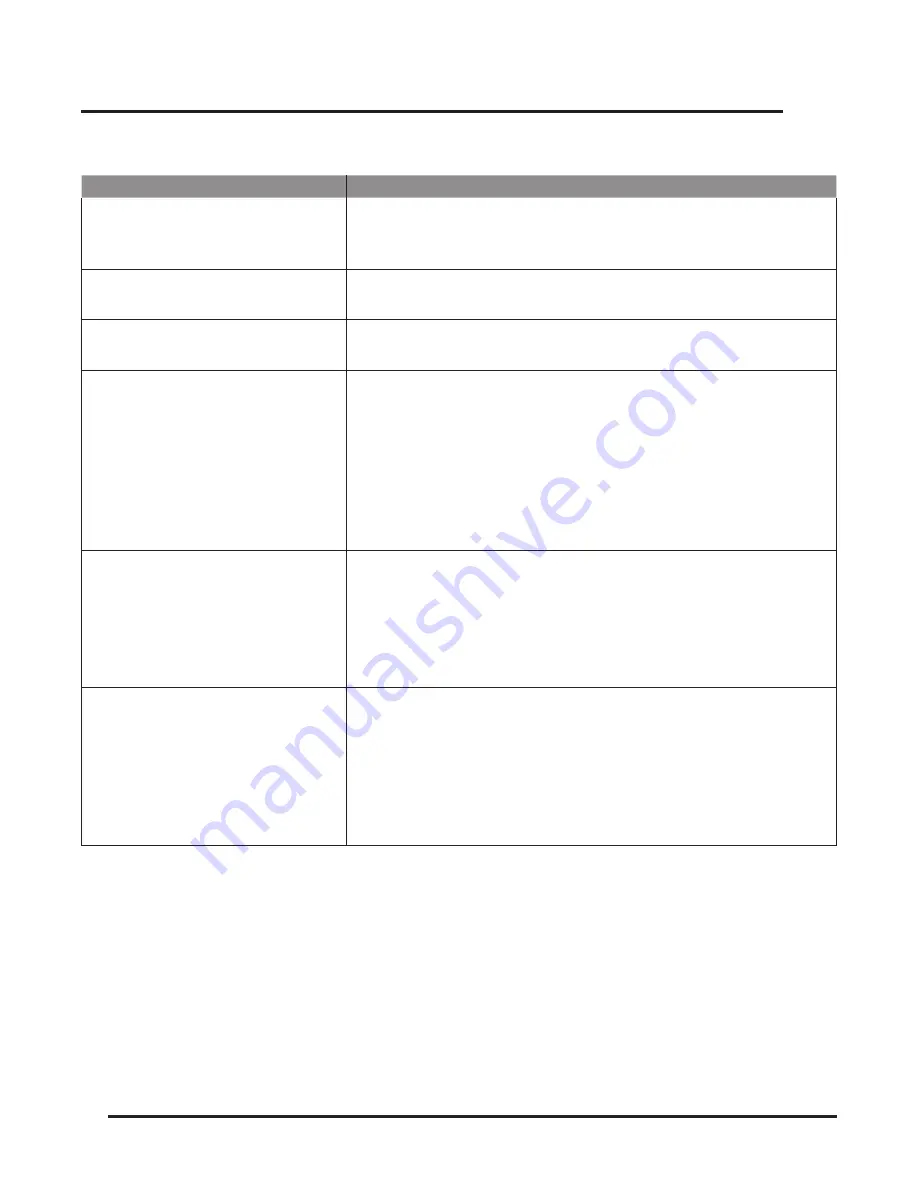
10
Before Calling for Service
Issue
Possible Cause / Solution
The range hood doesn't turn on
• Check if the range hood is plugged in. Make sure that all
power is turned ON, the fuse isn't blown and all electrical
wirings are properly connected.
The range hood turns on but the
LED light doesn't
• Replace the defective LED assembly. Refer to Range Hood
Care section for instructions.
The range hood vibrates when
the blower is on
• Check and tighten the mounting screws to secure the hood
to the cabinet or wall properly.
The blower or fan seems weak
• Check that the duct size used is at least 6” or 3-1/4 x 10”.
Range hood WILL NOT function efficiently with insufficient
duct size. For example: 6” duct over 7” top vent and not
sealed properly.
• Check if the duct is clogged or the damper (half-circular
flapper) is not installed correctly or opening properly. A tight
mesh on a side wall cap might also cause restriction to the
air flow.
The lights work but the blower is
not spinning at all or is rattling
• The blower might be jammed or scraping the bottom due to
shipping damage.
• Disconnect the power cord, remove the fan grill and the fan
blade, might see the fan blade or/and motor is not in the
proper position (offset from the center). Try to fix/adjust it or
please contact us immediately.
The hood is not venting out
properly
• Make sure the distance between the stove top and the
bottom of the hood is within recommended 24” and 30” in
distance. *Due to different ceiling height configurations, the
recommended height may not be applicable.
• Reduce the number of elbows and length of duct work.
Check if all joints are properly connected, taped and sealed.
• Make sure the power is on high speed for heavy cooking.
Range
Hood
Troubleshooting