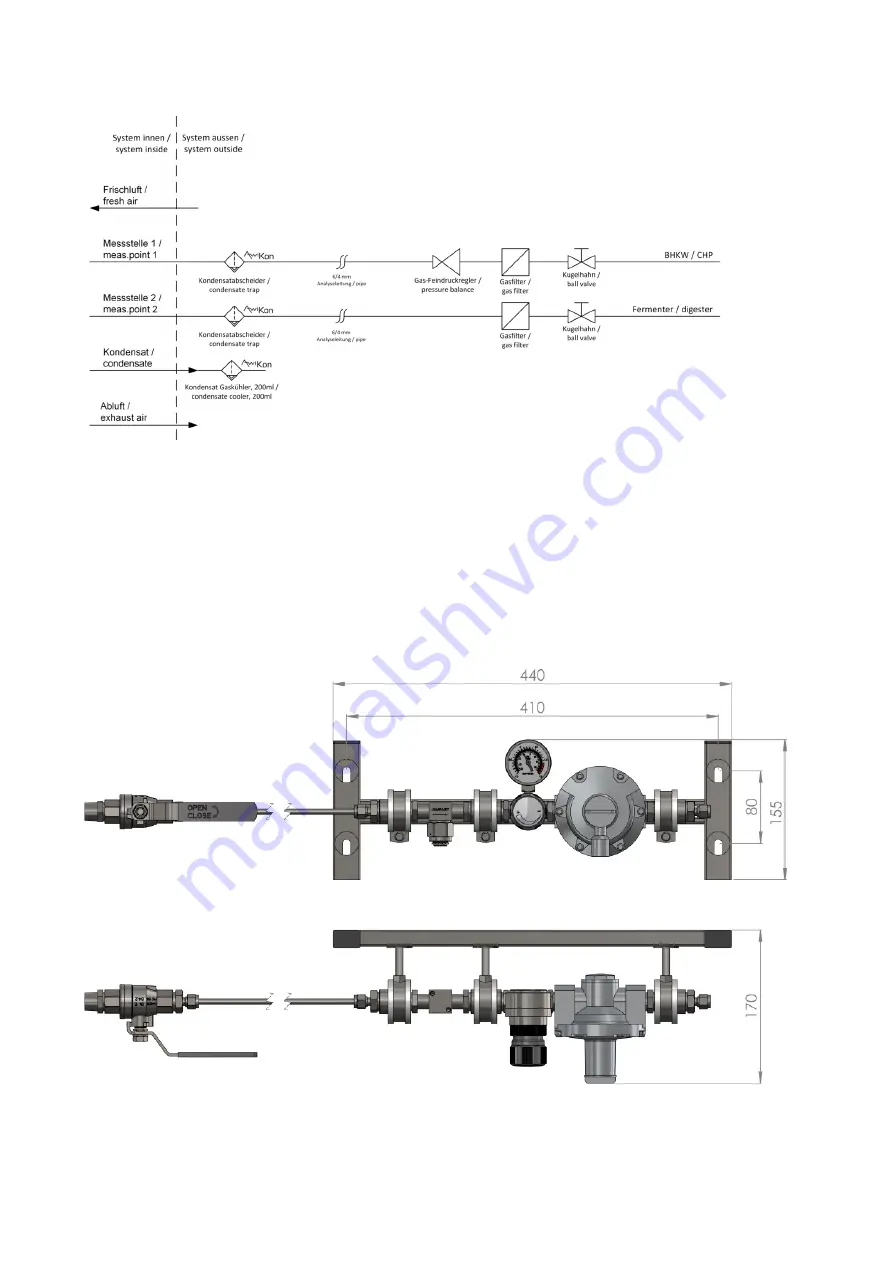
Preparing the Gas Analysis System for Use
Figure 6: Schematic layout of the extraction points for analysis gas – Exemplary
representation
5.2.6.1.2
Gas extraction fitting up to 16bar (PN16)
For gas extraction from pipes with system pressures between 400mbar and 16bar relative overpressure,
the gas extraction fitting 16bar (PN16) is used. The fitting is designed for indoor installation.
Figure 7: Gas extraction fitting 16bar (PN16) with particle filter (optional)
31