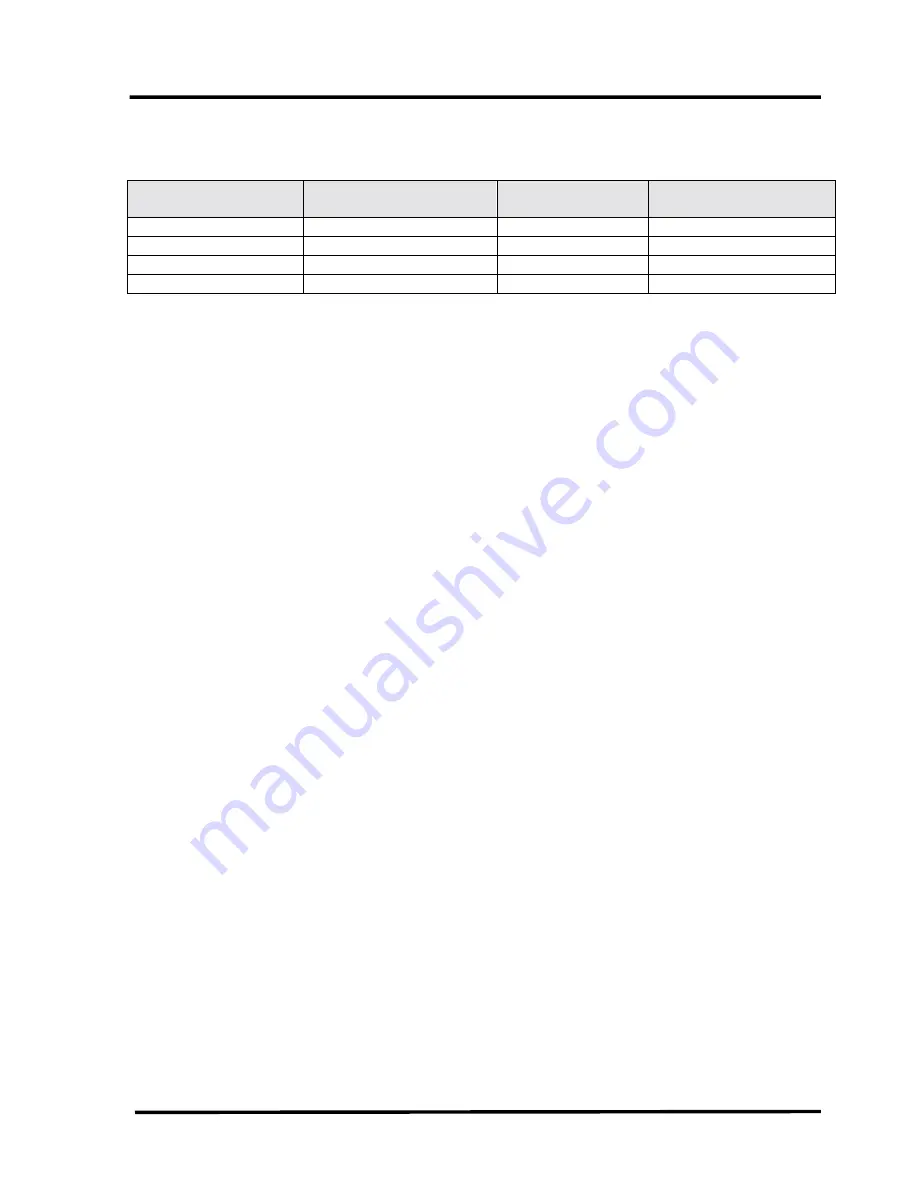
LX Series Digital
Chapter 2, Amplifier Assembly Description,
Power Amplifier Assembly
Maintenance & Remote Control Connections
Volume 2, Rev. 1
2-4
2.1.2 System Configurations
Table 2-1: Typical LX Series Digital System Configuration Drawings and Parts Lists
DIGITAL SYSTEM
CONFIGURATIONS
INTERCONNECT
RACKING PLAN
PARTS LIST
125W 1303940
1303596
1303913
250W 1303940
1303596
1303893
500W 1303940
1303596
1303894
1 kW
1303941
1303596
1303895
NOTE: Refer to Table 2-1 for the
Interconnect, Racking Plan and Parts
List Numbers for your system. The
actual drawings and parts lists are
located in Appendix B of this manual.
A Drawing List of the order the
drawings appear in the Appendix is
found at the beginning of the section.
2.1.2.1 125 Watt, 250 Watt or 500W
Digital Output System Configurations
In a 125 Watt digital system, the output
of the (A3) power amplifier chassis
assembly at the 7/16” connector J203 is
cabled to (A9) the bandpass filter for the
system. In a 250 Watt or 500W digital
system, the output of the (A3) power
amplifier chassis assembly at the 7/16”
connector J205 is also cabled to the (A9)
bandpass filter. The filtered output
connects either directly to (A11) the
output coupler or first to the Optional 1
section or 2 section trap filter if more
filtering is needed and then to the output
coupler. The (A11) coupler assembly
supplies a forward and a reflected power
samples to the (A4) Dual Peak Detector
Board. The Dual Peak Detector Board
supplies reflected and forward output
power samples to the exciter/driver for
metering purposes. The reflected sample
connects to TB31-13 and the forward
sample at TB31-14. The RF output for the
transmitter is at J2 the 7/8” EIA connector
on the (A11) coupler assembly.
2.1.2.2 1 kW Digital Output System
Configuration
In a 1 kW digital system, the output of the
(A3) and the (A6) power amplifier chassis
assemblies, at the “7/16” connectors
J205, are cabled to (A7) the hybrid
combiner for the system, mounted to the
input of the bandpass filter. A 500 Watt
reject load (A9) connects to J4 on the
hybrid combiner to dissipate reject
power. A thermal switch (A9-A1) is
mounted to the reject load and supplies
an overtemperature fault, at 175º F., to
the driver assembly, at TB30-7 & TB30-
15, if a problem occurs in the output
lines.
NOTE:
If an overtemperature fault
occurs, it must be manually reset on the
system controller after repairs are made.
The combined output of the hybrid
combiner at the “7/8” Jack J3 is
connected to J1 on the digital bandpass
filter. The filtered output of the bandpass
filter is connected to (A14) the low pass
filter assembly. The output of the filter is
either cabled directly to the (A11) output
coupler or first to an optional 1 or 2
section trap filter and then to the output
coupler. The (A11) coupler assembly
supplies a forward and a reflected power
samples to the (A4) Dual Peak Detector
Board. The Dual Peak Detector Board
supplies reflected and forward output
power samples to the exciter/driver for
metering purposes. The reflected sample
connects to TB31-13 and the forward
sample at TB31-14. The RF output for
the transmitter is at J2 the 7/8” EIA
connector on the (A11) coupler
assembly.
2.1.2.3 1.5 kW Digital Output System
Configuration
In a 1.5 kW system, the outputs of A3,
A6 and A13 power amplifier chassis
assemblies, at the “N” connectors J205,
are cabled to (A7) the hybrid combiner
for the system mounting facing the rear