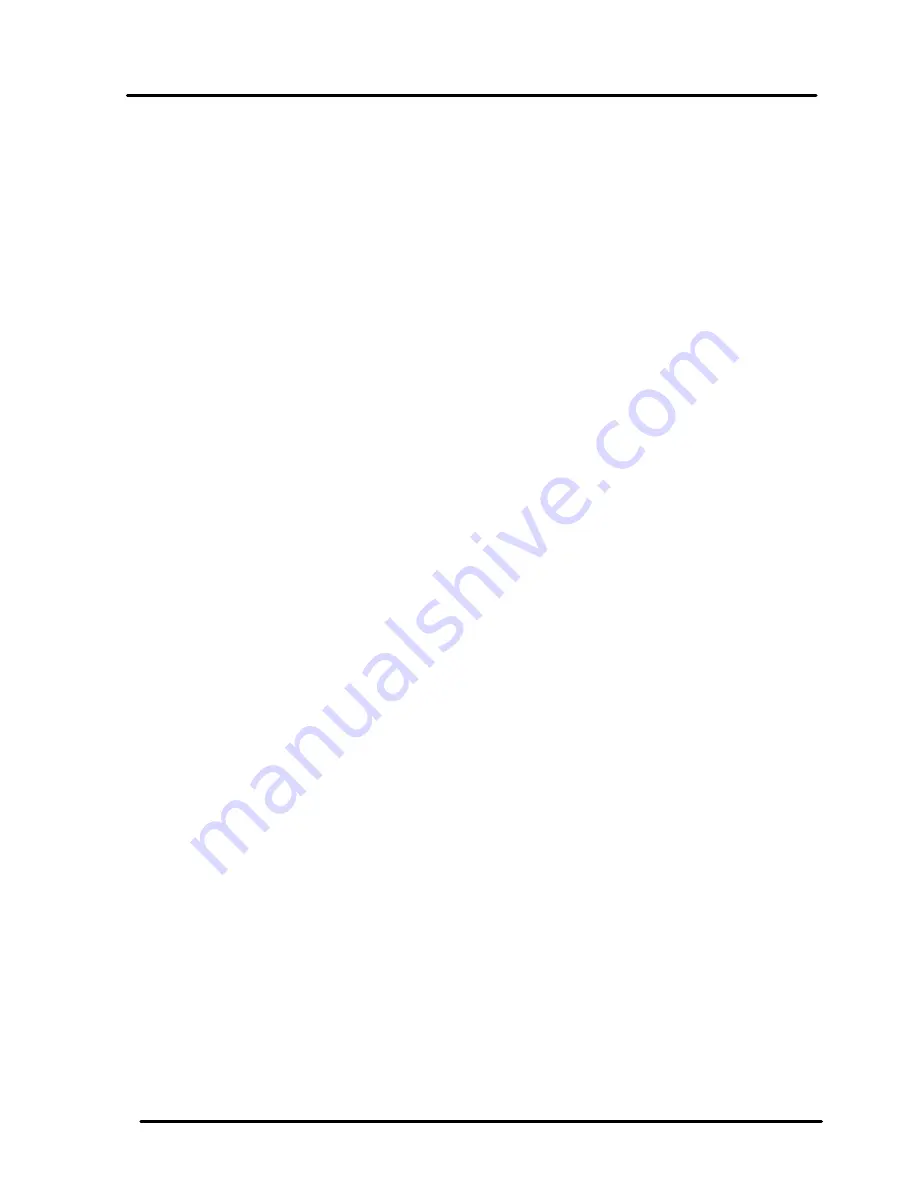
350-Watt Digital VHF LB Transmitter
Chapter 2, System Description, Maintenance &
Remote Control Connections
DT325B, Rev. 0
2-8
on the Controller Module. Since RF
performance of the transmitter requires
different hardware for different
frequency bands, not all frequency
configurations are valid for a specific
transmitter. The Power detectors in the
transmitter are frequency dependent,
therefore the detectors of the power
amplifiers are calibrated at their
frequency of use. The detectors for
System RF monitoring are also
calibrated at the desired frequency of
use.
2.6: Maintenance
The Transmitter is designed with
components that require little or no
periodic maintenance except for the
routine cleaning of the fans and the front
panels of the modules and the periodic
check of general tightness of hardware.
It is recommended that periodically, the
time interval depends on the amount of
movement the cabinet receives, all
mounting hardware, holding tray slides,
shelving and mounting plates inside the
cabinet are checked for tightness. All
screws and bolts that are accessible
should be tightened initially when the
transmitter is received and periodically
thereafter if the transmitter is moved by
vehicle. All coaxial connectors, hard-line
connections and hardware holding
combiners, splitters, or any other
mounted items should be checked and
tightened. Check the front panel
thumbscrews that hold the Exciter/Driver
Sleds, Amplifier Module and Power
Supply Sleds in place are tight. This is
especially important after the transmitter
has been transported.
The amount of time between cleanings
depends on the conditions within the
transmitter room. While the electronics
have been designed to function even if
covered with dust, a heavy buildup of
dust, dirt, or insects will affect the
cooling of the components. This could
lead to a thermal shutdown or the
premature failure of the affected
modules.
When the front panels of the modules
become dust covered, the top covers
should be taken off and any accumulated
foreign material should be removed. A
vacuum cleaner, utilizing a small, wand-
type attachment, is an excellent way to
suction out the dirt. Alcohol and other
cleaning agents should not be used
unless you are certain that the solvents
will not damage components or the silk-
screened markings on the modules and
boards. Water-based cleaners can be
used, but do not saturate the
components. The fans and heatsinks
should be cleaned of all dust or dirt to
permit the free flow of air for cooling
purposes.
It is recommended that the operating
parameters of the amplifier assembly and
transmitter be recorded from the LEDs on
the modules and the LCD system
metering on the control/monitoring
module at least once a month. It is
suggested that this data be retained in a
rugged folder or envelope.
2.6.1: Module Replacement
Module replacement on the products is a
relatively simple process. All modules
plug directly into the backplane board
except for the power amplifier module,
and in higher power units, the power
supply and power amplifier modules,
which plug into a blind mating
connector.
To replace a module, refer to the
following procedure. Loosen the two grip
lock connectors, located on the front
panel, at the top and bottom of the
module, counterclockwise until the
module releases. The Downconverter,
Upconverter and the Controller/Power
Supply can then be gently pulled from
the unit. After removal of the failed
module, slide the replacement module in
place and make certain it connects to the
backplane board. If the replacement