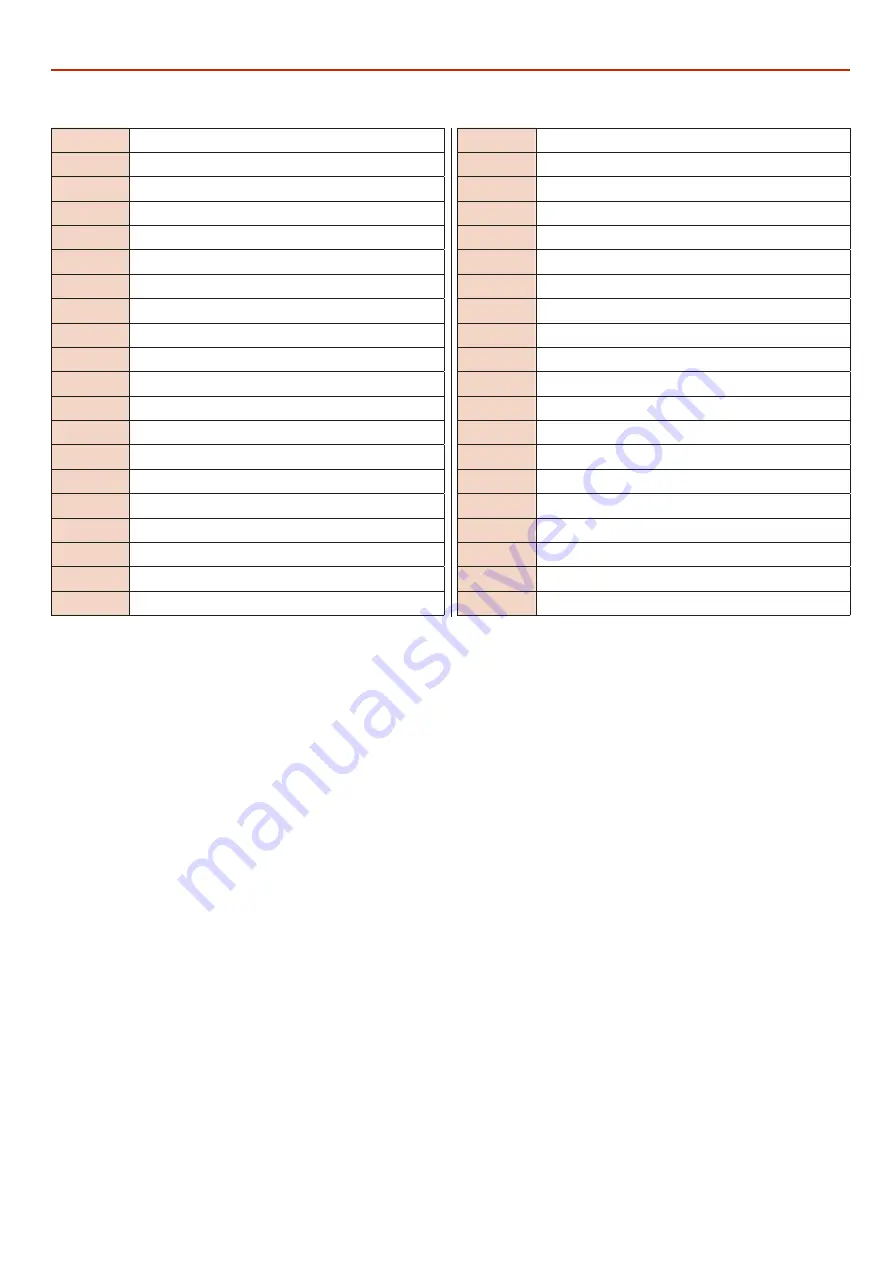
Exploded Diagram/Parts List
41
Diagram/List A
No
Description
A-1
Sliding Panel Set
A-2
Hex Head Screw M10x55
A-3
Washer 10mm
A-4
Hex Nut M10
A-5
Washer 6mm
A-7
Access Panel
A-8
Pan Head Screw M6X12
A-9
Guard
A-10
Pan Head Screw M6x30
A-11
Spacer
A-12
End cap
A-13
Side Plate
A-14
“L” Plate
A-15
Pan Head Screw M5x10
A-18
Limit switch QKS7
A-19
Pan Head Screw M4x30
A-22
Plate
A-23
Box Stand
A-24
Pan Head Screw M6x12
A-25
Washer 6mm
A-26
Dust Port
A-27
Strain Relief
A-28
Switch Box
A-29
Sealer
A-30
Cover Switch Box
A-31
Washer 4mm
A-32
Pan Head Screw M4x12
A-33
Rubber Seal
A-34
Main Switch
A-35
Taping Screw ST4.2x20
A-36
Pan Head Screw M5x16
A-37
Washer 5mm
A-38
Hex Nut M5
A-39
Emergency Stop Lever
A-40
Push Stick
A-41
Holder Push Stick
Summary of Contents for 101256
Page 1: ...PS315 1600mm Panel Saw Code 101256 Original Instructions AT M 21 06 2018 BOOK REF 101882 ...
Page 4: ...What s Included 4 1 3 4 6 8 5 7 2 ...
Page 5: ...What s Included 5 10 9 11 12 13 15 16 17 14 ...
Page 6: ...What s Included 6 B C D E G F H I J 18 19 20 21 22 23 24 23 Box inside the machine ...
Page 40: ...Exploded Diagram Parts List 40 Diagram List A ...
Page 42: ...Exploded Diagram Parts List 42 Diagram List B ...
Page 44: ...Exploded Diagram Parts List 44 Diagram List C ...
Page 46: ...Exploded Diagram Parts List 46 Diagram List D ...
Page 48: ...Exploded Diagram Parts List 48 Diagram List E ...
Page 50: ...Exploded Diagram Parts List 50 Diagram List F ...
Page 52: ...Wiring Diagram 52 Single Phase ...
Page 53: ...Notes 53 ...
Page 54: ...Notes 54 ...
Page 55: ...Notes 55 ...